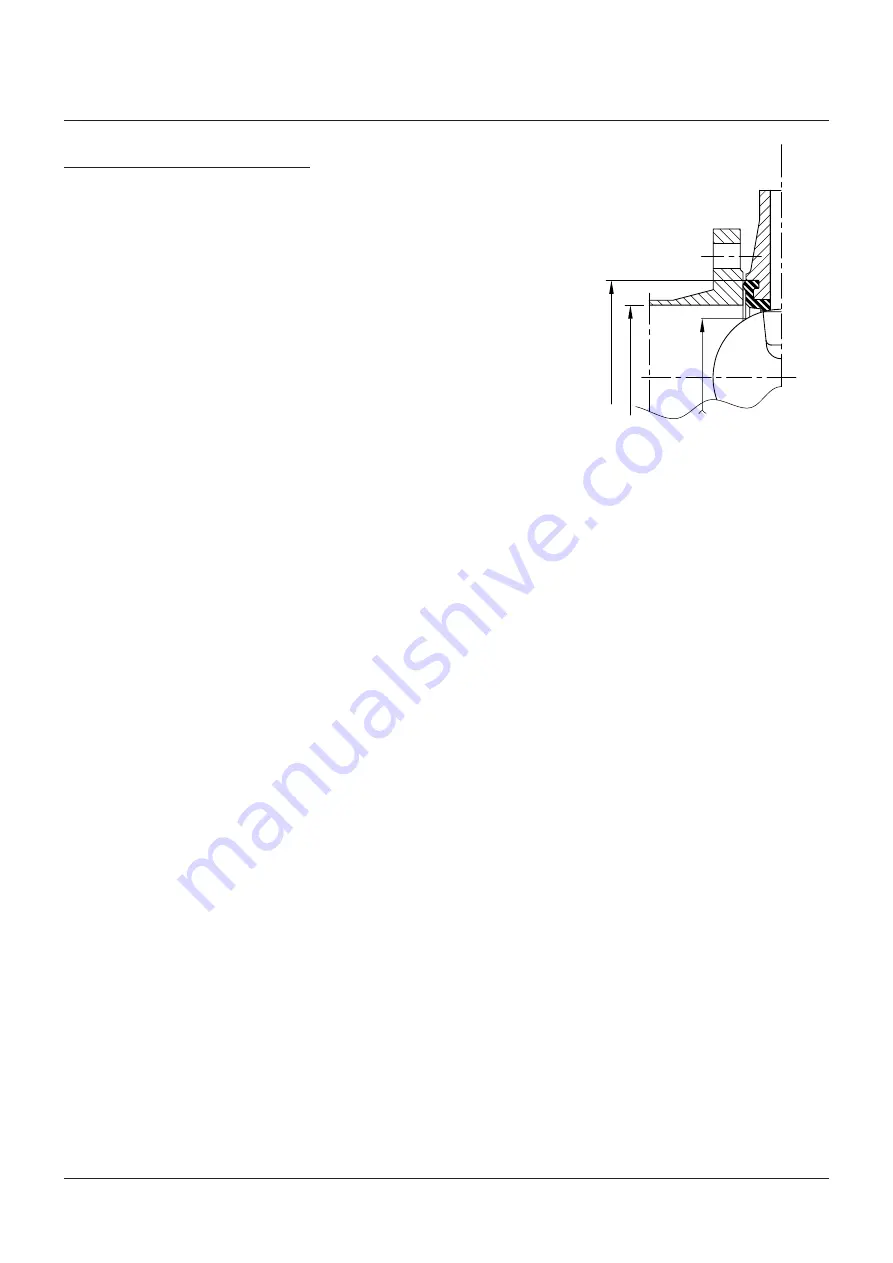
2
KEYSTONE
OPTISEAL F14/16 - 15/17 AND BREWSEAL BUTTERFLY VALVES
INSTALLATION AND MAINTENANCE INSTRUCTIONS
3 INSTALLATION
WARNING!
For safety reasons, it is important to take the
following precautions before you start work on
the valve:
1. Personnel making any adjustments to
the valves should utilize suitable equipment.
All required personal protection means
should be worn.
2. The line must be depressurized before
installing the valve.
3. Installation and handling of valves should be
done only by personnel that is trained in all
aspects of manual and mechanical handling
techniques.
4. Misuse of the valve is not allowed.
For example: the valve, handles, actuators or
other parts may not be used as ‘climbing tools’.
5. Ensure that valve pressure/temperature
limitations marked on the identification tag
are within the service conditions. The trim
number on the valve’s tagplate identifies
the valve materials. See Product Manual for
valve specific P/T diagram and trim number
definition.
6. Ensure that valve materials are compatible
with the pipeline fluid.
7. For DVGW-Gas approved lugged valves,
through threaded rods must be used instead
of flange bolts.
YY
D max./min.
Q
3.1 Visual valve inspection
1. Confirm that the materials of construction
listed on the valve nameplate are
appropriate for the service intended and
are as specified.
2. Tag/name plate identification
Manufacturer:
Keystone
Fig.:
e.g. OptiSeal 14-112
JOB:
Job number
Nominal size:
DN
M.P.W.P.:
maximum permissible
working pressure
Flange compatibility: e.g. PN 10/16
Temperature:
e.g. -40/120°C
Body:
e.g. GJL 250.
3.2 Flange and pipe compatibility
Check matching of flange drilling pattern
of valve and pipe before assembly.
Flanges have to meet the following
requirements:
- The face inside diameter should be:
D min.: the valve Q-dim adequate
disc clearance.
D max.: the optimum inside diameter (ID)
is equal to the inside diameter of flange
standard EN 1092-1, table 8, type 11.
For larger than D max inside diameters or
other flange types please contact your local
Emerson Sales organization, as larger inside
diameters might result in reduced valve
functionality.
Do not use flange gaskets, these lead to
valve damage!
3.3 Valve installation
The valves are bi-directional and may be
fitted in either direction relative to the flow.
The valve will control flow equally in either
direction. The recommended installation
position is shaft horizontal and the lower disc
edge opening down-stream. (Especially for
slurry service and media with a tendency for
sedimen tation). For optimum valve control and
smooth performance, it is recommended to
have a 10 to 20 pipe diameters of straight run
inlet piping and 3 to 5 pipe diameters straight
outlet piping.
A valve is no crow-bar. Do not use the valve
to spread the flanges. Seat damage might be
the result.
- If the flange (or pipe) is provided with a
raised face, the diameter of this shall be at
least 8 mm larger than the YY-dimension of
the valve.
The use of the flange-gaskets is not allowed
since it might damage the valve.
The Keystone seat-face design eliminates
the need for the gaskets.
Use flange bolting in agreement with
appropriate standard.