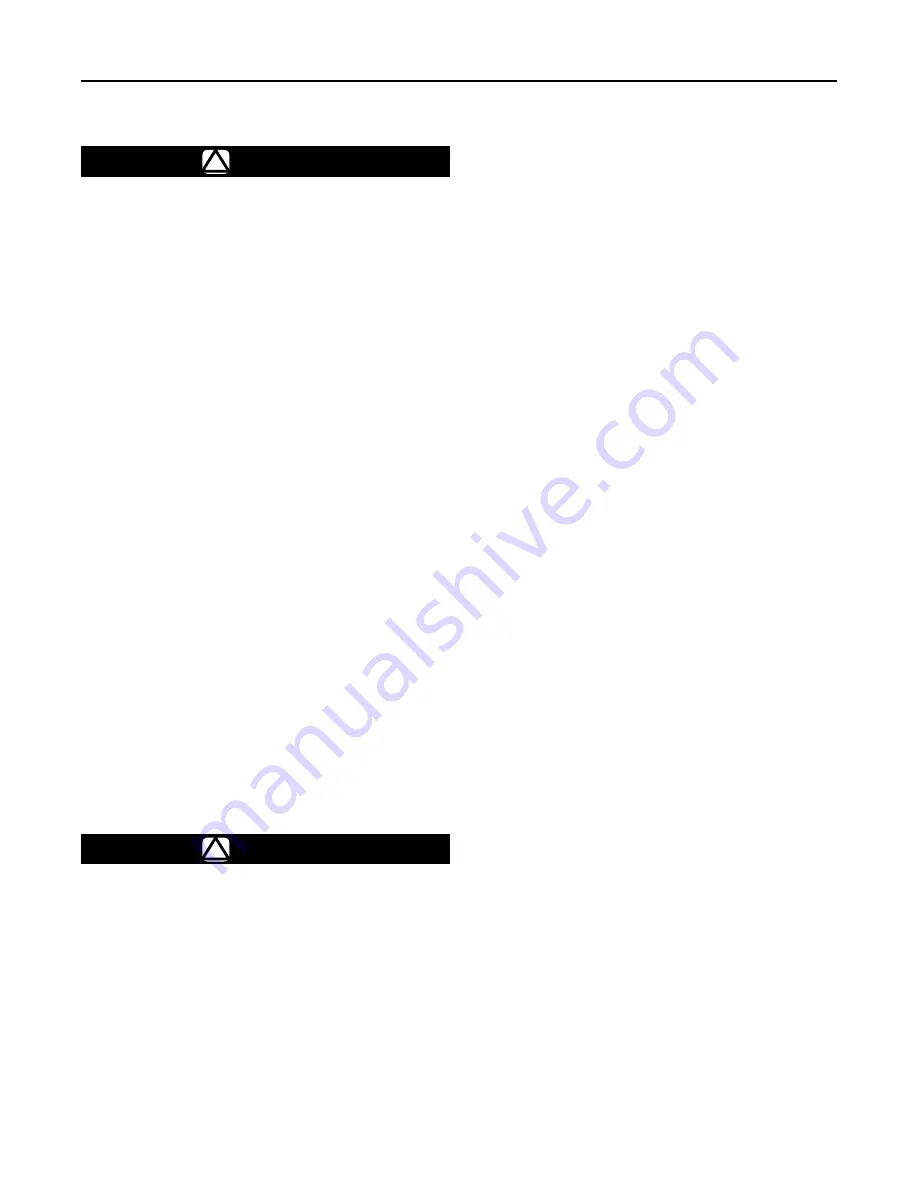
T208VR Series
4
installation
Warning
!
Personal injury, property damage,
equipment damage or leakage due to
escaping gas or bursting of pressure-
containing parts may result if this
equipment is overpressured or is
installed where service conditions
could exceed the limits given in the
Specifications or where conditions
exceed any ratings of the adjacent piping
or piping connections. To avoid such
injury or damage, provide pressure-
relieving or pressure-limiting devices
(as required by the appropriate code,
regulation or standard) to prevent
service conditions from exceeding
those limits.
additionally, physical damage to this
equipment could cause personal injury
or property damage due to escaping
gas. To avoid such injury or damage,
install the equipment in a safe and well
ventilated location.
note
if this equipment is shipped mounted on
another unit, install that unit according to
the appropriate instruction manual.
1.
Only personnel qualified through training and
experience shall install, operate and maintain this
equipment. For T208VR Series equipment that
is shipped separately, make sure that there is no
damage to or foreign material in it. Also ensure that
all tubing and piping have been blown free.
Warning
!
This equipment may vent some gas to the
atmosphere. In hazardous or flammable
gas service, vented gas may accumulate
and cause personal injury, death or
property damage due to fire or explosion.
Vent equipment in hazardous gas service
to a remote, safe location away from air
intakes or any hazardous area. The vent
line or stack opening must be protected
against condensation or clogging.
2. This equipment may be installed in any position as
long as the flow through the body is in the direction
indicated by the arrow attached to the body. If
continuous operation is required during inspection
or maintenance, install a threeway bypass valve
around the equipment.
3.
To keep the vent assembly (key 26) from being
plugged or the spring case (key 3) from collecting
moisture, corrosive chemicals or other foreign
material, point the vent down or otherwise protect
it. The diaphragm casing (key 4,Figure 6) may be
rotated in order to obtain desired positioning.
4. To remotely vent the regulator, remove the vent
assembly (key 26) and install obstruction-free
tubing or piping into the 1/4 NPT vent tapping.
Provide protection on a remote vent by installing
a screened vent cap into the remote end of the
vent pipe. If continuous operation of the system is
required during inspection or maintenance, install a
three-way bypass valve around the regulator.
5.
The Type T208VRM requires a control line. Be sure
to install the control line before putting the regulator
into operation. Make the control line as short and
straight as possible and do not install it in a location
where flow may be turbulent. Significant restrictions
in the control line can prevent proper pressure
registration. When using a hand valve, it should
be a full flow valve, such as a full port ball valve.
Install the control line sloping downward toward the
tank to prevent condensation buildup and avoid low
points (or traps) that could catch liquid. The sensing
line must enter the tank above the liquid level at a
point that senses the vapor space pressure and is
free from turbulence associated with tank nozzles
or vents. The control line pipe should be at least
1/2-inch / 13 mm in diameter and increase 1 pipe
size for every 10 feet / 3.05 m of control line, with
setpoint less than 5-inches w.c. / 12 mbar.