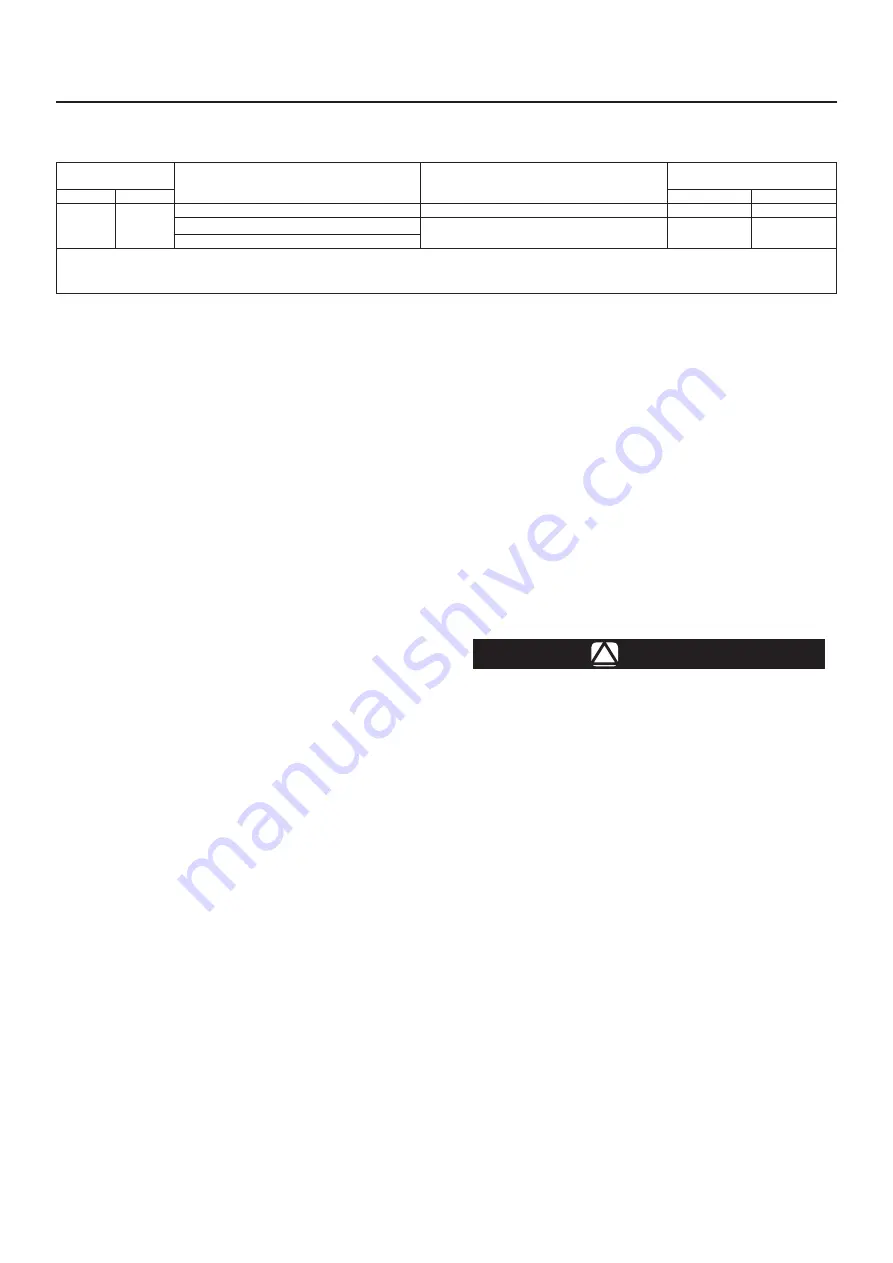
For flanged bodies, use suitable line gaskets and approved
piping and bolting practices. Install the regulator in any
position desired
(2)
, unless otherwise specified, but be sure
flow through the body is in the direction indicated by the
arrow on the body.
Note
It is important that the regulator be installed
so that the vent hole in the spring case
is unobstructed at all times. For outdoor
installations, the regulator should be located
away from vehicular traffic and positioned
so that water, ice and other foreign materials
cannot enter the spring case through the vent.
Avoid placing the regulator beneath eaves
or downspouts, and be sure it is above the
probable snow level.
Overpressure Protection
T205 Series regulators have an outlet pressure rating lower
than the inlet pressure rating. The recommended pressure
limitations are stamped on the regulator nameplate. Some
type of overpressure protection is needed if the actual inlet
pressure can exceed the maximum operating outlet pressure
rating. Common methods of external overpressure protection
include relief valves, monitoring regulators, shut-off devices
and series regulation. Overpressuring any portion of the
regulators beyond the limits in the Specifications section
may cause leakage, damage to regulator parts or personal
injury due to bursting of pressure-containing parts.
Regulator operation below the maximum pressure limitations
does not preclude the possibility of damage from external
sources or debris in the line. The regulator should be
inspected for damage after any overpressure condition.
Startup
The regulator is factory set at approximately the midpoint
of the spring range or the pressure requested, so an initial
adjustment may be required to give the desired results.
With proper installation completed and relief valves properly
adjusted, slowly open the upstream and downstream
shutoff valves.
Adjustment
To change the control pressure, perform the
following procedure.
For internal flat circular adjusting screw:
1.
Remove the closing cap (key 22).
2. Use a 25 mm / 1 in. hex rod or flat screwdriver to turn
the adjusting screw (key 35) either clockwise to increase
control pressure or counterclockwise to decrease
control pressure. The regulator will go into immediate
operation. To ensure correct operation, always use a
pressure gauge to monitor the tank blanketing pressure
when making adjustments.
3.
After making the adjustment, replace the closing cap
gasket (key 25) and install the closing cap (key 22).
For external square head adjusting screw:
1.
Loosen the locknut (key 20).
2. Turn the adjusting screw (key 35) either clockwise
to increase control pressure or counterclockwise to
decrease control pressure. Always use pressure gauge
to monitor the tank blanketing gas pressure when
making adjustments.
3. After making the adjustment, tighten the locknut (key 20).
Taking Out of Service (Shutdown)
!
WArNINg
To avoid personal injury resulting from sudden
release of pressure, isolate the regulator from
all pressure before attempting disassembly.
* Recommended spare part
1. Use for optional external square head adjusting screw assembly recommended for 83 to 172 mbar / 1.2 to 2.5 psig, 0.17 to 0.31 bar / 2.5 to 4.5 psig, and 0.31 to 0.48 bar / 4.5 to 7 psig
spring ranges only.
2. Not available for Types T205H and T205HM.
Parts List
Key Description
1 Body
2
Cap Screw
3
Spring Case
4
Lower Casing
5*
Orifice
6
Spring
7
Diaphragm Head
8
Pusher Post
9*
Diaphragm Gasket
10* Diaphragm
11* Body Seal O-
Ring
12* Insert Seal O-ring
13* Disk Assembly
14
Stem
15* Cotter Pin
16
Lever Assembly
17
Machine Screw
18
Guide Insert
19
Upper Spring Seat
(1)
20
Lock Nut
(1)
22
Closing Cap
23
Hex Nut
24
Spring Case Cap Screw
25* Closing Cap Gasket
26
Vent Assembly
Key Description
27
Pipe Plug (Types T205
and T205H only)
30* Stem Seal O-ring
(Types T205M and
T205HM only)
31* Throat Seal O-ring
(Types T205M and
T205HM only)
32
Pitot Tube (Types T205
and T205H)
34
Machine Screw
(Types T205M
and T205HM only)
35
Adjusting Screw
36
Washer
38
Diaphragm Cap Screw
45* Diaphragm Head Gasket
46
Nameplate
47
Drive Screw
48
Flow arrow (not shown)
49
Backup Ring
50
Lower Spring Seat
51
NACE Tag (not shown)
52
Tag Wire (not shown)
54
Diaphragm Head
(not shown)
Table 1.
Body Sizes, End Connection Styles and Maximum Allowable Inlet Pressures
BODY SIZE
BODY MATERIAL
ENd CONNECTION STylES
(1)
MAxIMuM AllOWABlE ANd
OPErATINg INlET PrESSurE
dN
In.
bar
psig
20 or 25
3/4 or 1
Gray Cast Iron
(2)
NPT
10.3
150
WCC Carbon Steel
NPT, CL150 RF, CL300 RF or PN 16/25/40 RF
13.8
(3)
200
(3)
CF8M/CF3M Stainless Steel
(4)
1. All flanges are welded. Weld-on flange dimension is 356 mm / 14 in. face-to-face.
2. Not available for Types T205H and T205HM.
3. Inlet pressure is limited to 10.3 bar / 150 psig for Types T205H and T205HM.
4. Pipe nipples and flanges are 316 Stainless steel for flanged body assemblies.
T205 Series
2