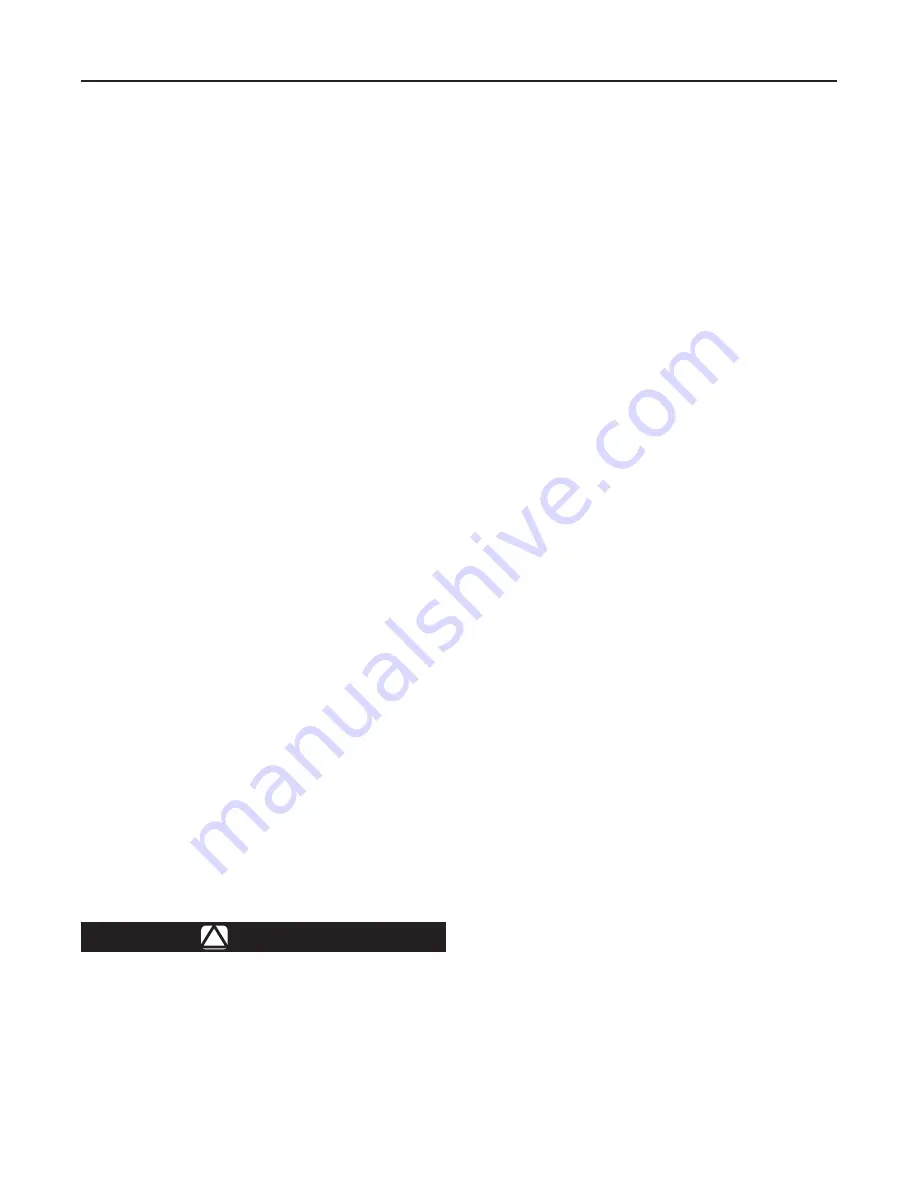
S201 and S202 Series
5
1. Check to see that all appliances are turned off.
2. Slowly open the upstream block valve.
3. Check inlet and outlet pressure for correct values.
4. Check all connections for leaks.
5. Light the appliance pilots.
Adjustment
The range of allowable pressure settings is stamped
on the nameplate. If the required setting is not within
this range, substitute the correct spring (as shown
in Table 3). If the spring is changed, change the
nameplate to indicate the new pressure range.
A pressure gauge should always be used to monitor
downstream pressure while adjustments are being made.
1. Remove the closing cap (key 4, Figure 5) or
loosen the hex locknut.
2. To increase the outlet setting, turn the adjusting
screw (key 3, Figure 5) clockwise. To decrease
the outlet setting, turn the adjusting
screw counterclockwise.
3. Replace the closing cap or tighten the hex locknut.
Shutdown
Installation arrangements may vary, but in any
installation it is important that the valves be opened
or closed slowly and that the outlet pressure be
vented before venting inlet pressure to prevent
damage caused by reverse pressurization of the
regulator. The steps below apply to the typical
installation as indicated.
1. Open the vent valves downstream of the regulator.
2. Slowly close the upstream block valve.
3. Inlet pressure will automatically be released
downstream as the regulator opens in response
to the lowered pressure on the diaphragm.
Maintenance
!
WARNING
To avoid personal injury or equipment
damage, do not attempt any
maintenance or disassembly without
first isolating the regulator from system
pressure and relieving all internal
pressure as described in “Shutdown”.
Regulators that have been disassembled
for repair must be tested for proper
operation before returned to service.
Only parts manufactured by Emerson
Process Management Regulator
Technologies, Inc. should be used for
repairing Fisher
®
regulators. Relight
pilot lights according to normal
startup procedures.
Due to normal wear or damage that
may occur from external sources, this
regulator should be inspected and
maintained periodically. The frequency
of inspection and replacement of parts
depends upon the severity of service
conditions or the requirement of local,
state, and federal rules and regulations.
Disassembly to Replace Diaphragm
1. Remove the closing cap (key 4, Figure 5) or
loosen hex locknut. Turn the adjusting screw
or nut (key 3) counterclockwise to ease
spring compression.
2. For Types S201, S201H, S202, and S202H units,
remove the adjusting screw and spring (key 2).
For Type S201K remove the adjusting screw,
hex locknut, and closing cap (key 4), the upper
spring seat (key 6), and spring (key 2).
3. Remove hex nuts (key 15) and cap screws
(key 14). Separate the upper spring case (key 1)
from the lower casing assembly (key 9).
Note
If disassembling a Type S202 or S202h
regulator, lift the upper spring case
straight up in order to avoid hitting the
stem (key 24).
4. Slide the diaphragm and diaphragm head assembly
(key 7) away from the body (key 21) to unhook the
pusher post (key 8) from the lever (key 10). Lift off
the diaphragm and diaphragm head assembly.
5. Unscrew the cap or reset stem (key 24) which
fastens the lower spring seat (key 6) to the
pusher post to separate the lower spring seat,
diaphragm and diaphragm head assembly, and
pusher post. (The relief valve spring (key 25) will
also have to be removed from Types S202 and
S202H regulators).