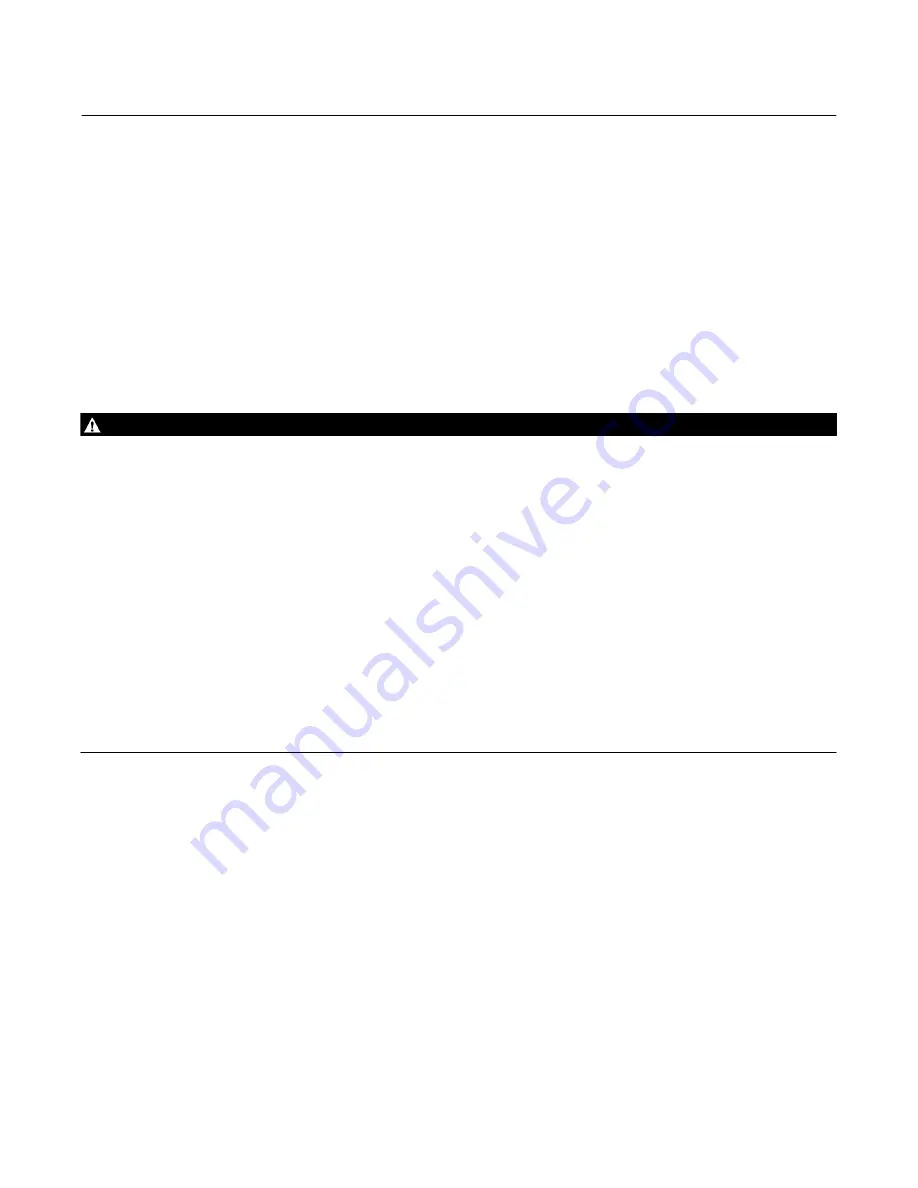
Instruction Manual
D100304X012
656 Actuator
June 2017
4
The actuator spring and diaphragm have been selected to meet the requirements of the application. It should be
noted that the actuator spring has a constant rate of compression and that adjustment of the spring compression
merely shifts the initial spring setpoint up or down to make the actuator travel within the initial spring setpoint and the
maximum diaphragm pressure indicated on the nameplate.
In some instances, however, such as high friction butterfly and ball valves, the actuator will fully stroke with less
diaphragm pressure than indicated on the nameplate. To increase the pressure required to initiate actuator stem
movement, turn the lower bearing seat (key 14) up toward the spring case. To decrease the pressure at which
movement begins, turn the lower bearing seat down, away from the spring case.
Maintenance
WARNING
Avoid personal injury or property damage from sudden release of process pressure or uncontrolled movement of parts.
Before performing any maintenance operations:
D
Do not remove the actuator from the valve while the valve is still pressurized.
D
Always wear protective gloves, clothing, and eyewear when performing any maintenance operations to avoid personal
injury.
D
Disconnect any operating lines providing air pressure, electric power, or a control signal to the actuator. Be sure the
actuator cannot suddenly open or close the valve.
D
Use bypass valves or completely shut off the process to isolate the valve from process pressure. Relieve process pressure
from both sides of the valve. Drain the process media from both sides of the valve.
D
Vent the power actuator loading pressure and relieve any actuatorspring precompression.
D
Use lock‐out procedures to be sure that the above measures stay in effect while you are working on the equipment.
D
The valve packing box may contain process fluids that are pressurized,
even when the valve has been removed from the
pipeline.
Process fluids may spray out under pressure when removing the packing hardware or packing rings, or when
loosening the packing box pipe plug.
D
Check with your process or safety engineer for any additional measures that must be taken to protect against process
media.
Disassembly
1. If the actuator is installed on a control valve, isolate or bypass the control valve.
2. Shut off the diaphragm loading pressure and remove the pipe or tubing from the loading pressure connection in
the top of the diaphragm case.
3. Turn the lower bearing seat (key 14) down, away from the spring case to relieve all spring compression.
4. If the entire actuator is to be removed from its mounting, disconnect the actuator stem (key 10) from the stem
connector, clevis, etc., and remove the jam nuts (key 23). Loosen the cap screws that hold the yoke (key 9) to its
mounting plate or bracket, and lift the entire actuator from its mounting.
5. Remove the diaphragm case cap screws and nuts (keys 19 and 20) and lift the upper diaphragm case (key 1 ) off the
actuator. Remove the diaphragm (key 2).
6. Lift out the diaphragm plate (key 4) and stem (key 10). They may be separated by removing the cap screw (key 3).