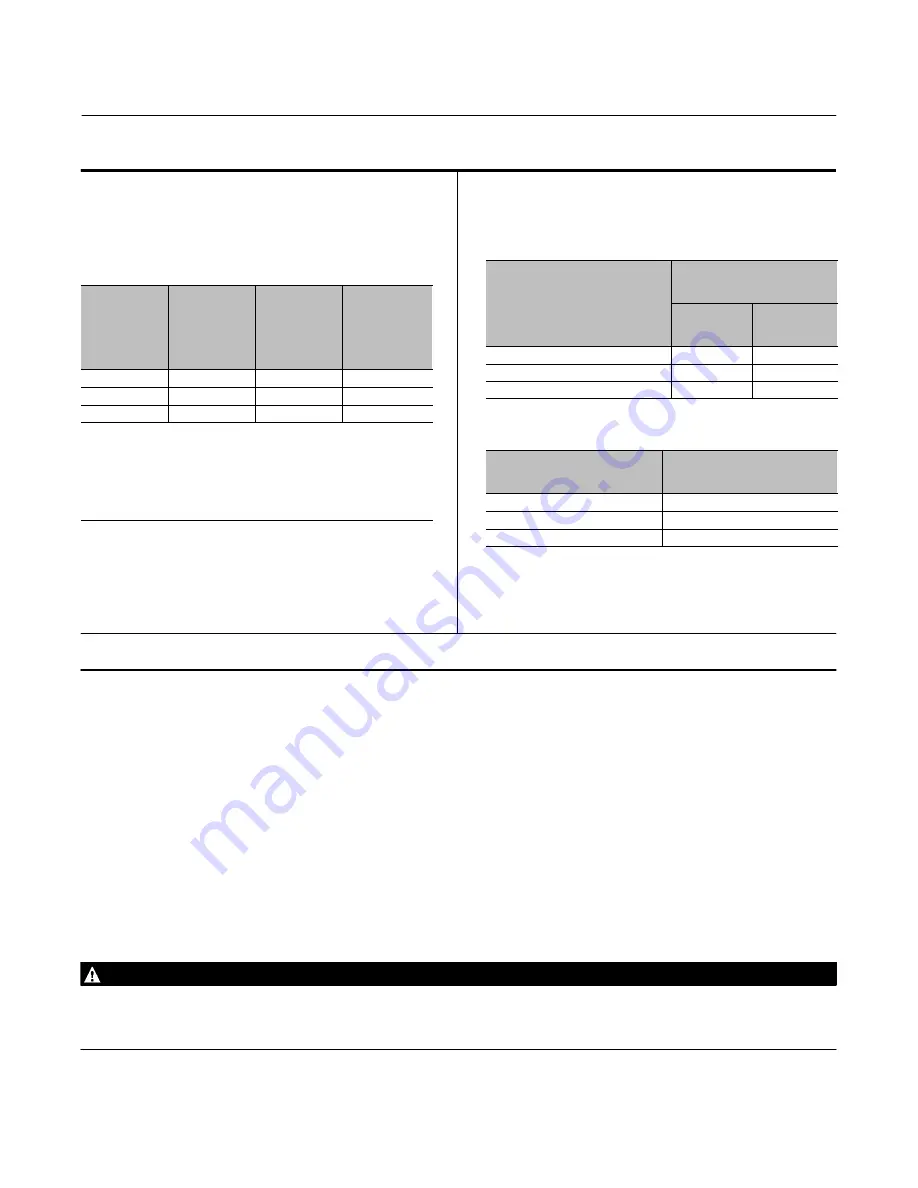
Instruction Manual
D100304X012
656 Actuator
June 2017
2
Table 1. Specifications
Maximum Recommended Casing Operating
Pressure
(1)
2.4 bar (35 psig)
Maximum Allowable Casing Pressure
(2)
Actuator
Size
Maximum
Casing
Pressure for
Actuator
Sizing
(2)
,
Bar (Psig)
Maximum
Excess
Diaphragm
Pressure
(1)
,
Bar (Psig)
Maximum
Diaphragm
Casing
Pressure
(2,3)
,
Bar (Psig)
30
8.6 (125)
1.0 (15)
9.7 (140)
40
4.5 (65)
0.69 (10)
5.2 (75)
60
2.8 (40)
0.69 (10)
3.4 (50)
1. Additional pressure may be added when the actuator is at full travel. If the Maxi
mum Excess Diaphragm Pressure is exceeded, damage to the diaphragm or dia
phragm casing might result. See the Maximum Pressure Limitation section.
2. Maximum diaphragm casing pressure must not be exceeded and must not produce
a force on the actuator stem greater than the maximum allowable actuator output
thrust or the maximum allowable stem load. See the Maximum Pressure Limitation
section.
3. This maximum casing pressure is not to be used for normal operating pressure. Its
purpose is to allow for typical regulator supply settings and/or relief valve tolerances.
Operating Temperature Range
(3)
J
-
40 to 82
°
C (-40 to 180
°
F) with Nitrile Elastomer
J
-
40 to 149
°
C (-40 to 300
°
F) with Silicone
Diaphragm
Casing Pressure Connection
1/4 NPT internal
Maximum Travel
ACTUATOR SIZE
MAXIMUM RATED
STEM TRAVEL,
mm (INCHES)
Standard
Travel
Stop
Optional
Travel
Stop
30
54 (2.125)
Not available
40
89 (3.5)
76 (3)
60
105 (4.125)
97 (3.8125)
Actuator Weight
Actuator Size
Approximate
Shipping Weight,
kg (Pounds)
30
23 (50)
40
32 (70)
60
73 (160)
Options
J
Top‐mounted handwheel/adjustable travel stop
J
Casing‐mounted adjustable down travel stop
1. Control and stability may be impaired if this pressure is exceeded.
2. Exceeding this pressure can cause damage to the diaphragm, diaphragm casing, or other parts.
3. The temperature limits in this manual and any applicable standard or code limitation for valve should not be exceeded.
Principle of Operation
In a direct acting diaphragm actuator, increasing loading pressure moves the actuator stem downward, compressing
the spring. When the diaphragm pressure is decreased, the spring moves the actuator stem upward. In the event of
failure of the loading pressure, the actuator stem moves to the extreme upward position.
Specifications
Refer to table 1 for Specifications of the 656 actuator. See the actuator nameplate for specific information for your
actuator.
WARNING
To avoid personal injury or damage to equipment that may result in the malfunction of the control valve or loss of control
of the process caused by excessive pressure, do not exceed the Maximum Pressures listed in table 1. Refer to the following
Maximum Pressure Limitations section.