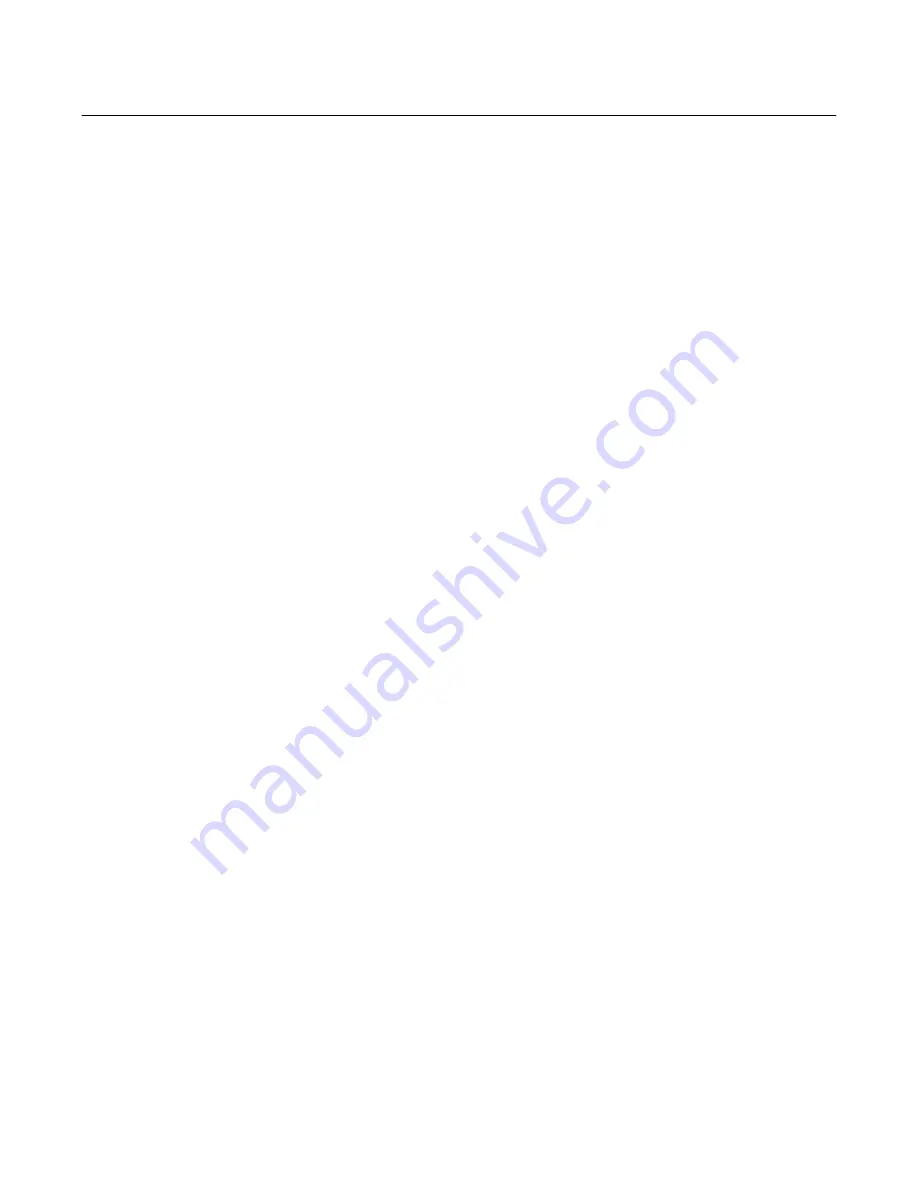
Instruction Manual
D200354X012
4200 Transmitters
March 2011
9
2. Bolt the stem mounting bracket and spacer (keys 34 and 39) to the stem connector on the actuator stem. Replace
the stem connector cap screws with the two cap screws (key 35) furnished with the stem mounting bracket.
3. If necessary, refer to the appropriate procedures in the actuator instruction manual to reconnect the actuator stem
to the valve stem.
4. Fasten the stem bracket (key 33) to the stem mounting bracket (key 34) with two cap screws (key 37) centered in
the slots of the stem bracket. Tighten the cap screws slightly.
5. On the transmitter, install the pickup pin into the lever assembly (key 30) in the position to match the application.
Refer to table 3 and figure 15.
6. Temporarily connect the 24 volt DC power supply to the instrument as indicated in figure 4.
7. Perform the potentiometer alignment procedures before mounting the transmitter on the actuator. To simulate
mid‐stroke position in step
4 of the procedure, move the lever assembly (key 30) until its center line is parallel with
the center line of the operating arm (key 25). After completing step 9 of the potentiometer alignment procedure,
remove the 24 volts DC, and continue the actuator mounting procedure as described in the following steps.
8. Stroke the actuator to the mid position of the valve travel.
9. Fit the pickup pin, located in the lever assembly (key 30), into the horizontal slot in the stem bracket (key 33). Bolt
the mounting plate (key 21) to the actuator with cap screws, washers, and spacers (keys 23, 24, and 22) using the
two tapped holes in the side of the actuator yoke.
10. Use the mounting plate slots, which allow the lever assembly (key 30) and the operating arm (key 25) to be nearly
parallel, and position the long edge of the mounting plate parallel with the actuator stem. Tighten the bolts
securely.
11. Loosen the two cap screws (key 37) connecting the stem bracket (key 33) to the stem mounting bracket (key 34).
Manually move the lever assembly (key 30) until its center line is parallel with the center line of the operating arm
(key 25).
12. Tighten the two cap screws (key 37) in the slotted holes.
13. Stroke the actuator to ensure that full travel is allowed.
14. Perform the electrical connection and direct and reverse action procedures.
15. Verify potentiometer alignment by performing the potentiometer alignment procedure.
Rotary‐Shaft Actuator Mounting, 4210, 4211, 4212, and 4215
Refer to figure 19 for key number locations for this example.
1. Install the transmitter on the mounting plate (key 21) with two cap screws (key 32). The transmitter can be
mounted in any of four positions on the bracket. Tighten the cap screws slightly.
2. On the actuator, attach the coupler plate assembly (key 57) and travel indicator to the actuator shaft. This is
accomplished by removing two self‐tapping screws and travel indicator and replacing them with the self‐tapping
screws and coupler plate assembly furnished with the transmitter for the mounting application.
3. Install the mounting plate (key 21) on the actuator using the four cap screws and washers (keys 23 and 24). The
transmitter and bracket can be mounted in any of four positions by using the cap screws (key 23) on the face of the
actuator hub.
4. Tighten the cap screws (key 23) slightly while aligning the potentiometer shaft on the transmitter with the coupler
plate assembly pin (key 57). When aligned, tighten the four cap screws (key 23). Maintain this alignment while
tightening the two cap screws (key 32) holding the transmitter to the mounting plate (key 21).
5. Slide the coupler (key 52) over the potentiometer shaft and into the hole in the mounting plate (key 21). Slide the
coupling (key 54) onto the plate assembly pin and attach the coupling to the plate assembly pin using the set screw.
6. Slide the coupler (key 52) into the coupling (key 54). The coupling should not be deflected in any direction when
installed. Do not tighten the coupling set screw (key 53) as it will be tightened during the potentiometer alignment
procedure.