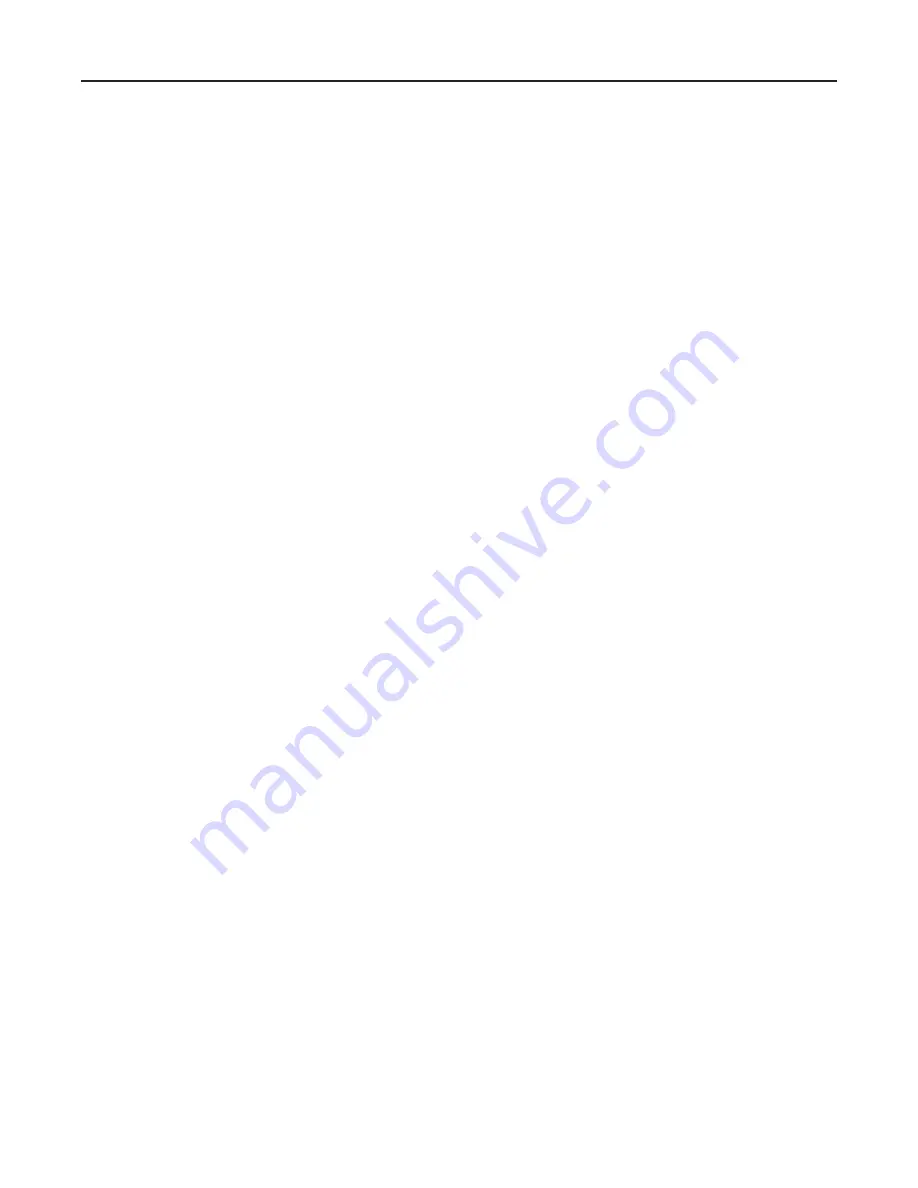
Type 122A
5
Disassembly
1. Loosen the locknut (key 30). Rotate the adjusting
screw (key 7) counterclockwise until all compression
has been relieved from the spring (key 3).
2. Disconnect piping from the bottom connector
(key 36). Unscrew and remove the bottom connector.
3. To remove the lower seat ring (key 37), insert a
hexagonal bar into the seat ring hole and use the bar
to unscrew the seat ring. The hexagonal hole in the
seat ring is 7/16 in. / 11 mm across the flats.
4. Unscrew and remove the spring case cap screws
and nuts (keys 26 and 4). Remove the spring case,
upper spring seat and spring (keys 1, 31 and 3).
5. Unscrew the hex nuts (key 4) from the stem
(key 5). Remove the spring guide, diaphragm
head, diaphragm, O-ring, back-up ring and
washer (keys 6, 8, 9, 12, 13 and 10).
6. Unscrew the remaining hex nuts from the stem
and pull the disk holder assembly (key 22) and
attached stem out through the bottom opening.
7. Remove the disk holder from the stem.
8. Disconnect the control line from the diaphragm
case (key 2). Unscrew the union nut (key 19) and
remove the diaphragm case, snap ring (key 20)
and body gasket (key 21) from the body (key 23).
9. Unscrew the self-tapping screws (key 16) from
each end of the diaphragm case. Remove the
washers and guide bushings (keys 14 and 15).
10. Remove the O-ring and back-up rings (keys 12
and 13) from the diaphragm end of the diaphragm
case and remove the felt washers, flat washer,
O-ring and back-up rings (keys 18, 17, 12 and 13)
from the valve end of the diaphragm casing.
11. Use a thin-wall socket wrench to remove the upper
seat ring (key 24).
Assembly
1. Screw the upper seat ring (key 24) into the body
(key 23).
2. Install the back-up rings and O-rings (keys 13
and 12) into each end of the diaphragm case
(key 2).
3. Install the washer (key 17) and three felt washers
(key 18) into the valve end of the diaphragm case.
Replace the guide bushings (key 15) in each end
of the diaphragm casing. Carefully insert the stem
(key 5) through the diaphragm casing to be sure the
parts are aligned. Attach the washers (key 14) with
self-tapping screws (key 16). Remove the stem.
4. Replace the body gasket and snap ring (keys 21
and 20). Secure the diaphragm case to the body
with the union nut (key 19).
5. Coat the threads on the valve end of the stem
with high strength threadlocker. Attach the disk
holder assembly (key 22) to the stem. Carefully
install the stem through the opening of the body.
6. Screw two hex lock nuts onto the stem. Install
the back-up ring, washer, O-ring, diaphragm,
diaphragm head and spring guide (keys 13, 10, 12,
9, 8 and 6). Secure with two hex lock nuts (key 4).
7. Set the spring and spring seat (keys 3 and 31)
onto the spring guide. Attach the spring case with
cap screws in a crisscross pattern.
8. Screw the lower seat ring (key 37) into the bottom
connector (key 36). Install the bottom connector
into the body.
9. Re-connect piping to the bottom connector and to
the control connection in the diaphragm casing.
10. Adjust the spring by following the
“Adjustment” instructions.
Parts Ordering
When corresponding with your local Sales Office
about this valve, mention the serial number and
all other data stamped on the nameplate. When
ordering replacement parts, also state the complete
11-character part number of each part required as
found in the following parts list.