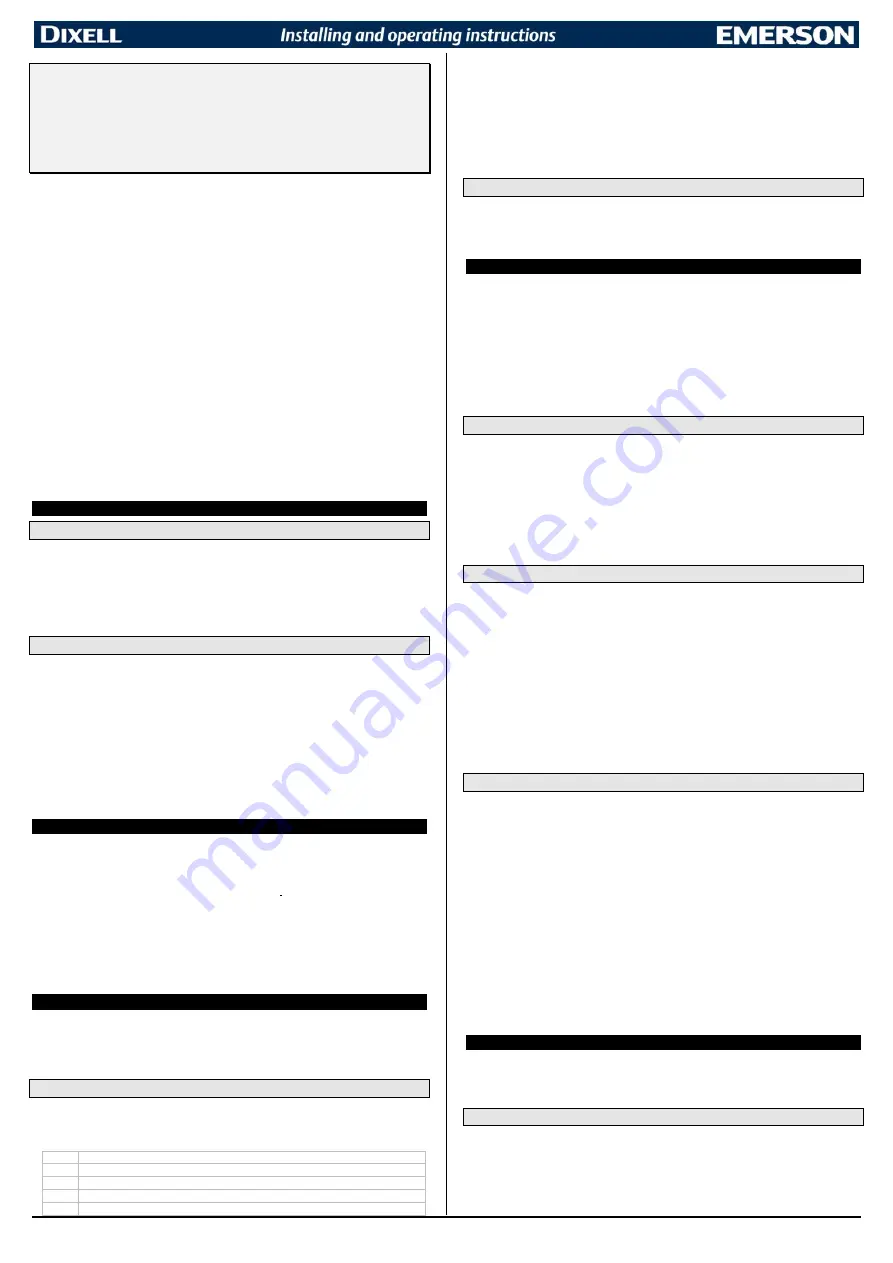
1592026601 XWi70K STD FULL EN r1.6 2022.07.29.docx
XWi70K
1/15
XWi70K
ADVANCED ENERGY MANAGEMENT CONTROLLER
FW REL. 24.5
............................................................................................ 8
1
GENERAL WARNING
1.1
PLEASE READ BEFORE USING THIS MANUAL
•
This manual is part of the product and should be kept near the instrument for easy and quick
reference.
•
The instrument shall not be used for purposes different from those described hereunder. It cannot
be used as a safety device.
•
Check the application limits before proceeding.
•
Dixell S.r.l. reserves the right to change the composition of its products, even without notice,
ensuring the same and unchanged functionality.
1.2
SAFETY PRECAUTIONS
•
Check the supply voltage is correct before connecting the instrument.
•
Do not expose to water or moisture: use the controller only within the operating limits avoiding
sudden temperature changes with high atmospheric humidity to prevent formation of condensation
•
Warning: disconnect all electrical connections before any kind of maintenance.
•
Fit the probe where it is not accessible by the End User. The instrument must not be opened.
•
In case of failure or faulty operation send the instrument back to the distributor or to “Dixell S.r.l.”
(see address) with a detailed description of the fault.
•
Consider the maximum current which can be applied to each relay (see Technical Data).
•
Ensure that the wires for probes, loads and the power supply are separated and far enough from
each other, without crossing or intertwining.
•
In case of applications in industrial environments, the use of mains filters (our mod. FT1) in parallel
with inductive loads could be useful.
2
GENERAL DESCRIPTION
Model
XWi70K
is a microprocessor-based controller suitable for applications on medium or low
temperature refrigerating units. It must be connected by means of a two-wire shielded twisted cable (
1mm) at up to 30 meters to the keyboard
CH620
,
T620T/H
or
T820T/H
. It is provided with five relay
outputs to control compressor, defrost (which can be either electrical or hot gas), evaporator and
condenser fans and light or alarm. It is also provided with 4 NTC or PT1000 probe inputs. It has a both
a frequency output and a serial port which can be used to control variable speed compressors. A couple
of analogue outputs (4-20mA or 0-10Vdc) and a master 2-wire RS485 output for serial controlled
ventilator complete the HW resources.
The HOTKEY I/O port allows connecting the unit, by means of the external module XJ485-CX, to a
network line
ModBUS-RTU
compatible such as
an
X-WEB monitoring system. With the HOTKEY port
it is possible to modify the configuration of the controller (by using the Wizmate Progtool Kit).
The instrument is fully configurable and it can be easily programmed through an external keyboard.
3
FIXED SPEED COMPRESSOR CONTROL
The regulation uses the temperature measured by the regulation probe with a positive differential from
the set point: if the temperature increases and reaches set point plus differential the compressor is
started and then turned off when the temperature reaches the set point value again. In case of any
regulation probe fault, the compressor management will switch to fixed ON/OFF time mode, as set in
the parameters
Con
and
CoF
.
3.1
DOUBLE FIXED SPEED COMPRESSOR CONTROL
The controller can drive double compressor circuits. To do this, a couple of relays need to be properly
configured:
oAx=CP1
and
oAy=CP2
. (do not use
oA5
for compressor management). The parameters
used for this kind of regulation are the following:
AC
Compressor anti-short-cycle delay
AC1
Second compressor anti-short-cycle delay
2CC
Activation mode for second compressor (valid if oAx=CP1 and oAy=CP2)
rCC
Compressors rotation enabled
Cdd
Maximum time with compressor active
The second compressor output is activated by following the
2CC
parameter:
-
If
2CC=FUL
then in parallel with the relay of the first compressor (
CP1
), with a possible
delay as set in the
AC1
parameter. Both compressors are switched off at the same time.
-
If
2CC=HAF
then only if the temperature
T>SET+HY+HY1
. The delay
AC1
is always
respected. The second compressor is deactivated when
T<SET+HY
.
With parameter
rCC
it is possible to enable the compressor rotation function: the activation of the first
and the second compressor will be alternated to equalize the number of working hours of both of them.
In case of hot gas defrost operation, it is possible to select if one or both compressors will be used.
3.2
PULL DOWN
When defrost is not in progress, it can be activated by keeping the
UP
button pressed for 3 sec. The
compressor will operate to reach the
CCS
set point by the time set through the
CCt
parameter. The
cycle can be terminated before the end of the
CCt
time by using the same activation button (keeping
the
UP
pressed for 3 sec when PULL DOWN is running)
4
DEFROST
Two defrost modes are available through the
tdF
parameter: defrost through electrical heater
(
tdF=EL
) and hot gas defrost (
tdF=in
).
The defrost interval depends on the presence of the RTC (optional). The internal RTC is controlled by
means of the
EdF
parameter:
-
EdF=in:
the defrost is made every
idF
time
–
standard way for controller without RTC.
-
EdF=rtC:
the defrost is real time controlled, depending on the day enabled in the parameters
dd1
…
dd7
and the hours set in the parameters
Ld1...Ld6
.
Other parameters are used to control defrosting cycles: the maximum length (
MdF
) and defrosting
modes: timed or controlled by the evaporator’s pro
be (
P2P
).
At the end of defrost dripping time is started, its length is set in the
Fdt
parameter. With
Fdt=0
the
dripping time is disabled.
4.1
SYNCHRONIZED DEFROST
This defrost function requires:
-
To set a digital input of any controller as
ixF=dEF
-
To connect (by wire) all digital inputs set as
ixF=dEF
A maximum number of 20 controllers can be used in this configuration.
The Synchronized defrost mode is enabled by par.
SYd=SYn
. After any defrost request (received by
RTC, timed by par.
idF,
manually by defrost button or by digital input set as dEF), all controllers will
activate their own defrost phase. The first controller which ends its defrost phase will release the defrost
line and load its dripping time. At the end of the dripping time the normal regulation will restart.
The other controllers follow the same logic.
4.2
DESYNCRONIZED DEFROST
This defrost function requires:
-
To set a digital input of any controller as
ixF=dEF
-
To connect (by wire) all digital inputs set as
ixF=dEF
A maximum number of 20 controllers can be used in this configuration.
The De-Synchronized defrost mode is enabled by par.
SYd=nSY
. After any defrost request (received
by RTC, timed by par.
idF,
manually by defrost button or by digital input set as dEF), all controllers will
load a random delay. The first controller which ends the random delay will retain the
ixF=dEF
line to
signal to the other controllers that they have to wait before starting their own defrost phases. When the
first controller ends its defrost phase, it will release the
ixF=dEF
line. The other ones will repeat the
same procedure. The total defrost phase will end when all controllers complete their own defrost phases.
NOTES:
-
take care about the time available to complete the defrost phase. It must be used for selecting
the proper
MdF
value
-
all controllers in waiting mode will keep on the normal regulation
4.3
RANDOM DEFROST
A random defrost mode can be enabled by par.
Syd=rnd
. After any defrost request (received by RTC
or timed by par.
idF
) a random delay will be added. At the end of the added delay the defrost will start.
The random function lead to desynchronize the start of the defrost phases in those cases where more
than a cabinet is installed in the same “island”. The maximum defrost delay is linked to the following
parameters:
-
Mdf
=maximum time for any defrost
-
ndE
=delay multiplier
by the following formula:
MAX_DEFROST_DELAY =
Mdf*ndE
(min)
For example: if
ndE=10
and
Mdf=20 min
, this means that the total interval of time used by any device
for complete its defrost phase is 200 min (worst case).
NOTE:
-
take care about the interval of time available for defrost. It must be used for selecting both
MdF
and
ndE
values
-
the higher is the
ndE
value and the better is the result in terms of desynchronization. On the
other side, the longer will be the total interval of time required to complete defrosts
5
FAN MANAGEMENT
The controller can manage the following type of fans:
-
Fixed speed fans (
oAx=FAn
,
Cnd
)
-
Variable speed fans with 0-10V or 4-20mA control signal (
1Ao or 2Ao=FAn, Cnd
)
-
Variable speed fans with Modbus control signal (EBM models only)
5.1
MODBUS FAN SUPPORTED
It is possible to use up to 4 fans with EBM Modbus communication protocol. The following parameters
need to be properly configured:
-
S00:
number of condenser fan controlled via Modbus
-
C01
to
C04:
serial address for condenser fans
-
vdF:
serial output for fan management enabled