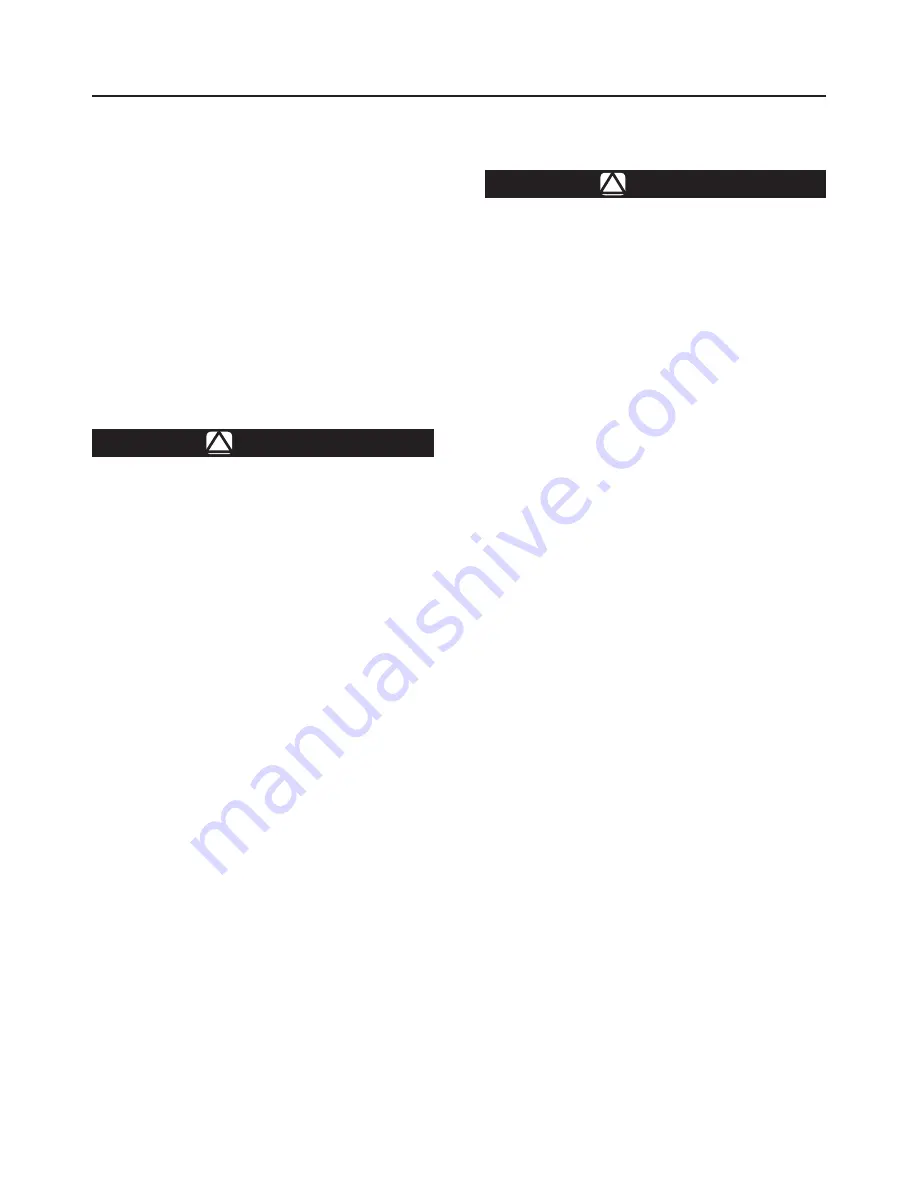
Shutdown
Installation arrangements may vary, but in any installation
it is important that the valves be opened or closed slowly
and that the outlet pressure be vented before venting
inlet pressure to prevent damage caused by reverse
pressurization of the regulator. The steps below apply to the
typical installation as indicated.
1 .
Slowly close the upstream shutoff valve
2 .
Open vent valves downstream of the regulator.
3 .
Inlet pressure should automatically be released
downstream as the regulator opens in response to the
lowered pressure under the diaphragm.
4 .
Close outlet shutoff valve.
Maintenance and Inspection
!
waRNINg
To avoid personal injury or equipment
damage, do not attempt any maintenance
or disassembly without first isolating
the regulator from system pressure and
relieving all internal pressure as described in
“Shutdown” section.
Regulators that have been disassembled for
repair must be tested for proper operation
before being returned to service. only parts
manufactured by emerson should be used
for repairing Fisher™ regulators. Restart
gas utilization equipment according to
normal startup procedures.
Due to normal wear or damage that may
occur from external sources, this regulator
should be inspected and maintained
periodically. The frequency of inspection
and replacement depends on the severity
of service conditions or the requirement of
local, state and federal rules and regulations.
In accordance with the applicable National or
Industry codes, standards and regulations/
recommendations, all hazards covered by
specific tests after final assembly and before
applying the Ce marking, shall be covered
also after every subsequent reassembly
at installation site, in order to ensure that
the equipment will be safe throughout its
intended life.
periodic inspection must be performed on
the CSB700 Series that include the slam-shut
overpressure protection module to ensure
protection of the downstream system in the
event the primary regulator losses pressure
control. This inspection must test that slam-
shut functions as intended.
Main Diaphragm Maintenance
CauTIoN
For version with token relief measure the
distance before disassembly and note for
reassembly (see Figure 10).
Failure to follow the instructions regarding
measurement could impact the token
relief’s set-point
Perform the following steps to disassemble, inspect and
replace the main diaphragm:
1 .
Remove the closing cap (key 60, Figure 12) or loosen
hex nut (key 67). Turn the adjusting screw (key 65)
or adjusting bolt (key 64) counterclockwise to ease
spring compression.
Note
when disassembling a CSB700 Series
regulator, support the adjusting screw
(key 65) to prevent damage or contamination
due to falling.
2 .
Remove the adjusting screw (key 65) or the adjusting
bolt (key 64), then the bonnet (key 61), upper spring
seat (key 63) and sealing washer (key 113). Check the
sealing washer and replace if damaged. Remove the
spring (key 38).
3 .
Remove hex nuts (key 16, Figure 7 or 8) and bolt
(key 15). Separate the upper spring case (key 1) from
the lower casing assembly (key 9).
Note
when disassembling a CSB700 Series
regulator, lift the upper spring case (key 1,
Figure 7 or 8) straight up in order to avoid
hitting the stem (key 44).
4 .
Slide the diaphragm assembly (key 55, Figure 10) away
from the body (key 70) to unhook the pusher post from
the lever (key 10). Lift out the diaphragm assembly
(key 55) and its attached parts like pusher post (key 50)
and relief valve seat (key 51).
5a. For non-relieving units such as Type CSB700EN, see
Figure 10 — Non-relief assembly. Remove the screw
(key 45) and nut (key 40) to separate relief valve spring
seat (key 43), diaphragm assembly (key 55) and pusher
post (key 50). Check the diaphragm (key 55A) for damage
and replace if necessary.
CSB700 Series
14