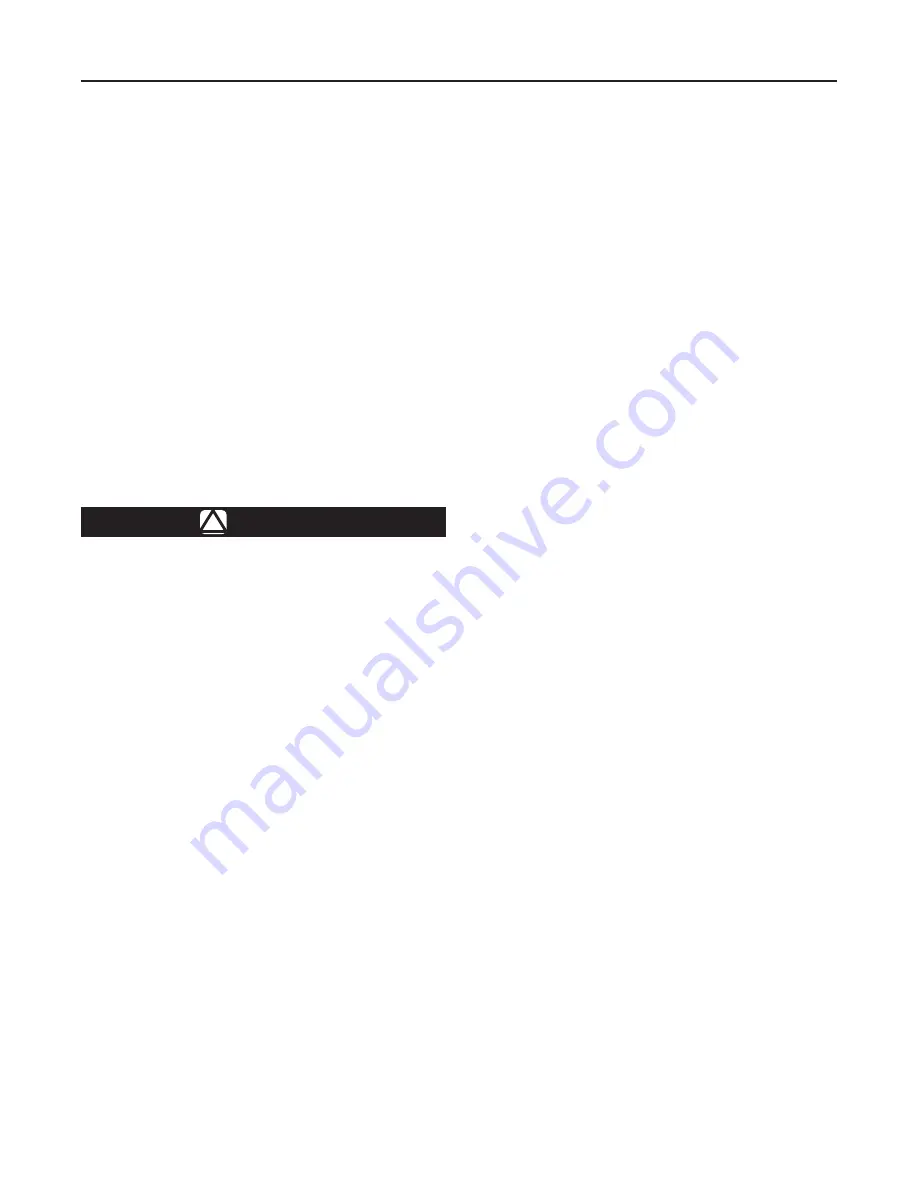
CSB400 Series
15
number of bends and elbows. The remote vent line
should have the largest practical diameter. Vent piping
on regulators with token relief must be large enough to
vent all relief valve discharge to atmosphere without
excessive backpressure and resulting excessive
pressure in the regulator.
For Types with optional Token relief, this low capacity
relief is located in the spring case of the Primary
Regulator. If necessary to vent escaping gas away,
install a remote vent line in the spring case tapping of
the Primarily Regulator as described above.
Periodically check all vent openings to be sure that
they are not plugged or obstructed.
CSB400 Series outlet pressure ranges are shown in
Table 5. Outlet pressure higher than 0,35 bar (5 psig)
above the setpoint may damage internal parts such as
the diaphragm head and valve disk.
The maximum
emergency (casing) outlet pressure is 4,0 bar
(58 psig).
Startup
CaUTIOn
Pressure gauges must always be used
to monitor downstream pressure
during Startup.
With the downstream system depressurized, use the
following procedure to start up the regulator.
1. Check to see that all appliances are turned off.
2. Slowly open the upstream shut-off valve.
3. Check inlet and outlet pressure for correct values.
4. Check all connections for leaks.
5. Turn on utilization equipment and recheck
the pressures.
adjustment
note
For types that include the Integral
Monitor module, refer to the Instruction
Manual for Type TM600 Integral Monitor
for adjustment and maintenance of the
Integral Monitor. For the types that
include the slam-shut module, refer to
the instruction manual for Type VSX4
slamshut for adjustment and maintenance
of the slamshut.
The range of allowable pressure
settings for the primary regulator
is stamped on the nameplate. If the
required setting is not within this range,
substitute the correct spring (as shown
in Table 5). If the spring is changed,
change the nameplate to indicate the
new pressure range.
a pressure gauge must always be used
to monitor downstream pressure while
adjustments are being made.
For Types CSB400 and CSB420
1. Remove the closing cap (key 60, Figure 17).
2. To increase the outlet setting, turn the adjusting
screw (key 65) clockwise. To decrease the outlet
setting, turn the adjusting screw counterclockwise.
3. Replace the closing cap.
For Type CSB450
1. Loosen the hex nut (key 58, Figure 17).
2. To increase the outlet setting, turn the adjusting
screw (key 65, Figure 17) clockwise. To decrease
the outlet setting, turn the adjusting screw
counterclockwise.
3. Tighten the hex nut.
CSB400 Series with Integral Monitor
When adjusting the primary regulator and Integral
Monitor for operation, ensure that the pressure
differences between the primary regulator and the
integral monitor shown in Table 6 are observed. For
example, if the primary regulator setpoint is set at
20 mbar (8-inches w.c.), then the Integral Monitor
should be set at a minimum of 35 mbar (14-inches w.c.)
or higher.
To test the Integral Monitor operation, the primary
regulator setpoint must be adjusted above the Integral
Monitor’s setpoint to simulate a failure of the primary
regulator. If the spring range of the primary regulator
is sufficiently high, it can simply be adjusted above the
Integral Monitor’s setpoint by following step 2 above.
Otherwise, a different spring with a setpoint higher
than the Integral Monitor’s setpoint must be installed to
check the operation of the Integral Monitor.
CSB400 Series with Slamshut
When adjusting the primary regulator and slamshut for
operation, refer to Table 7 for the OPSO setpoints and
also the combined OPSO and UPSO setpoints of the
slamshut for a given regulator spring ranges.
Shutdown
Installation arrangements may vary, but in any
installation it is important that the valves be opened