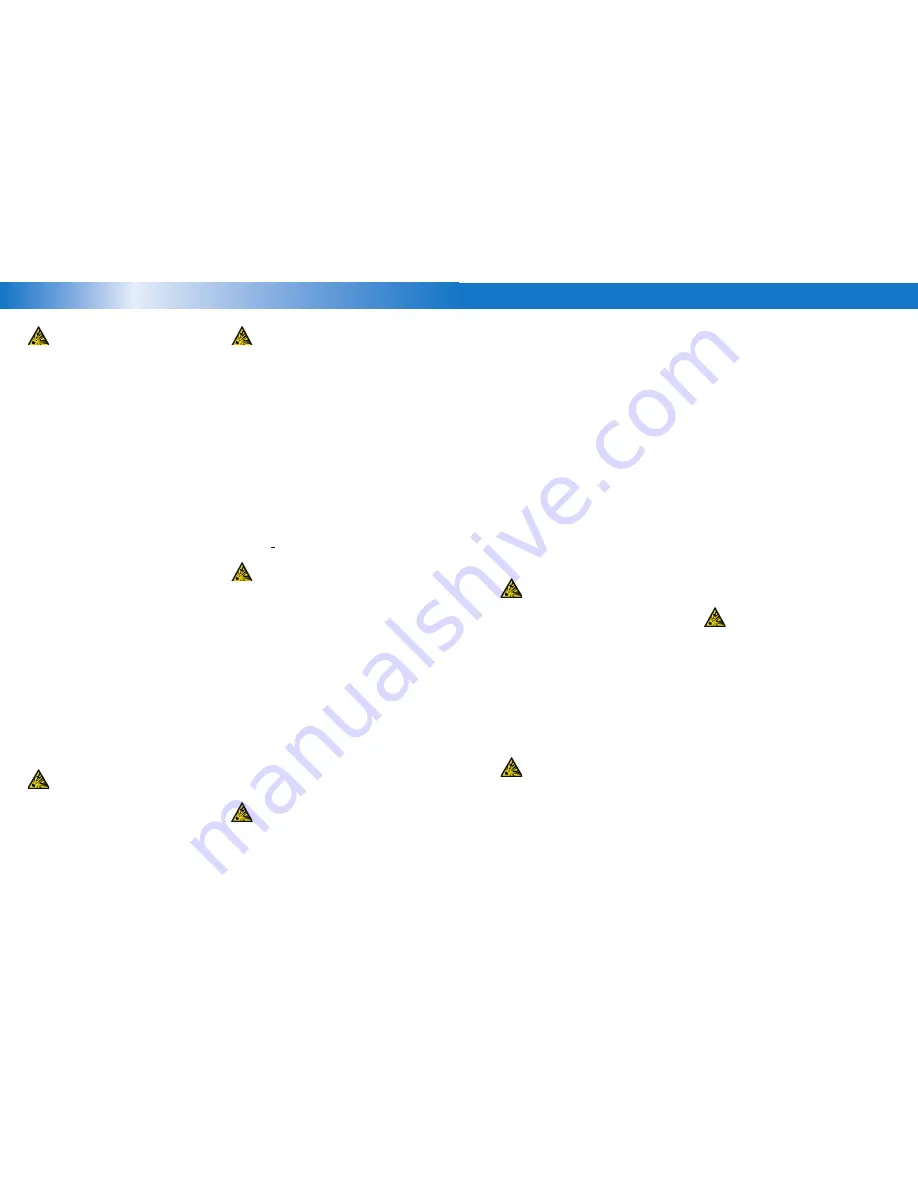
18
19
Maintenance
Refrigerant Exchange
Qualifi ed refrigerants and oils were indicated on page 8.
It
is not necessary to replace the refrigerant with a new one
unless contamination due to an error such as topping up
the system with an incorrect refrigerant is suspected. To
verify correct refrigerant composition, a sample can be
taken for chemical analysis. A check can be made during
shut down by comparing the refrigerant temperature and
pressure using precision measurements at a location in
the system where liquid and vapor phases are present and
when the temperatures have been stable.
In the event that the refrigerant needs replacing, the charge
should be recovered using a suitable recovery machine.
When R22 in a system with mineral oil is to be replaced
with R407C or R404A, the oil must also be changed.
Please refer to Technical Information “Refrigerant
changeover from HCFC to HFC Refrigerants”.
Replacing Compressor
Rotalock valves should be re-torqued periodically to
ensure that leak tightness is maintained. All gaskets and
fi ttings should be inspected for signs of leaks and repaired
if necessary. Electrical connections should be checked for
tightness. All wires should be clamped securely and routed
away from hot surfaces to prevent damage from vibration
and heat.
Some minor repairs like sensor replacement can be done while
the compressor is still under pressure. To replace components
that are under pressure, shut down the compressor, wait 15
seconds, and turn off all power. Close the service valves, recover
the refrigerant and change the faulty component. Evacuate the
compressor only, open the service valves, and recharge the same
quantity of refrigerant that was recovered.
Change the accumulator after replacing a compressor with
a burned out motor. The accumulator oil return orifi ce or
screen may be plugged with debris or may become plugged.
This will result in starvation of oil to the new compressor and
a second failure.
In the case of a motor burnout, the majority of contaminated
oil will be removed with the compressor. The rest of the oil
is cleaned through the use of suction and liquid line fi lter
The maximum pressure for leak testing should be no
higher than 22.5 bar(g).
Use only dry nitrogen or dry air for system pressure
testing. DO NOT USE other industrial gases.
If using dry air do not include the compressor in the
pressure test – isolate it fi rst. Never add refrigerant to the
test gas (as leak indicator).
System Evacuation and Dehydration
Before the installation is put into operation, remove the
holding charge then evacuate with a vacuum pump.
Proper evacuation reduces residual moisture to 50 ppm.
The installation of adequately sized access valves at the
furthest point from the compressor in the suction and
liquid lines is advisable. To achieve undisturbed operation,
the compressor valves are closed and the system is
evacuated down to 0.3 mbar / 0.225 Torr. Pressure must
be measured using a vacuum pressure (Torr) gauge on the
access valves and not on the vacuum pump; this serves to
avoid incorrect measurements resulting from the pressure
gradient along the connecting lines to the pump. Then the
compressor must be evacuated. Due to the factory holding
charge of dry air, the compressor is under pressure (about
1-2.5 bar), this is to indicate the compressor does not leak.
Preliminary Check
Discuss installation details with the installer. If possible,
obtain drawings, wiring diagrams, etc. It is ideal to use a
checklist but always check the following:
•
Visual check of the electrics, wiring, fuses etc.
•
Visua
l check of the plant for leaks, loose fi ttings such
as TXV bulbs etc.
•
Compressor oil level
•
Calibration of HP and LP switches and any pressure
actuated valves
•
Check setting and operation of all safety features and
protection devices
•
All valves in the correct running position
•
Pressure and compound gauges fi tted
•
Correctly charged with refrigerant
•
Compressor electrical isolator location & position
Never install a system in the fi eld and leave it unattended
when it has no charge, a holding charge, or with the service
valves closed without securely electrically locking out the
system. This will prevent unauthorized personnel from
accidentally operating the system and potentially ruining
the compressor by operating with no refrigerant fl ow.
Do not start the compressor while the system is in
a vacuum.
Refrigerant Charging
PC Board should be powered to close EXV before
charging. The system should be liquid-charged through
the liquid-receiver shut-off valve or through a valve in the
liquid line. The use of a fi lter drier in the charging line is
highly recommended. Because scrolls have discharge
check valves, systems should be liquid-charged on both
the high and low sides simultaneously to ensure that a
positive refrigerant pressure is present in the compressor
before it runs.
Charging quantity can be determined by referring to system
discharge and suction pressures. Another very useful
parameter is the liquid line temperature which has been
listed in the Fusion Catalogue. At a measured condensing
temperature and an evaporating temperature, the liquid line
temperature should be around Emerson‘s recommendation
value 5K tolerance.
The majority of the charge should be placed in the high side
of the system to prevent bearing washout during fi rst-time
start on the assembly line or on site.
Do not operate with a restricted suction. Do not operate
with the low-pressure cut-out bridged. Do not operate
compressor without enough system charge to maintain at
least 0.3 bar suction pressure. Allowing pressure to drop
below 0.3 bar for more than a few seconds may overheat
scrolls and cause early drive bearing damage. If the suction
pressure is low on startup, and top up of the refrigerant
charge is required, it is preferable to bleed liquid slowly
into the suction line of a running compressor than to risk
overheating by vapour charging.
The system should be liquid-charged through the liquid-
receiver shut-off valve or through a valve in the liquid
line. The use of a fi lter drier in the charging line is highly
recommended. The majority of the charge should be
placed in the high side of the system to prevent bearing
washout during fi rst-time start on the assembly line.
Initial Startup
It is important to ensure that new compressors are not
subjected to liquid abuse. Turn the crankcase heater on 12
hours before starting the compressor.
.
Warning
Warning
Warning
driers. A 100% activated alumina suction line fi lter drier is
recommended but must be removed after 72 hours. It is highly
recommended that the suction accumulator be replaced if the
system contains one. This is because the accumulator oil-return
orifi ce or screen may be plugged with debris or may become
plugged shortly after a compressor failure. This will result in
starvation of oil to the replacement compressor and a second
failure. When a single compressor or tandem is exchanged in
the fi eld, it is possible that a major portion of the oil may still
be in the system. While this may not affect the reliability of the
replacement compressor, the extra oil will add to rotor drag
and increase power usage.
Lubrication and Oil Removal
Do not mix up ester oils with mineral oil and/or alkyl
benzene when used with chlorine-free (HFC) refrigerants.
The compressor is supplied with an initial oil charge.
The standard oil charge for use with refrigerants R404A
is a polyolester (POE) lubricant Emkarate RL 32 3MAF.
In the fi eld, the oil level could be topped up with Mobil
EAL Arctic 22 CC if 3MAF is not available. The standard
mineral oil for R22 is Karamay 32BYMO. Therefore it is
recommended that a properly sized fi lter drier is installed
in all POE systems. This will maintain the moisture level in
the oil to less than 50 ppm.
If the moisture content of the oil in a refrigeration system
reaches unacceptably high levels, corrosion and copper
plating may occur. The system should be evacuated down to
0.3 mbar or lower. If there is uncertainty as to the moisture
content in the system, an oil sample should be taken
and tested for moisture. Sight glass/moisture indicators
currently available can be used with the HFC refrigerants
and lubricants; however, the moisture indicator will just
show the moisture content of the refrigerant. The actual
moisture level of POE would be higher than what the sight
glass indicates.
Oil Additives
Although Emerson Climate Technologies cannot
comment on any specific product, from our own testing
and past experience, we do not recommend the use of
any additives to reduce compressor bearing losses or for
any other purpose. Furthermore, the long term chemical
stability of any additive in the presence of refrigerant, low
and high temperatures, and materials commonly found in
refrigeration systems is complex and difficult to evaluate
without rigorously controlled chemical laboratory testing.
Warning
Warning
Warning
Warning
Warning