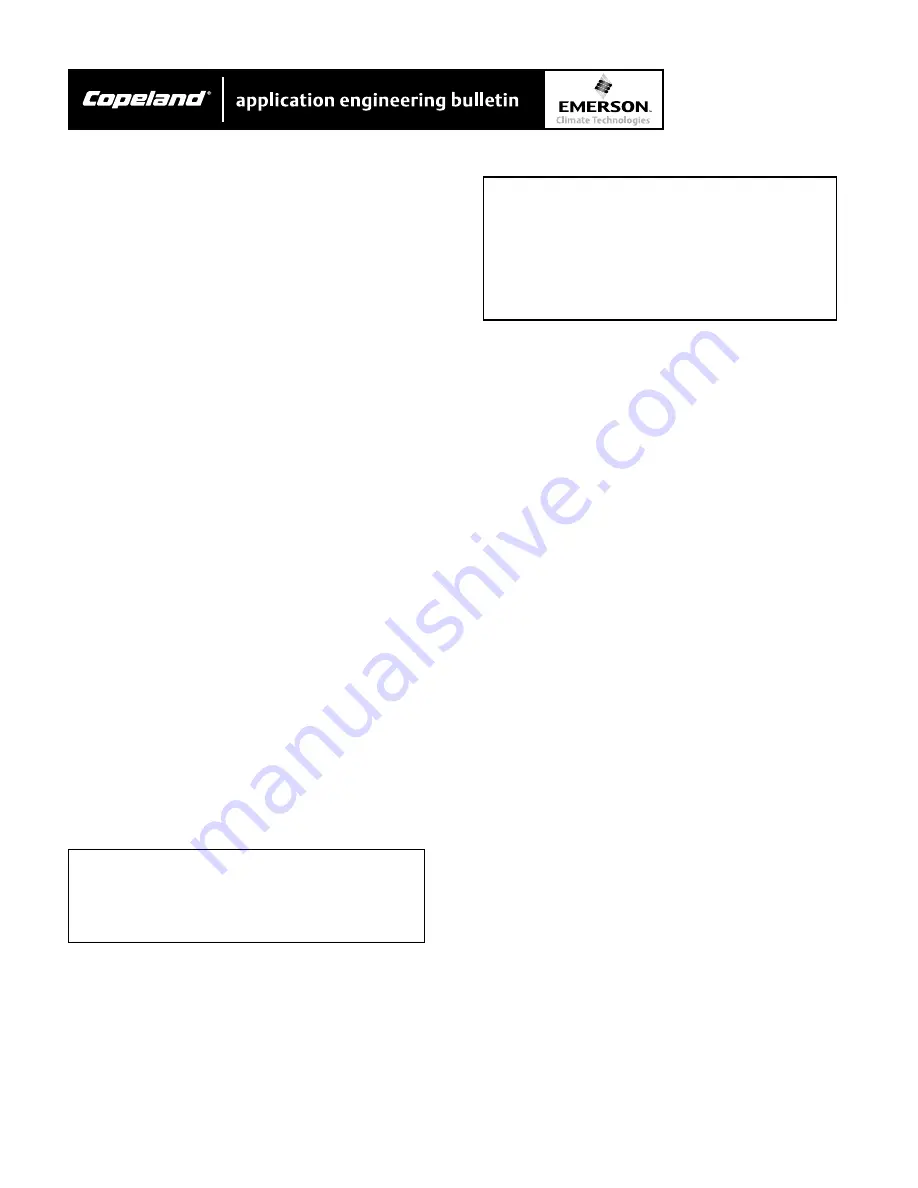
AE4-1322
© 2002 Copeland Corporation
Issued 4-2002
Printed in U.S.A.
18
•
Direction of rotation/phase sequence (direct mea-
surement at compressor terminals)
-
Immediate interruption of control current and
lock-out with wrong direction of rotation / phase
sequence (indication via signal contact 12)
-
Reset (after correction of fault) by interruption of
the supply voltage L/N for at least 2 seconds.
The protection device is built into the terminal box.
The wiring to the motor and oil temperature PTC
sensors and also to be motor terminals is factory
mounted. The electrical connections to the device
should be made according to figure 21 or 22 and the
schematic wiring diagrams.
In principle the device could be also built into the
control panel. In the case it is essential to adhere to
the following recommendations:
Special attention must be given when fitting the
INT69VSY-II in the control panel:
•
The connecting cables to the motor terminals must
be wired in the sequence described (L1 to terminal
“1” etc.) Check with a direction of rotation indicator!
•
Danger of induction!
Only use shielded cables or a twisted pair to
connect to the PTC motor sensors and oil tempera-
ture PTC sensors.
•
Additional fuses (4 A) must be incorporated in the
connecting cables between “L1/L2/L3” of the
protection device and the motor terminals “1/2/3”.
•
The terminals T1-T2 on the compressor and 1-2 on
protection device must not come into contact with
supply or control voltage.
CAUTION
CAUTION
CAUTION
CAUTION
CAUTION
If the rotation direction is wrong: Danger
If the rotation direction is wrong: Danger
If the rotation direction is wrong: Danger
If the rotation direction is wrong: Danger
If the rotation direction is wrong: Danger
of severe compressor damage!
of severe compressor damage!
of severe compressor damage!
of severe compressor damage!
of severe compressor damage!
6.4 Schematic wiring diagrams
6.4 Schematic wiring diagrams
6.4 Schematic wiring diagrams
6.4 Schematic wiring diagrams
6.4 Schematic wiring diagrams
The following schematic wiring diagrams show ex-
amples of application for
part winding and star delta
part winding and star delta
part winding and star delta
part winding and star delta
part winding and star delta
start each with infinite and 4-step capacity con-
start each with infinite and 4-step capacity con-
start each with infinite and 4-step capacity con-
start each with infinite and 4-step capacity con-
start each with infinite and 4-step capacity con-
trol.
trol.
trol.
trol.
trol.
In addition optional control schemes for liquid
injection, economizer operation and oil level controls
are included.
CAUTION
CAUTION
CAUTION
CAUTION
CAUTION
Make sure that the rotation monitoring is
Make sure that the rotation monitoring is
Make sure that the rotation monitoring is
Make sure that the rotation monitoring is
Make sure that the rotation monitoring is
functioning! T
functioning! T
functioning! T
functioning! T
functioning! Terminal D1 of the
erminal D1 of the
erminal D1 of the
erminal D1 of the
erminal D1 of the
INT69VSY
INT69VSY
INT69VSY
INT69VSY
INT69VSY-II must be connected
-II must be connected
-II must be connected
-II must be connected
-II must be connected
according to the wiring diagram.
according to the wiring diagram.
according to the wiring diagram.
according to the wiring diagram.
according to the wiring diagram. Remove
Remove
Remove
Remove
Remove
the jumper L/D1 at this time.
the jumper L/D1 at this time.
the jumper L/D1 at this time.
the jumper L/D1 at this time.
the jumper L/D1 at this time.
The following requirements must be ensured by
The following requirements must be ensured by
The following requirements must be ensured by
The following requirements must be ensured by
The following requirements must be ensured by
the control logic:
the control logic:
the control logic:
the control logic:
the control logic:
•
Minimum time of standstill: 1 minute. Valid during
maintenance also!
Returning time of the control slide - CR3 (Y3)
energized
•
Maximum cycling rate 6 to 8 starts per hour!
•
Minimum running time desired 5 minutes!
•
Switch-over time part winding 0.5 seconds start
delta 1 second
Instruction for start delay timer with economizer
Instruction for start delay timer with economizer
Instruction for start delay timer with economizer
Instruction for start delay timer with economizer
Instruction for start delay timer with economizer
operation
operation
operation
operation
operation
The switching-on device F7 must ensure that the
refrigerant flow to the liquid sub-cooler is not switched
on until operating conditions have sufficiently stabi-
lized. This is achieved by using the solenoid valve Y6.
With frequent starting from high suction pressure, a
pressure switch should be sued. The set point should
be sufficiently above the nominal evaporating tempera-
ture in order to prevent the economizer solenoid valve
Y6 from short cycling.
For systems with relatively constant pull down cycles
(such as liquid chillers), an alternative is to use a time
relay. The delay time must then be checked individu-
ally for each individual systems.
Legend
Legend
Legend
Legend
Legend
B2
Control Unit
F1
Main fuse
F2
Compressor fuse
F3
Control circuit fuse
F4
Control circuit fuse
F5
High pressure cut out
F6Low pressure cut out
F7
Start delay timer “Economizer”
F8
Oil level switch (option)
F13
Thermal overload “motor” PW1