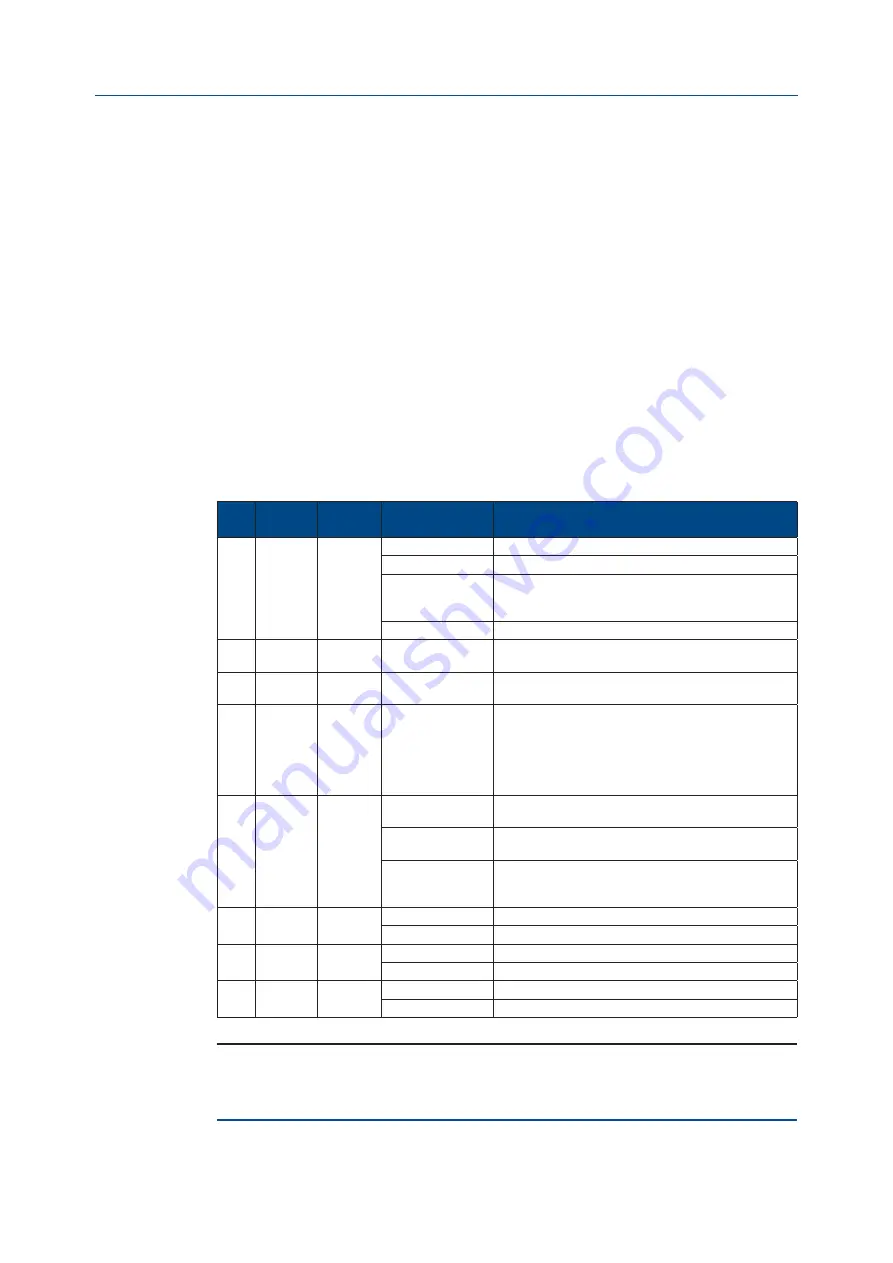
November 2021
Installation, Operation and Maintenance Manual
VCIOM-15590-EN Rev. 0
Commissioning
6
Section 3: Commissioning
Section 3: Commissioning
When commissioning a PROFIBUS-DP network, the devices on the PROFIBUS-DP have to
be parameterised and configured with the project configuration software of the control
system used (PROFIBUS configurator).
In this step, each subscriber connected to the PROFIBUS also has to be given a unique address.
The project configuration software first reads in the GSD file (General Station Description) of
the various actuators. The GSD file contains information about the device’s properties needed
by the master. The current GSD file can be downloaded at Emerson Global Sales Portal.
After that, the user can configure and parameterise each device on the PROFIBUS-DP.
This information is stored in the control system (DP master) and sent to the actuators
(DP slaves) each time communication starts up.
The following additional parameters become visible in the control unit for the Bettis RTS
actuator with the PROFIBUS option enabled.
Table 2.
Menu
Item
Subitem
Options
Explanation/Comments
P15.1 PROFIBUS PROFIBUS
0: disabled
PROFIBUS disabled
1: allow paramet.
Parameterisation by the master is allowed.
(2): ignore paramet.
Parameterisation by the master is ignored.
Only parameters set in the actuator control system are
effective (recommended setting).
3: deny paramet.
Parameterisation by the master is not allowed.
P15.2 PROFIBUS
Address
Channel A
0 bis 125
Setting of the bus address for the first, primary channel.
P15.3 PROFIBUS
Address
Channel B
0 bis 125
Setting the bus address of the second, secondary channel
(only with the option “PROFIBUS redundant”).
P15.4 PROFIBUS
Watchdog
time
0.0 – 10.0 s
(0.0 s)
Monitoring of the toggle bit transmitted from the master
(bit 7 in the command). With a bus watchdog time set,
this bit has to toggle within that time; otherwise there
is a bus watchdog error. At 0.0 s the watchdog function
is disabled, in which case toggling of the toggle bit may
be omitted.
P15.5 PROFIBUS
Setpoint
Source
(0): Standard
The set point is specified via PROFIBUS
(only relevant when the positioner is enabled)
1: Analog
The set point is specified by the analogue signal
(only relevant when the positioner is enabled).
2: Bus/Analog
With a fault-free bus, the set point is specified via the
PROFIBUS. With a bus error, the analogue value is
switched to (only relevant when the positioner is enabled).
P15.6 PROFIBUS
Status 2
(0)
Standard assignment for Status 2.
1 - 2
Reserved for future use.
P15.7 PROFIBUS
Status 3
(0)
Standard assignment for Status 3 (current event).
1 - 2
Reserved for future use.
P15.8 PROFIBUS
Status 4
(0)
Standard assignment for Status 4.
1-2
Reserved for future use.
NOTE
After changing an address, the control unit has to be briefly switched off and back on again
in order to apply the change.