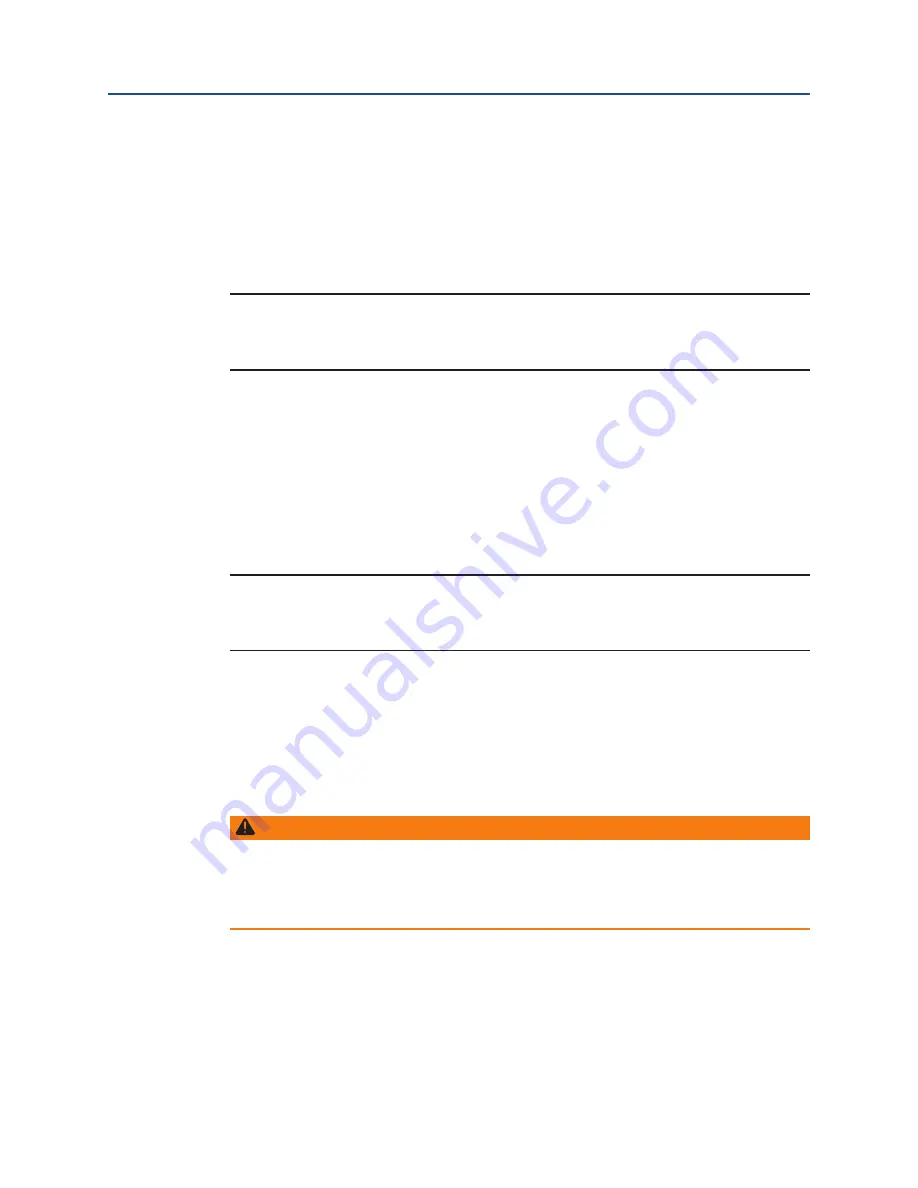
October 2015
Service Instructions
124842E Rev. C
21
Section 3: Actuator Reassembly
Actuator Reassembly
3�5
Actuator Testing
3�5�1
Leakage Test – All sources of leakage to atmosphere and across piston are to be
checked, using hydraulic pressure.
3�5�2
Cycle the actuator five times at 10% of the operating pressure, as listed on the
cylinder name tag under maximum pressure.
NOTE:
If excessive leakage across the piston remains, the actuator must be disassembled and the
cause of leakage must be determined and corrected.
3�5�3
Apply operating pressure as listed in step 3.5.2 to one side of the piston and allow
the actuator to stabilize.
3�5�4
Repeat the above procedure for the opposite side of the piston.
3�5�5
If an actuator was disassembled and repaired, the above leakage test must be
performed again.
3�5�6
Shell test the actuator as follows: Apply 1.5 times the pressure listed on the
cylinder name tag to both sides of the piston simultaneously for a period of two
(2) minutes.
NOTE:
If any leakage occurs during step 3.5.6 the actuator must be disassembled and the cause of
leakage must be determined and corrected.
3�5�7
If an actuator was disassembled and repaired, the above testing must be
performed again.
3�5�8
Shell Pressure Test – Optional pressure test could be performed on the actuator by
applying pressure to both sides of the piston simultaneously for a period of two (2)
minutes. If any leakage occurs across a static seal, the unit must be disassembled
and the cause of leakage determined and corrected.
WARNING: PED PRESSURE TESTING
The actuator's main pressure bearing parts will be tested in controlled conditions in
accordance with the requirement of PED by pressuring both sides of the piston to avoid
damage and over torquing of the actuator components. If further future testing in the field
is necessary, Emerson should be contacted for guidance.
3�5�9
After the actuator is installed on the valve all accessories should be hooked up and
tested for proper operation and replaced if found defective.