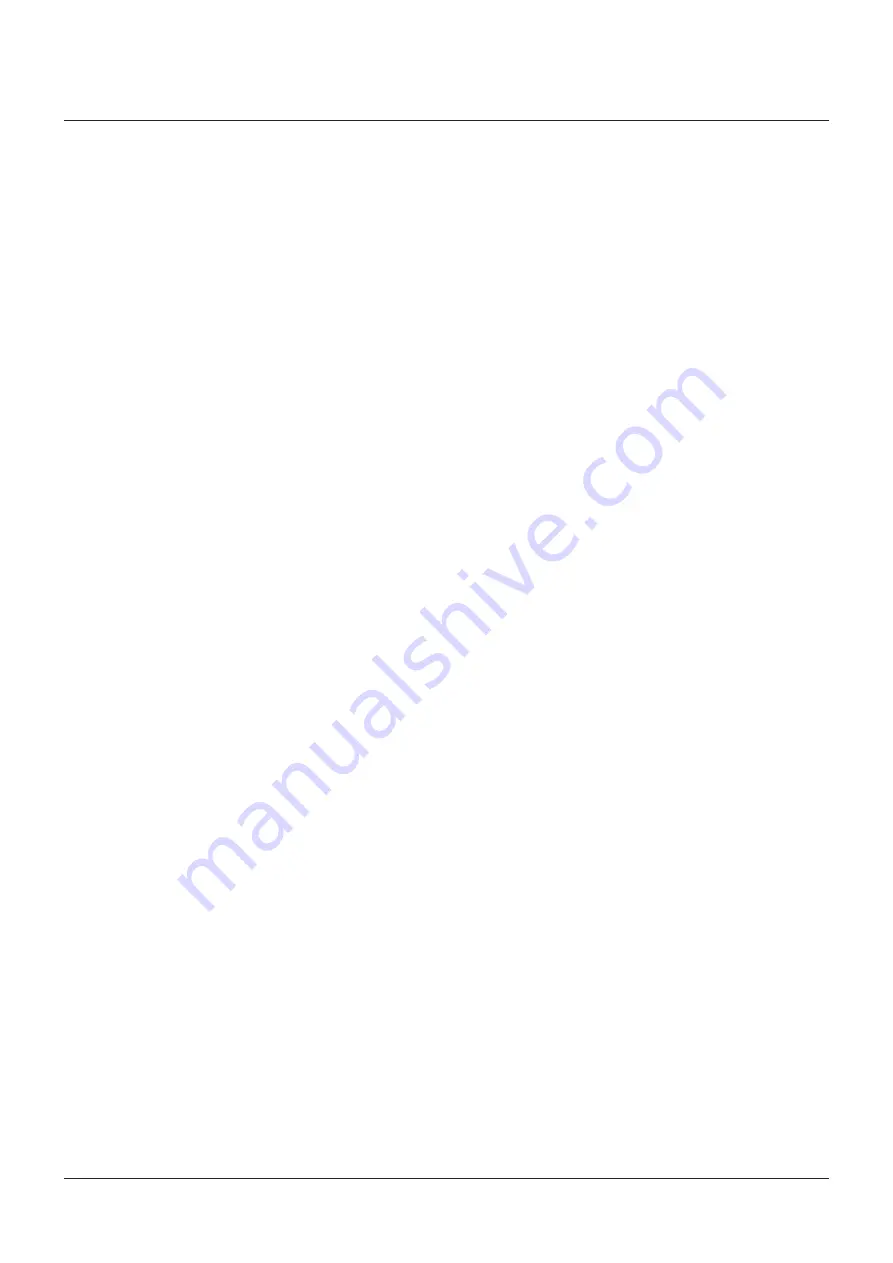
9
ANDERSON GREENWOOD
TYPE 9300H POSRV
INSTALLATION AND MAINTENANCE INSTRUCTIONS
Internals stack sub-assembly
Reference Fig (2)
31. Install the guide collar (200) up-side down
and tighten the wrench flats in the vise.
32. In the following order stack the internal
components on the guide collar (200).
33. Install the blousing plate (150) with the
convex bulged rim upward.
34. Install a diaphragm slipper (190).
35. Install the diaphragm (250).
36. Install 0.010” Teflon Diaphragm Spacer
(~3” diameter) (240).
37. Install the NAS flat washer ( rounded edges
down) (260).
38. Install diaphragm slipper (190).
39. Install the main seat plate with the concave
side upward. (140).
40.Install flat NAS washer (rounded edge down)
(260).
41. Install second 0.010” PTFE Washer
(~ 3” diameter) (240).
42. Install flat NAS washer (rounded edges
down) (260).
43. Install the white Expanded PTFE Seat
Cushion (170).
44. Install the Seat film (as required on the
B.O.M.) (180).
45. Install the one or more protector plates (160)
as required on Bill of Materials (B.O.M.)
Note: if more than one the larger plate goes
on first and then the smaller plate if they are
a different outside diameters.
46. Install the standard flat washer (rounded
edge down) (410).
47. Install the split lock-washer (370).
48. Install the Jam-nut with thread lock
compound and tighten (280).
Mating internals stack sub-assembly to cap &
guide rod sub-assembly
Reference Figure (7)
49. While the cap flange is still in the slightly
past vertical position slide guide collar with
stacked internals onto the guide tube and
push the internals all the way back to the
hub.
50. Install Aluminum cross bar (490) over the
all thread rod (530) and align over two of the
(
5
/
16
") mounting plate studs.
51. Install (
5
/
16
”) washers and hex nuts.
52. Install the ¼-20UNC all thread rod (530)
through the crossbar lift bushing (500) and
into the lower guide collar thread Fig 2 (200)
until wrench tighten (12 ft-lb max.). Hold
the lift bushing Fig. 7 (520) to keep it from
rotating.
53. Place the main valve lifting lugs Fig 8 (540)
on the remaining (2) lower mounting plate
studs using the slotted hole and secure
them with the other (2)
5
/
16
Hex-nuts. Use
opposite slots on each side to maintain
lifting symmetry.
Installing cap and internals stack sub-
assemblies into body
Reference Figure (8)
CAUTION
Never allow the slings to come in contact with the
pilot or tubing. Use a spreader bar on the sling
to prevent contact. Failure to comply may cause
equipment damage.
54. Using a double chain, attach the chain to
lifting lugs (540) and carefully lift , remove
the cap and internals sub-assembly from
the holding device. (See illustration Fig. 7).
55. The cap flange face is now horizontal with
gasket surface facing downward allowing
the flat diaphragm Fig 1 (250) to hang
downward.
56. Using rubber glove apply thin film of
lubricant to the machined cap flange face
( this is to protect the diaphragm during
installation).
57. Using a crane, two hook chain in the central
lifting lugs, center the cap sub-assembly
over the valve body.
58. Lower the cap and internals assembly onto
the valve body flange assuring that the
diaphragm Fig 1 (250) perimeter is held
taughtly outward from the four corners.
59. Check that the Teflon encapsulated body
O-ring (Fig 1) (290) is in place before lowering
the cap sub-assembly onto the body.
60. Carefully rotate the cap to further align the
bolt holes and check for correct O-ring (Fig 2)
(290) position again by looking through the
bolt holes all around before resting the cap
flange and diaphragm on the main valve.
61. Stretch the diaphragm ( 250) outward until
taught all the way around.
62. Remove the crane and two hook chain.
63. Install the four hand grips about 90 degree
apart to hold the cap and the body together
with some low tension.
64. Using a
7
/
16
” box end wrench slowly rotate
the lift-bushing Fig (520) CCW allowing the
internals assembly to drop as far as it will
and then exerting some additional CCW
torque until the main pallet to ensure seat
engages the nozzle while pulling in the
diaphragm (main seat closed position-cap
will separate from the body approx.
1
/
16
"-⅛").
65. Slowly rotate the wrench in the CW direction
raise the internal assembly up against
the upper stop and then CCW a second
time down to the seat (after this step the
diaphragm will be fully pulled in as far as
it can be to the closed position-cap will
separate from the body approx.
1
/
16
"-⅛").
66. Using a small razor knife cut four holes in the
diaphragm Fig1 (250) between the cap and
body flange through the cap clearance holes
approximately 90 degrees apart and install
four cap hex bolts and washers Fig1 (360,370)
to loosely hold the cap in the indexed position.
67. Using the razor knife or hole punch (
5
/
16
" dia)
cut and remove remaining material in each of
the bolt holes and install remaining cap bolts
and washers Fig1 (360,370). Install the longer
Hex bolts at the lifting lugs (540) locations on
the side of the body, if applicable.
68. Remove the lifting lugs (540) from the lower
mounting plate (350) and reinstall them on the
machine surface on the bottom side of main
valve flange as shown on Fig. 8.
Install the nut and lock washer(270,390) on the
lower lifting lug face.
Note: these bolts are extra long and are
extra strength.
69. Removing tooling (
5
/
16
” nuts/cross-bar/
threaded rod) from lower pilot mounting
plate thread and store. Reduce tension
in the lifting bushing Fig 7 (520) before
removing all thread rod (Fig 7 (530) .
70. Index or rotate the lower pilot mounting
plate Fig6 (350) by loosening bolts (400) one
to two turns CCW ea. so that the mounting
plate studs are approximately split on the
outlet flange centerlines (set the pilot on the
mounting plate to align the inlet pipe with
the inlet pipe u-bolt and bracket). Once Pilot
inlet pipe/Pilot is aligned, remove the pilot
and tighten the four mounting plate bolts
Fig 6 (400).
Note: Once tightened the lower mounting
plate must not be able to rotate by hand.
71. Once tightened, re-Install the pilot and inlet
tubing and secure the bracket U-bolts (not
shown) and pilot mounting plate nuts and
washers Fig1 (390, 370).