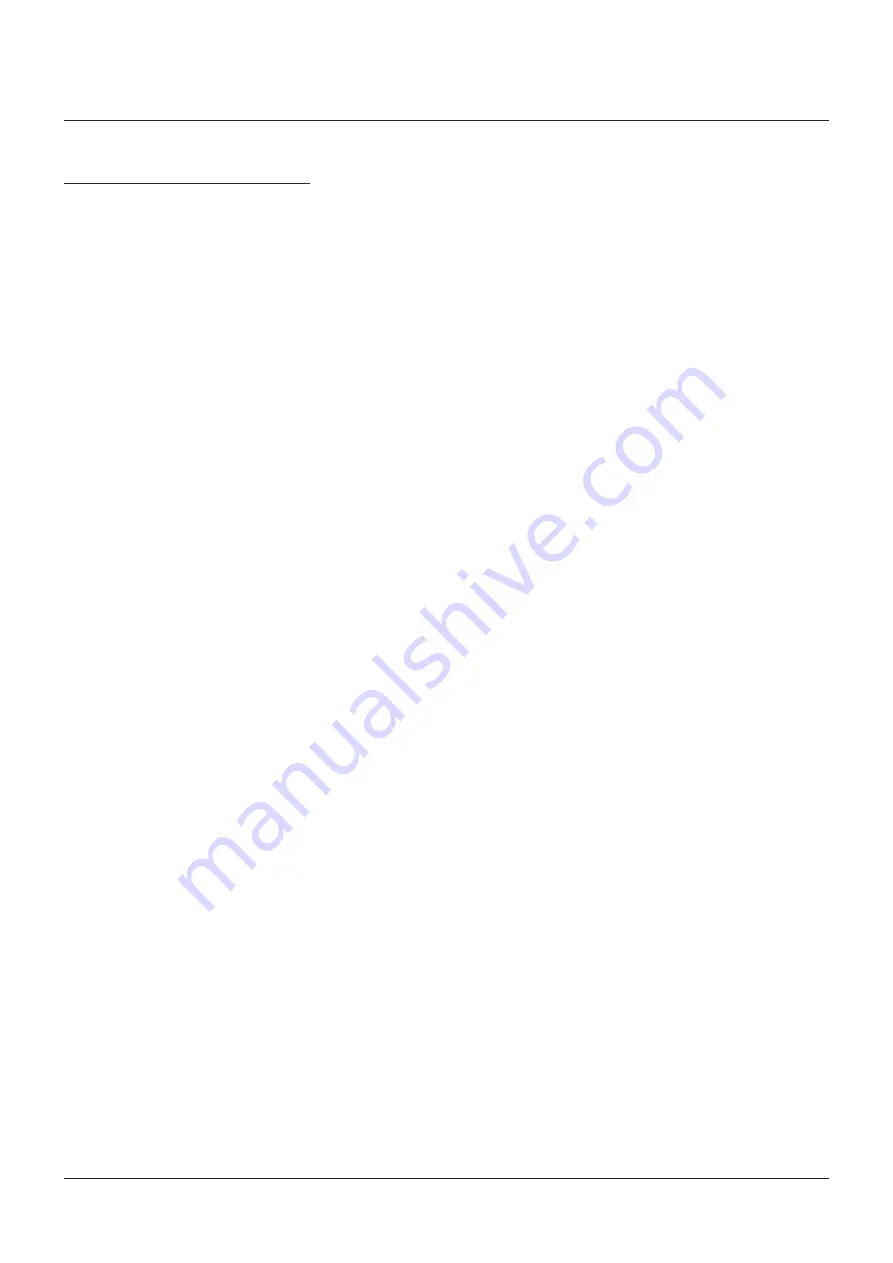
22
ANDERSON GREENWOOD
TYPE 9300H POSRV
INSTALLATION AND MAINTENANCE INSTRUCTIONS
4 FUNCTIONAL TESTING OF COMPLETE
ASSEMBLY OF MAIN VALVE AND PILOT
WARNING
Failure to follow the installation, operation or
maintenance instructions for a Emerson product
could lead to serious injury or death
from explosion or exposure to dangerous
substances.
To reduce the risk:
• Comply with all information on the product, in
this manual, and in any local and national codes
that apply to this product.
• Do not allow untrained personnel to work with
this product.
• Use Emerson parts and work procedures
specified in this manual.
WARNING
Use only genuine Anderson Greenwood
replacement parts. Components that are not
supplied by Emerson Automation Solutions
should not, under any circumstances, be used
in any Anderson Greenwood valve because they
may void your warranty, might adversely affect
the performance of the valve and could cause
personal injury and property damage.
WARNING
When the pressure relief valve is under pressure
never place any part of your body near to the
outlet/exhaust of the valve.
Failure to follow these instructions may result in
death or serious injury.
CAUTION
The control valve body and piping may be
extremely hot or cold. Wear personal protective
equipment appropriate to the situation when
working with the control valve. Adhere to your
company's safety standards and practices. Failure
to comply may cause serious injury
4.1 General
Assemble the pilot to the main valve, and
install remaining tubing and accessories. The
complete valve assembly should be leak tested
for internal and external leaks using a pressure
equal to 30% and 90% of set.
4.1.1 Leakage check - pressure relief valves
Apply pressure to the inlet equal to 30%
of the set pressure. Check for leakage
at the main valve seat, no visible leakage
shall occur. Hold time is 1 minute.
Slowly increase the inlet pressure to 90%
of the set pressure. Check for leakage at
the cap seal, casting, pilot support pipe
and supply tube and other applicable
connections using leak test solution and
at the main valve seat. No visible leakage
shall occur for a hold time of 1 minute.
4.2 Field test instructions for flowing
modulating action pilots
4.2.1 General
An optional field test accessory is
available for checking the positive set
pressure without removing the valve from
service. The field test accessory consists
of a 3-way ball valve to allow the pilot to
sense pressure from either the process
or from the test gas source.
A standard bottle of nitrogen equipped
with a pressure regulator, block
valve, pressure gage, and convenient
length of high pressure flexible hose
is recommended for testing. A set up
similar to that shown in Figure 15 should
be used. Such a test kit is available from
Anderson Greenwood under the part
number 04.4812.001 plus additional dash
numbers for the pressure gages required.
4.2.2 Field test procedure for flowing modulating
pilots
1. Connect the gas bottle as shown in
Figure 15.
2. Close vent valve “C”.
3. Open block valve “B” to supply regulator.
Note: Regulator pressure should be set
at 0.
4. Connect bubble tester bottle to pilot
exhaust vent.
5. Increase pressure at field test port to
slightly above tank pressure by slowly
increasing regulated pressure.
6. Open field test valve “A” and slowly
increase regulator pressure until bubbles
are seen in the bottle. That pressure will
be within 10% of the set pressure.
7. To remove the test set-up, close valves
“A” and “B” and open valve “C”.
4.1.2 Leakage check - vacuum relief valves
Valves equipped with vacuum pilots
shall be leak tested per 4.1.1 on
positive pressure with the set pressure
equal to the reciprocal of the vacuum
set pressure. Valves with weighted
diaphragms shall be tested for leakage at
50% of their weighted set.
4.1.3 Back flow preventers and/or field test
The use of some field test connection or
back flow preventers necessitates the
use of check valves. These valves shall
be installed per the applicable assembly
drawings and in the free flow direction
shall open at less than .5" W.C. The check
valves may be tested for forward flow
either before or after assembly at the
shops option. The output check valve of
back flow preventers shall be checked for
zero leakage per 4.1.1 paragraph 2.