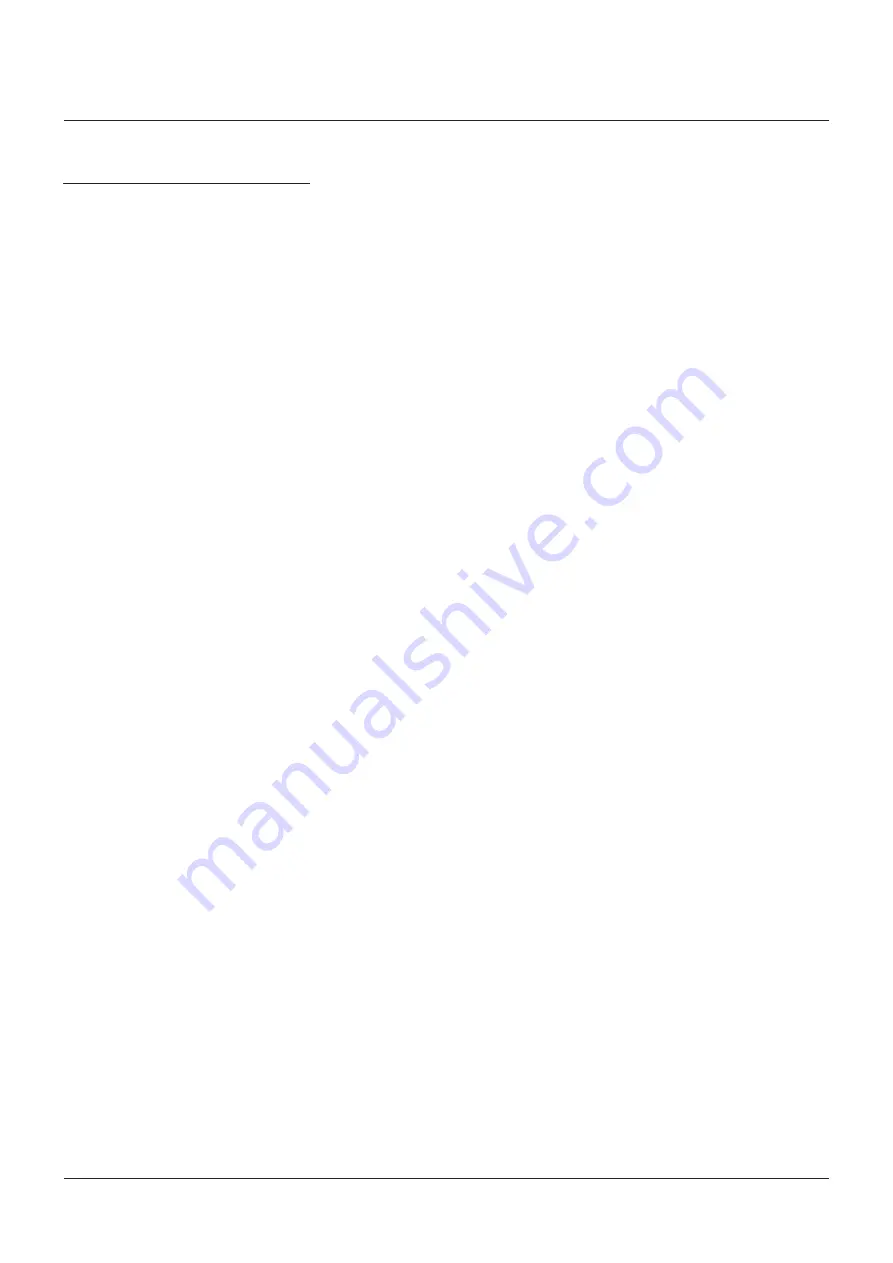
13
ANDERSON GREENWOOD
TYPE 9300H POSRV
INSTALLATION AND MAINTENANCE INSTRUCTIONS
3 PILOT DISASSEMBLY FOR FLOWING
MODULATING PILOTS (TYPES 91, 93, AND 93T)
Refererence Figures 9 thru 13
WARNING
Failure to follow the installation, operation or
maintenance instructions for a Emerson product
could lead to serious injury or death from
explosion or exposure to dangerous substances.
To reduce the risk:
• Comply with all information on the product, in
this manual, and in any local and national codes
that apply to this product.
• Do not allow untrained personnel to work with
this product.
• Use Emerson parts and work procedures
specified in this manual.
WARNING
Avoid personal injury from sudden release of
process pressure. If the process media starts to
escape from the valve or pilot, STOP IMMEDIATELY!
The escape of process media indicates that the
valve has NOT been properly vent, or process
pressure is trapped in the valve body nor pilot.
Check with your process or safety engineer for any
additional measures that must be taken to protect
against process media.
The pilot disassembly instructions and soft
goods vary between pilot types. Pay particular
attention to orientation of parts and materials.
The 93T pilot has all T eflon
®
soft goods
including diaphragms, and its maximum set
pressure is 15 psig. The 91 pilot has T eflon
®
soft goods with stainless steel (SS), Hastelloy
®
,
and T eflon
®
diaphragms, and its set pressure
ranges from 16 psig to 50 psig. The 93 pilot is
different from the 93T and 91 pilot in that it uses
elastomer seat, seals, and diaphragms.
1. Remove cap (760) and adjusting screw (790)
and adjusting screw seal (720) for vacuum
pilot. Remove bonnet bolts (770), seals (700)
for vacuum pilot, bonnet (200), spring (840)
and spring washer (820).
2. On Types 91 and 93T pilots, loosen boost
tube fitting (310) on boost tube (320) at boost
tube connector bolt (270). Refer to Detail B.
Remove boost tube connector nut (300),
washer (290), lower boost tube seal (590),
seal retainer (280). Let these three parts
slide down boost tube. Remove boost tube
connector bolt (270), upper boost tube seal
(590) and seal retainer (280).
3. On Type 93 pilot, loosen boost tube fitting
(310) on boost tube (320) at boost tube
connector bolt (270). Refer to Detail B.
Remove boost tube connector nut (300),
washer (290), lower boost tube seal (600)
Let these three parts slide down boost tube.
Remove boost tube connector bolt (270) and
upper boost tube seal (590).
8. Remove parts in the following order: hex
spacer (120), sense plate (150), sense
diaphragm (510), upper gasket (650), sense
spacer (140), boost plate (160), spacer
ring (230), diaphragm gasket (620), boost
diaphragm gasket (510), boost spacer (130),
check plate (560) and spindle seal (660).
(See Figure 12, Detail A).
9. Remove boost tube (320) from body (100)
and lower boost tube seal (590/600(93T))
from boost tube (320).
10. Remove spindle diaphragm (500) and gasket
(690) for 93T pilot and spindle/disc assembly
(550) from body (100).
11. Remove spindle diaphragm plate (170) and
shim washer(s) (490) from spindle/seat
assembly (550).
Note: shim washer(s) may not always be
used in assembly (550).
12. Refer to Detail A. For the 93T pilot seat
assembly, remove the retainer ring (430)
and seat retainer (420) from the spindle/disc
assembly (550). Remove the seat (570).
13. Remove blowdown bushing (390) and
blowdown seal (630) from body (100).
Note: the blowdown screw retainer (380)
is a loose fit on the blowdown adjustment
screw (350). Be prepared to catch it when
the bushing (390) is removed from the
body (100).
14. Loosen the blowdown screw locknut (370)
and remove the blowdown adjusting screw
(350) and seal (630) from the bushing (390).
15. Remove the vent (800) from the body (100).
Note: it is not necessary to remove the
filter screen (400) or nozzle (110) from the
body (100).
16. Remove the upper mounting plate (930),
bolt seals (610), plate seals (940) from body
(100) by unthreading the body bolts (340).
17. Clean all parts and replace all soft goods.
The spindle/seat assembly (550) is factory
assembled and must be replaced as a unit.
If the nozzle (110) is nicked or scratched, it
should be replaced. To remove it, use a deep
socket.
4. Remove case bolt nuts (260), washer (250)
and bolts (240). Remove upper case (210).
5. On Types 91 and 93T pilot. Hold hex spacer
(120) with a shortwell ¾" socket that has the
ratchet area bored out and inserting another
socket into the bored out hole, loosen.
6. Remove parts in the following order: hex
spacer (120), sense plate (150), upper
gasket (650), sense diaphragm case gasket
(650), spindle gasket (680), sense spacer
(140), boost plate (160), spacer ring (230),
diaphragm gasket (620), boost diaphragm
gasket (680) (See Figure 12, Detail A).
7. On Types 93 pilot, hold hex spacer (120) with
a shortwell ¾" socket that has the ratchet
area bored out and inserting another socket
into the bored out hole, loosen.