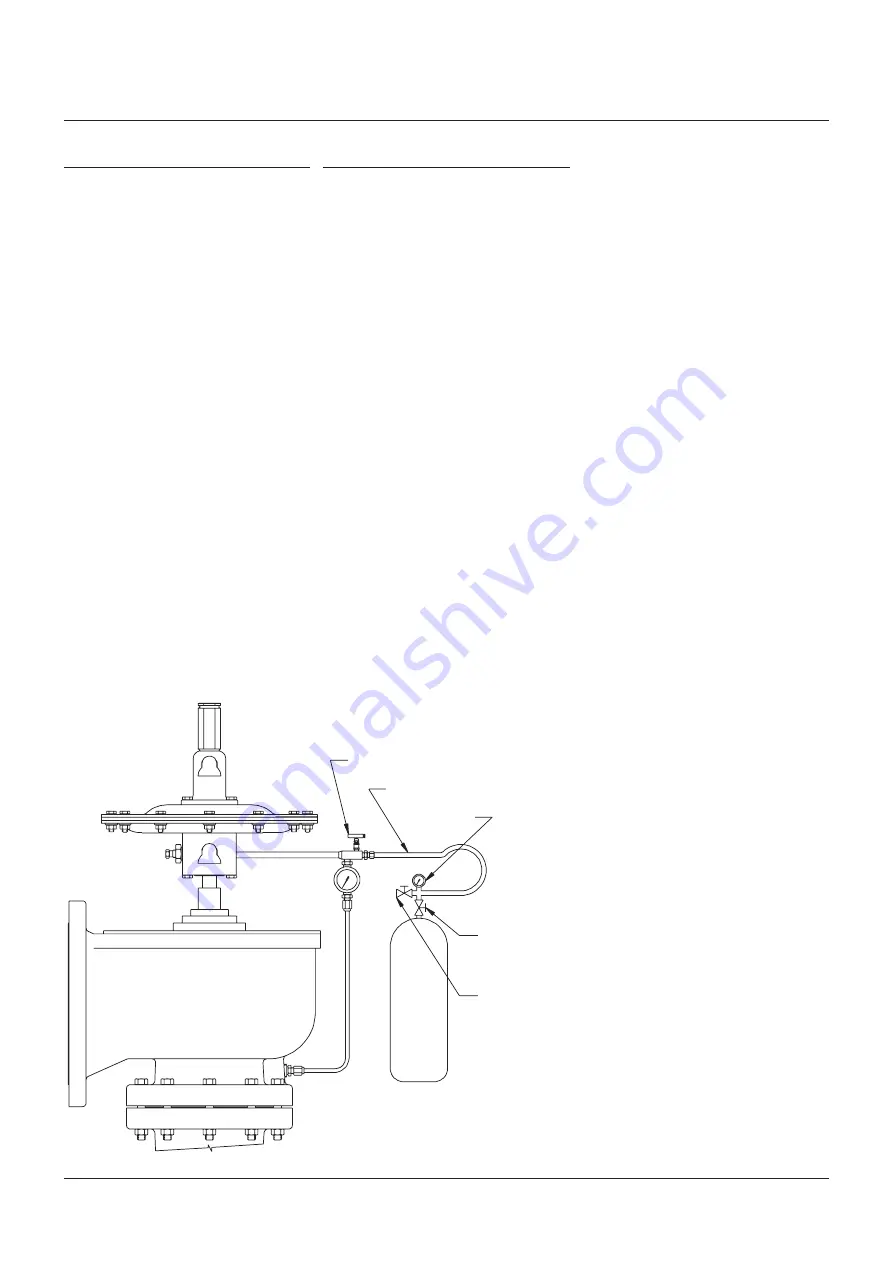
11
ANDERSON GREENWOOD
TYPE 91 AND 94 PILOT OPERATED SAFETY RELIEF VALVES
INSTALLATION AND MAINTENANCE INSTRUCTIONS
6 LEAK TESTING ASSEMBLY
6.1 General
The complete valve assembly should be leak
tested for internal and external leaks using a
pressure equal to 10% and 90% of set.
6.2 Internal leak test
Nozzle
Use a piece of wide masking tape to cover
the lower part of the main valve outlet, taped
across the opening 2” to 3” (50 to 76 mm) high.
Pour in enough water to cover just the base of
the nozzle. If bubbles are detected, the nozzle
seal is leaking.
Main seat
Pour in enough water to just cover the bottom
of the bellows and seat plate.
If bubbles are detected, the main seat is
leaking. Nozzle or seat may be damaged or
the bellows may not be seating squarely on
the nozzle. Improper bellows seating may
be due to incorrect assembly of cap to body.
Refer to Section 2
6.3 External leak test
Following the internal leak test, check for
external leakage by applying leak test solution
to all joints and seals. Tighten bolts or fittings
as required.
7 PILOT SET PRESSURE FIELD TEST PROCEDURE
7.1 General
The pilot set pressure can be checked in
the field by applying an external test pressure
to the pilot through the field test hand valve as
shown in Figure 9.
NOTE
If the process pressure at the time of test is less than
approximately 30% of the pilot set pressure, the main
valve will not open. If the process pressure is greater
than 30% and the main valve must remain closed,
temporarily replace the pilot exhaust vent with an
orifice plug having an orifice diameter of .040”/.060”
(1.02 mm/1.52 mm). This orifice must be removed
on completion of field testing as it prevents the main
valve from opening.
7.2 Procedure
1. Connect test gas bottle as shown in Figure 9.
2. Close vent valve “C”.
3. Open field test valve “B”. Test gauge will
read process pressure.
4. Open block valve “A” SLOWLY to increase
pressure until pilot “pops”. The set pressure
will be the pressure indicated on the test
gauge at the time of pop.
5. To remove test set up, close valves “A” and
“B”, open valve “C”.
FIGURE 9
Field test valve “B”
Flexible hose
Block valve “A”
Block valve “C”
Nitrogen
bottle
Test gage