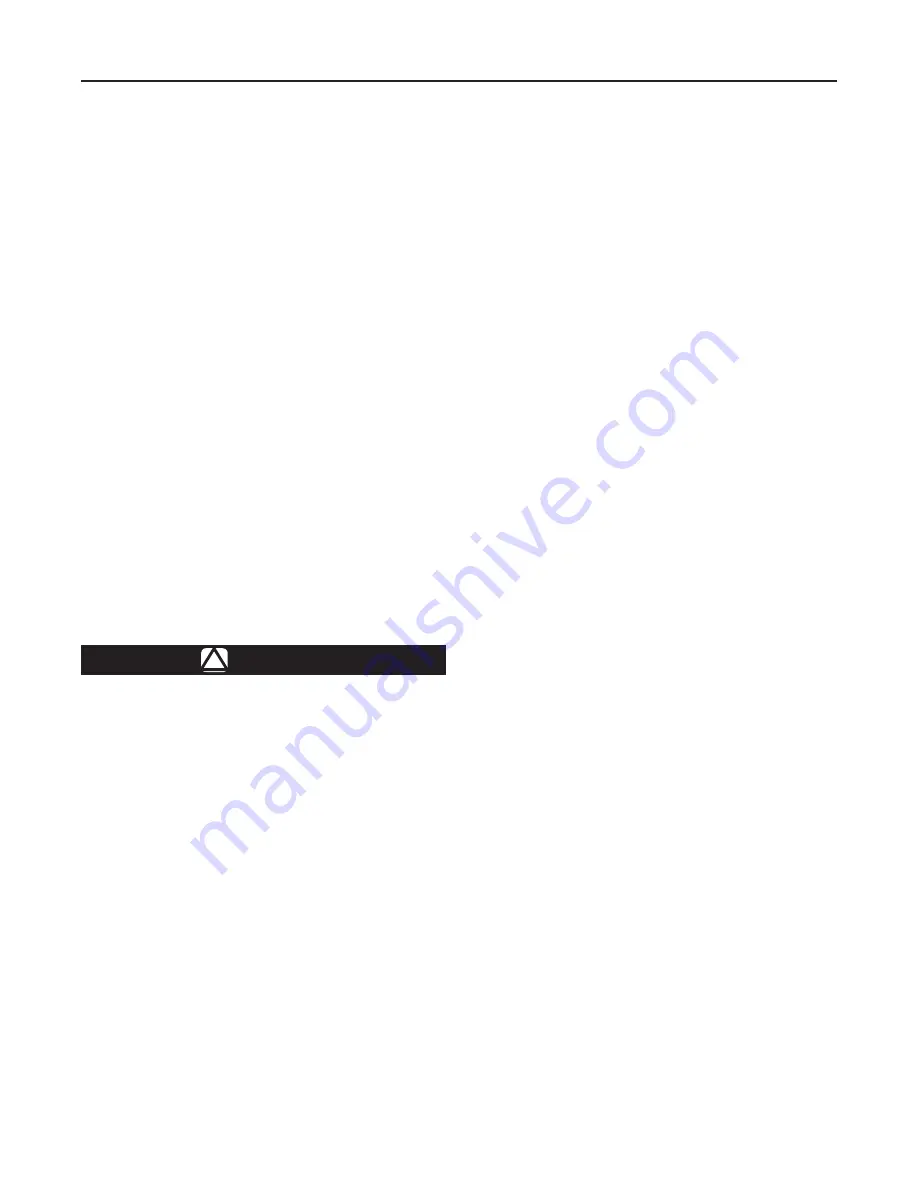
Types 63EG and 1098-63EGR
8
are referenced in Figure 10. Key numbers for both
the complete Type 63EGR main valve and its trim
package are referenced in Figure 11. Replacement
trim package assembly numbers are listed in the
parts list.
Note
All disassembly, trim change and
reassembly steps in this section may
be performed with the relief valve in the
main line. The pilot and its pipe nipple
need not be removed for trim package
replacement with the Type 63EGR main
valve but must be removed with the
Type 63EG main valve.
1. Remove the cap screws (key 3) on a cast iron or
steel body or remove the stud bolt nuts (key 29,
not shown) on a Stainless steel body. Pry the body
flange (key 2) loose from the valve body (key 1)
and lift out the trim package.
2. Perform any required inspection, cleaning or
maintenance on the exposed surfaces of the
body interior or trim package. Replace the gasket
(key 4) or cage O-ring (key 17) as necessary.
3. On a factory-built replacement trim package with
indicator assembly, check indicator zeroing by
unscrewing the indicator protector (key 19) and
seeing if the flange on the indicator nut (key 22)
lines up evenly with the bottom marking on
the indicator scale (key 18). If not, remove the
indicator scale and separate the indicator nut and
hex nut (key 8). Hold the indicator scale against
the indicator fitting (key 5) with the scale base
resting against the shoulder of the fitting and turn
the indicator nut until its flange is aligned with
the bottom scale marking. Then lock both nuts
against each other and install the indicator scale
and protector.
Note
In the following step a Type 63EG trim
package must be installed so the body
flange and body side tappings are
aligned, but a Type 63EGR trim package
requires no special orientation in
the body.
Backpressure Installations
Slowly close the upstream shutoff valve while opening
the bypass valve. Then close the downstream
shutoff valve and open both vent valves to release all
pressure from the main valve and pilot.
Maintenance
Relief valve parts are subject to normal wear and
must be inspected and replaced as necessary. The
frequency of inspection and replacement of parts
depends upon the severity of service conditions or the
requirements of local, state and federal regulations.
Due to the care Emerson™ takes in meeting
all manufacturing requirements (heat treating,
dimensional tolerances, etc.), use only replacement
parts manufactured or furnished by Emerson.
Lubricate the stem O-rings on the Type 1098
actuator annually, using the grease fitting (key 28,
Figure 13). Stem O-rings can be checked for damage
during normal operation by line pressure leakage
or unexpected grease extrusion from the actuator
vent (key 27, Figure 13). Unless otherwise specified,
lubricate all O-rings, gaskets and seals with a good
grade of general-purpose grease and install gently
rather than force into position. Update nameplates to
accurately indicate any field changes in equipment,
materials, service conditions or pressure settings.
Avoid personal injury or damage
to property from sudden release
of pressure or uncontrolled gas or
other process fluid. Before starting
disassembly: isolate the relief valve from
system pressure, release all internal
pressure and vent the pilot(s) and main
valve diaphragm loading pressure.
Type 63EG or 63EGR Main Valve
Replacing Quick-Change Trim Package
Perform this procedure if the entire trim package
(Figure 10 or 11) or only the gasket or cage O-ring
(key 4 or 17, Figure 10 or 11) will be replaced if
exposed surfaces of the trim package or body interior
will be inspected or cleaned. Key numbers for both the
complete Type 63EG main valve and its trim package
!
WARNING