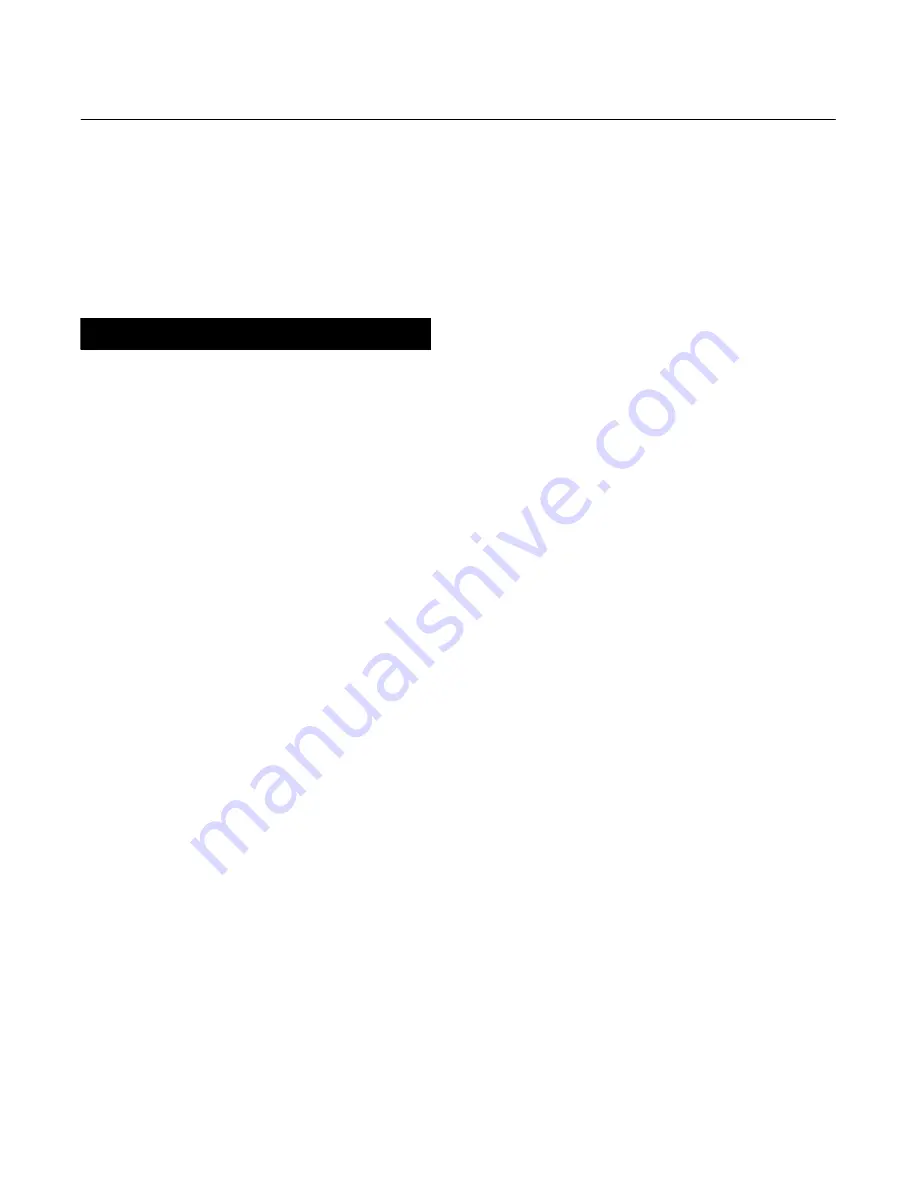
1051 & 1052 H & J
Instruction Manual
Form 5587
November 2006
20
2. Mark the orientation of the lever (key 27) with
respect to the output shaft (key 87). This marking is
used during reassembly to allow for proper
lever/output shaft positioning. When the lever and
output shaft are properly marked, heat the hex nut
(key 19) to 177
_
C (350
_
F) long enough for the
thread-locking adhesive (high strength) (key 77) to
lose its holding strength. Then, remove the cap
screw and hex nut (keys 18 and 19).
CAUTION
If necessary, use a wheel puller to
remove the lever (key 27) from the
output shaft (key 87). You may tap the
wheel puller screw lightly to loosen the
lever, but hitting the screw with
excessive force could damage the
operated equipment.
3. Loosen the cap screw (key 28) and remove the
lever (key 27) from the output shaft (key 87).
4. For an actuator with a J mounting adaptation.
a. Unscrew the cap screws (key 23), and remove
the actuator housing (key 20) from the mounting
bracket (key 22).
b. Rotate the actuator housing to the new
position (1, 2, 3, or 4).
c. Secure the actuator housing to the mounting
bracket with the cap screws (key 23). Tighten the
cap screws to the torque value listed in table 10.
5. For an actuator with an H mounting adaptation.
a. Unscrew the cap screws (key 78) and loosen
the actuator assembly from its mounting bracket.
b. Rotate the actuator housing to the new
position (1, 2, 3, or 4).
c. Secure the actuator housing to the mounting
bracket with the cap screws (key 78). Tighten the
cap screws to the torque value listed in table 10.
6. Referring to the alignment marks that were made
in step 2, install the lever (Key 27) onto the output
shaft (key 87) as follows:
a. If the new actuator position is 90 degrees
clockwise from the previous actuator position,
install the lever so that its orientation mark is
located 90 degrees clockwise from the mark on
the output shaft.
b. If the new actuator position is 90 degrees or
180 degrees counterclockwise from the previous
position, install the lever so that its orientation
mark is located either 90 degrees (for 90
degrees) or 180 degrees (for 180 degrees)
counterclockwise (respectively) from the mark on
the output shaft.
c. Slide the lever onto the output shaft with the
bolt holes in the lever aligned as closely as
possible with the hole in the rod end bearing
(key 17). Then, temporarily rotate the lever and
output shaft until the rod end bearing no longer
interferes with further installation of the lever, and
slide the lever as far as it can go onto the output
shaft. Clamp the lever to the output shaft with the
cap screw (key 28). Tighten the cap screw to the
torque value listed in table 10.
d. Rotate the lever and output shaft back to the
original position, and then adjust the rod end
bearing so that it can be attached to the lever.
7. Apply thread-locking adhesive (high strength)
(key 77) to the threads of the cap screw (key 18).
8. Connect the lever (key 27) and the rod end
bearing (key 17) with the cap screw and hex nut
(keys 18 and 19). This connection can be aided by
stroking the actuator from its up travel stop with a
regulated air source. Tighten the cap screw to the
torque value listed in table 10.
9. Note the position of the valve body or other
operated equipment and direction of rotation.
Position the travel indicator (key 37) accordingly.
Replace the cover (key 33), and secure it with the
cap screws and washers (keys 34 and 63). If the
holes in the cover and housing (key 20) do not align,
use a regulated air source to move the actuator
slightly off the up travel stop. If hole alignment
cannot be obtained in this manner, temporarily
loosen the cap screws (key 23), and shift the
housing slightly. Do not stroke the actuator while the
cover is off. Then, tighten both sets of cap screws to
the torque values listed in table 10.