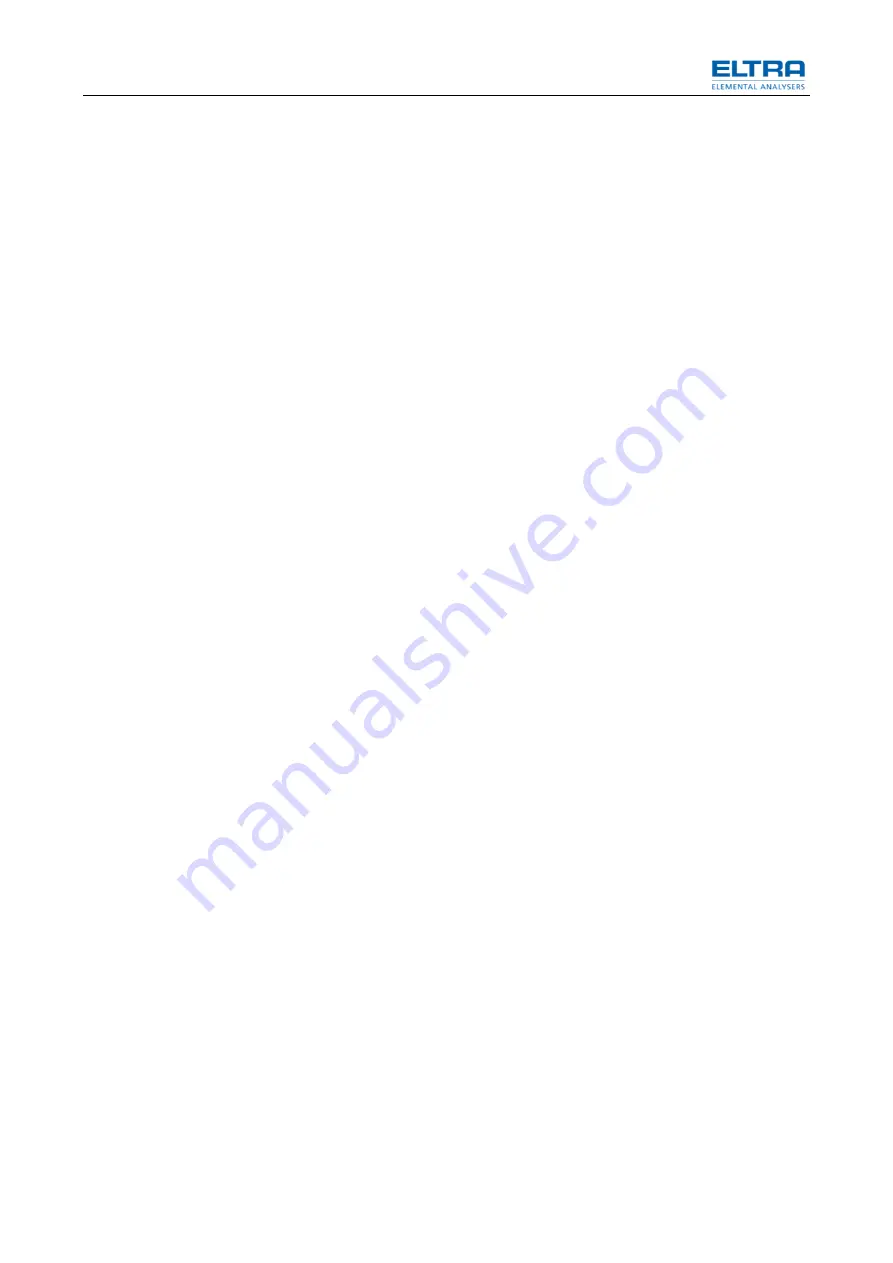
Maintenance
24
4 Maintenance
4.1 General information
–
Replace the magnesium perchlorate of the moisture trap of the
furnace after 150 analyses. See chapter “Front panel illustration” and
“Filling the reagent tubes”. In order to save material, replace first the
upper half. The next time replace the whole of the magnesium
perchlorate. This is based on the analysis of coal samples. It is not
necessary to replace the glass wool, unless it is penetrated by dust
and particles from the magnesium perchlorate.
–
The content of the oxygen pre-cleaning glass tube on the analyzer’s
front panel, see chapter
every 300 analyses. The depleting of these chemicals depends on the
purity of the carrier gas used. The CO2 absorber in the upper half of
this glass tube changes its color from black to grey after saturation.
The moisture trap in the lower half doesn’t change its color. When this
chemical is depleted, its particles stick together. It can be recognized
visually.
NOTICE
According to our experience in most cases when users report deviation of the
results, the problem is solved by replacing the magnesium perchlorate. This means
that the importance of the condition of the chemicals is underestimated.
The following chemicals are used:
–
Magnesium perchlorate (anhydrone)
as moisture absorber
–
Sodium hydroxide (ascarite)
as CO2 absorber
The chemicals are replaced when they are saturated.
It is not possible to dry the magnesium perchlorate and use it again, as it is
chemically changed after reacting with the moisture. The saturation of the sodium
hydroxide changes its color (it turns to light grey).
The magnesium perchlorate is saturated if its particles do not move when tapping
on the glass tube. It is essential to change the absorber before it becomes cloggy.
The moisture absorber should be checked every 100-200 induction analyses and if
necessary, it should be replaced (glass tube underneath the metal filter).
Please refer to the following schematics to identify the glass tubes on the analyzer.
In addition to the reagents in the glass tube, fill the bottom end of the tube with
glass wool. One should pay attention that the glass wool should be only as thick as
necessary, otherwise the gas flow can be choked. Under no conditions should the
amount of glass wool be less than that shown in the following schematics,
otherwise fine particles of magnesium perchlorate can pass through the glass wool
layer blocking the hole of the fitting underneath.
It should be pointed out that magnesium perchlorate is a very strong oxidizing
material.
At both ends of the glass tube, you should leave sufficient space for the gas
connections to be fitted. The free space at the tube ends serve as sealing space.
They must be cleaned after filling. The O-rings must be cleaned. Both the O-rings
as well as the sealing areas of the tube must be greased with high vacuum silicon
grease. This will be easier to assemble or disassemble and further it improves the
sealing of the glass tubes.
Make sure that the O-rings are completely sealed around the glass tubes, by
looking at the imprint of the O-ring on the inner surface of the glass tube. Check
whether there are fibers of glass wool trapped between O-ring and glass tube. This
causes leakages.
Summary of Contents for CS-580A
Page 3: ...3 ...
Page 38: ...Function description 38 Fig 14 Gas flow ...
Page 57: ......
Page 58: ......
Page 59: ......