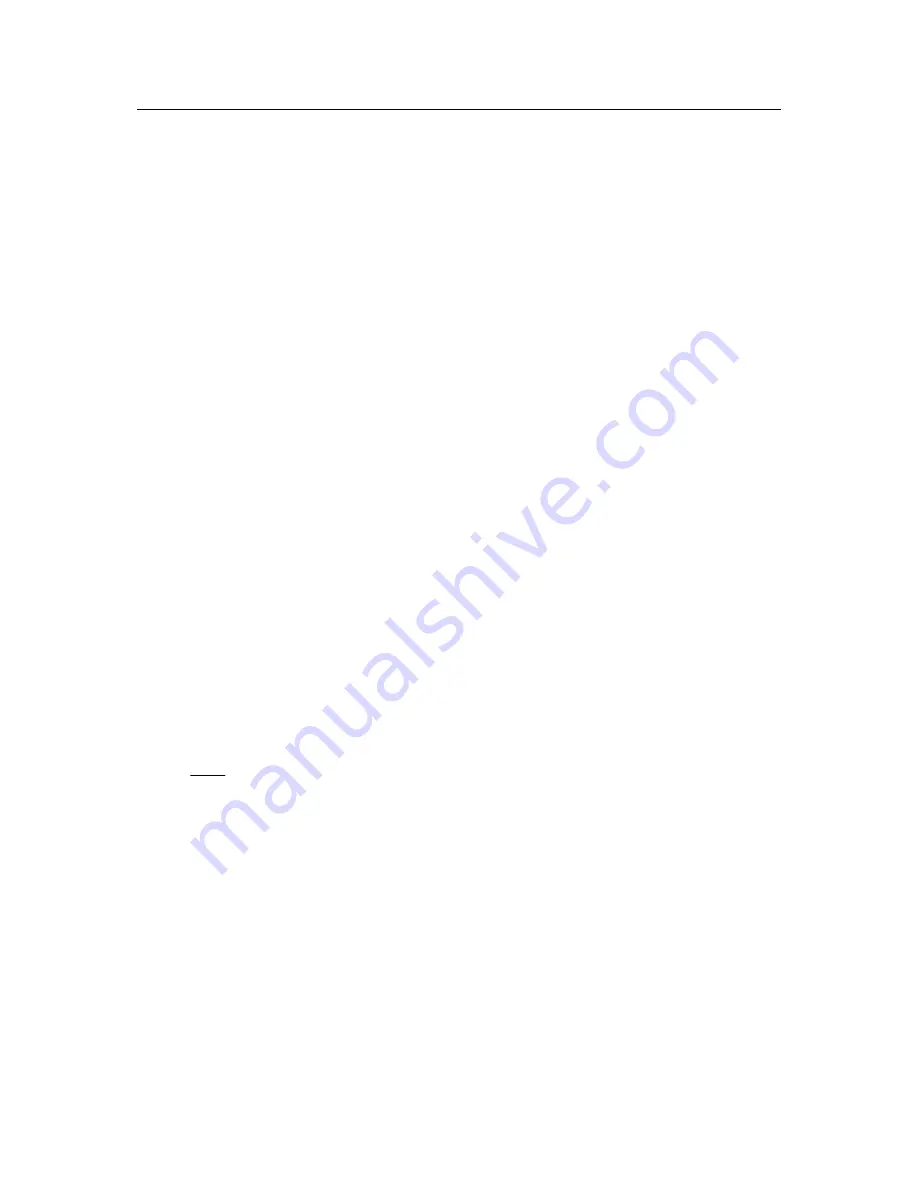
Model 2000 Flow Computer Instruction Manual
2.0
GENERAL
DESCRIPTION
Model 2000 issue 21
Page No
45
As an alternative to the Digital inputs described in paragraph 2.5.10 to indicate that a Grab Sampler Can is full the Model
2000 can also accept current input signals for sample can level indication this is fed into an single sided amplifier and having
a response time of approximately 470ms.
Input current:
4mA. to 20mA.
Input resistance:
100
Ω
To interface with the hazardous area where intrinsically safe transmitters are used a safety barrier must be used. The Input
is calibrated as a percentage of full indication and an alarm indication occurs when a preset level (percentage) is exceeded.
2.5.
OUTPUT SIGNALS
2.5.1.
ANALOGUE OUTPUT SIGNALS
Four analogue output signals are provided, on each fitted Output board, and these can be selected to be proportional to any
of the items in the Line Conditions selection list. All are current output signals and can be selected to be either 0 to 20mA or
4mA to 20mA or 0 to 24mA by selecting the appropriate links for each output on the output board (See section 4.6 for link
position details). The maximum load impedance that can be connected to an output to give 24mA is 500
Ω
. The minimum
load impedance that can be connected to any output is 50
Ω
.
Associated with each output are the Maximum and Minimum scaling factors.
O/Px
selects the function of the output from the above list
O/Px mn
scales the min. output i.e. 0mA. or 4mA.
O/Px mx
scales the max. output i.e. 20mA. or 24mA.
Where x is the output numbered 1 to 4
The above scaling factors are entered in the same units as the output parameter for example, if the output has been selected
to be Pressure then O/Px mn and O/Px mx are entered in the units of Pressure. The values entered for O/Px mn and O/Px
mx must be within the operating range of the parameter selected i.e. for Pressure between pmin and pmax. and the value
entered for O/Px mn should be above or equal to pmin. and lower in value than pmax. Similarly O/Px mx should be above
pmin. and O/Px mn and lower than or equal to pmax.
2.5.2.
PID CONTROL ANALOGUE OUTPUT SIGNALS
This function can be used to control process variables like flow rate, temperature, pressure etc. Most PID functions use the
difference between SP (Set point) and PV (Process Value) as input for its calculation. The output value is the sum of a
Proportional, Integral and Derivative action. It has a forward / reverse parameter to use the controller in the right direction.
The output value will be the override value in manual mode. Manual (Override) / Automatic switch over will be carried out
bumplessly. For each output the following parameters must be set up Time Delay in seconds, SP Preset (Set point) value,
Integral Time, Proportional Band and Derivative Time.
Calculations linking these parameters are as follows:-
P
P
gain
band
=
100
Summary of Contents for 2000
Page 3: ...Model 2000 issue 21 Page No 3 ...
Page 107: ......
Page 108: ......
Page 109: ......
Page 110: ......
Page 111: ......
Page 112: ......
Page 113: ......
Page 114: ......
Page 115: ......
Page 116: ......
Page 117: ......
Page 118: ......
Page 119: ......
Page 120: ......
Page 121: ......
Page 122: ......
Page 123: ......
Page 124: ......
Page 125: ......
Page 126: ......
Page 127: ......
Page 128: ......
Page 129: ......
Page 130: ......
Page 131: ......
Page 132: ......
Page 133: ......
Page 134: ......
Page 135: ......
Page 136: ......