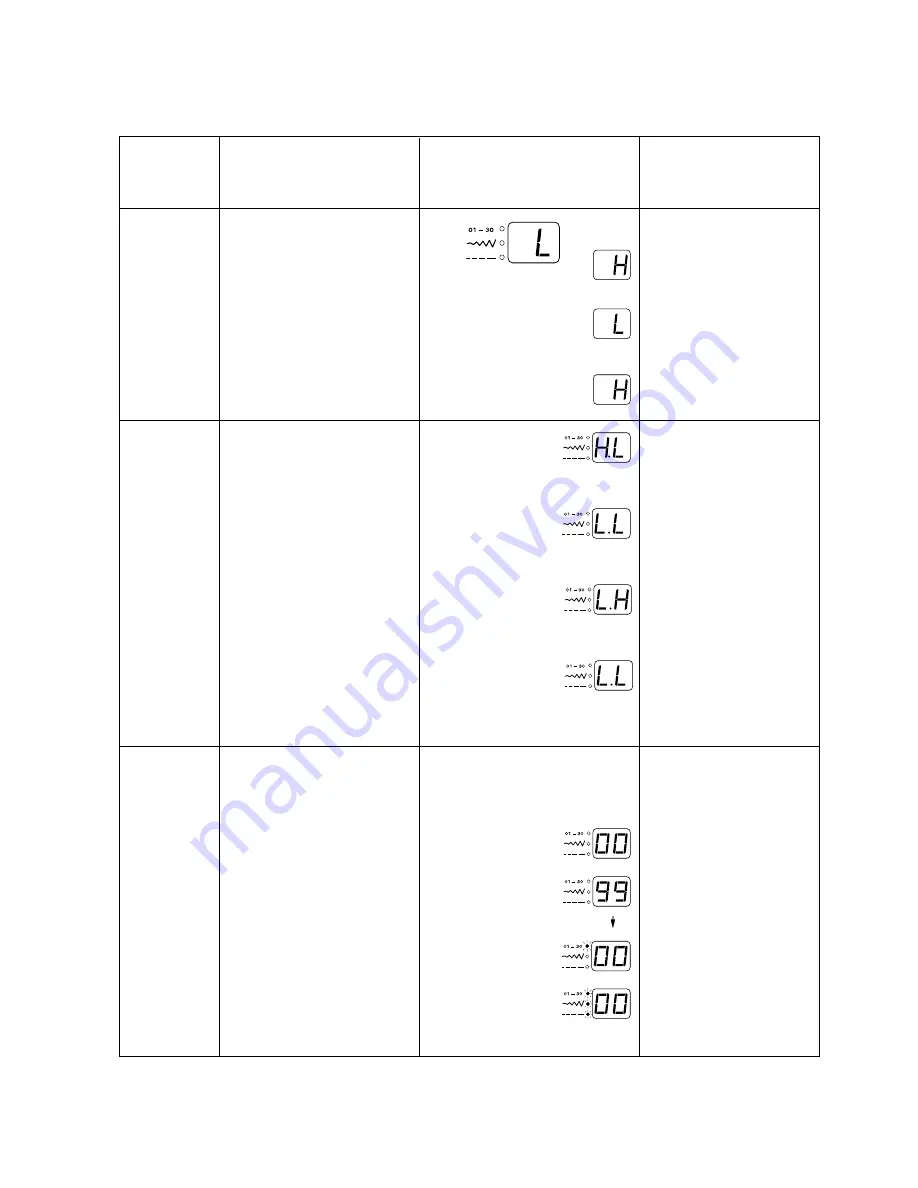
23
MODEL 520
CORRECT CONDITION
* When the buttonhole lever
is pulled, led displays "H".
* When the buttonhole lever
is free (positioned in the
center), led displays "L".
* When the buttonhole
lever is pushed, led
displays "H".
* When the needle is
at the highest position,
led displays "LH".
* When the needle is
at the lowest position,
led displays "LH".
* When the needle is
halfway, led
displays "LL".
* Led displays "00" first and the
indicates value increases as you
turn the handwheel.
(When the value
reaches 100, it will
return to "00" and one
mode led lights up.
For example, 2 mode
leds and "78" means
"278".)
The maximum value
should be 370 to 390.
STEP
06)
Buttonhole
sensor
07)
Upper shaft
sensor
08)
Sewing
speed
sensor
OPERATION
Press #01 button, led displays
"06" for one second.
1. Lower the buttonhole lever.
2. Move the buttonhole lever back
and forth.
Press the #01 button,
led displays "07" for one second.
* Turn the handwheel toward you
to
raise and lower the needle to its
highest and lowest position.
* Press the #01 button.
Led displays "08" for one
second.
* Turn the handwheel clockwise
by hand and check the counter
value displayed
by the leds.
DEFECTIVE CONDITION
Led display is different from
that shown to the left.
1. Adjust the buttonhole
sensor position.
2. Replace buttonhole
sensor.
3. Replace board "A".
* Led display is different from
that shown to the left.
1. Adjust upper shaft shield
plate.
2. Replace upper shaft sensor.
3. Replace board "A".
* Led displays different from
that shown to the left.
1. Replace motor.
2. Replace board "A".