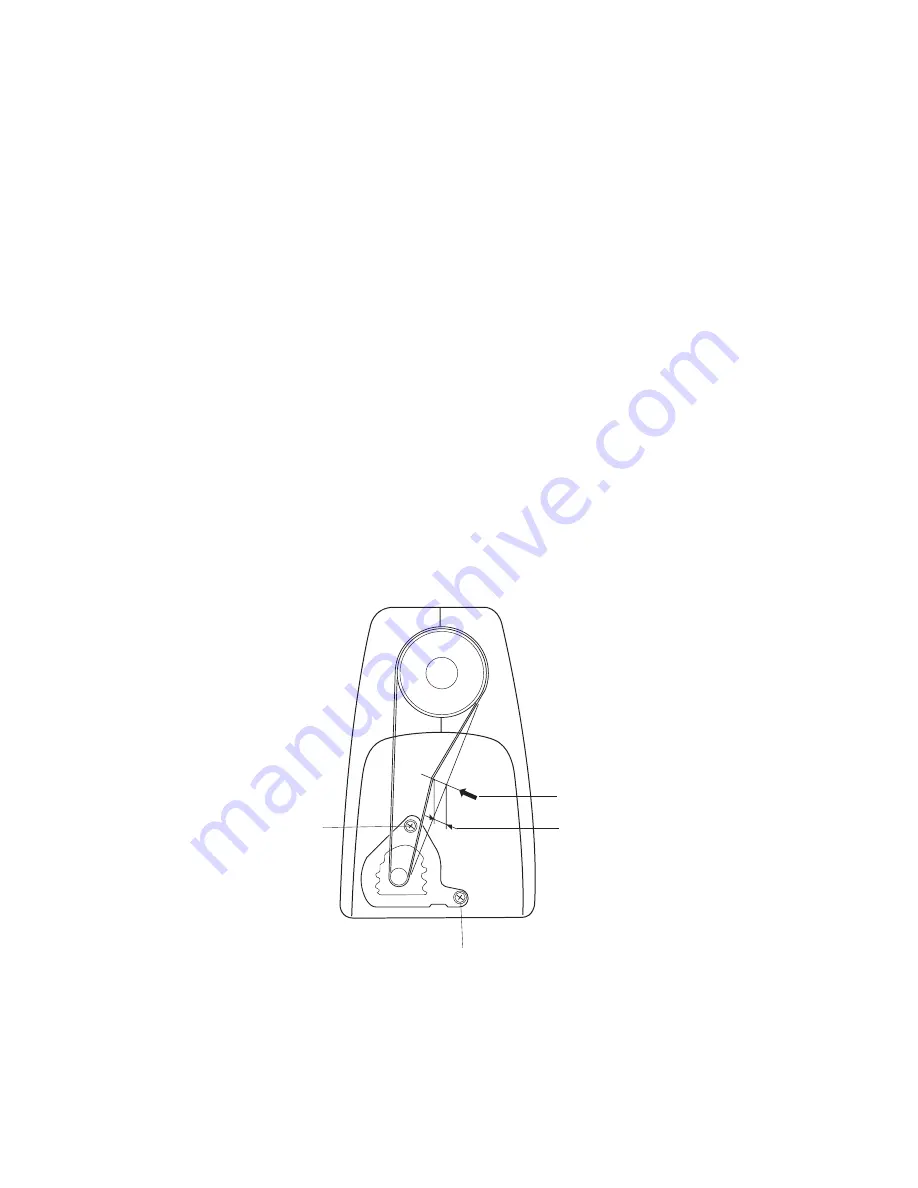
22
MECHANICAL ADJUSTMENT
MOTOR BELT TENSION
To check:
1. Improper belt tension may cause noise, overload of motor, slow running or motor belt jumping.
2. The belt deflection should be 7mm - 9mm when pressing the middle of the motor belt with
approximately 300 grams of pressure.
Adjustment procedure:
1. Remove the belt cover (See page 4).
2. Loosen the setscrews (A) and (B).
3. Move the motor up or down to adjust the deflection about 7mm - 9mm.
4. Tighten the setscrews (A) and (B).
5. Attach the belt cover.
300g Load
Deflection 7-9mm
Setscrew (B)
Setscrew (A)