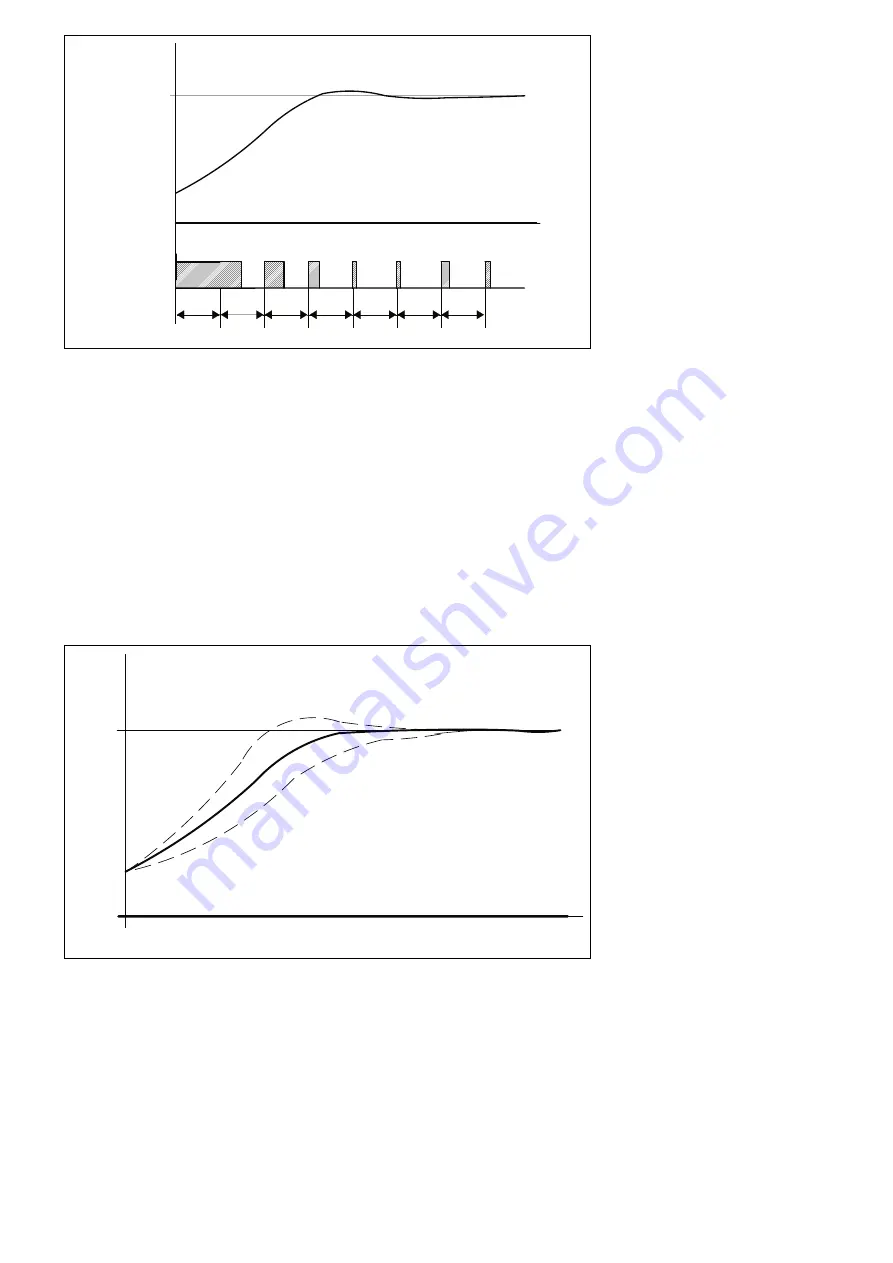
The Single Action PID control algorithm fore-
sees the setting of the following parameters :
"Pb" – Proportional Band
"tcr1" – Cycle time of the output 1rEG
"Int" – Integral Time
"rS" – Manual Reset (if “Int =0 only)
"dEr" – Derivative Time
“FuOC” - Fuzzy Overshoot Control
This last parameter allows the variable over-
shoots at the start up of the process or at the
changing of the Set Point to be avoided.
Please remember that a low value on this para-
meter reduces the overshoot while a high value
increase it.
1: Value “FuOC” OK
2: Value “FuOC” too high
3: Value “FuOC” too low
DOUBLE ACTION PID CONTROL (1REG -
2REG)
All the parameters referring to PID control are
contained in the group “]rEG”.
The Double Action PID control is used to con-
trol plants where there is an element which
causes a positive increase (ex. Heating) and an
element which causes a negative increase (ex.
Cooling).
This type of control can be obtained when 2
outputs are programmed respectively as 1rEG
and 2rEG and the par. “Cont” = Pid.
The element causing a positive increase has to
be connected to the output programmed as
1rEG while the element causing a negative
increase has to be connected to the output pro-
grammed as 2rEG.
The Double Action PID control works on the
outputs 1rEG and 2rEG depending on the active
Set Point “SP” and on the instrument’s PID algo-
rithm with two degrees of freedom.
In order to obtain good stability of the process
variable, in case of fast processes, the cycle
times “tcr1” and “tcr2” have to have a low value
with a very frequent intervention of the control
outputs.
In this case use of solid state relays (SSR) to
drive the actuators is recommended.
The Double Action PID control algorithm needs
the programming of the following parameters :
• "Pb" – Proportional Band
• "tcr1" – Cycle time of the output 1rEG
• “tcr 2” – Cycle time of the output 2rEG
• "Int" – Integral Time
• "rS" – Manual Reset (if “Int =0 only)
• "dEr" – Derivative Time
• “FuOC” - Fuzzy Overshoot Control
• "Prat" - Power Ratio or relation between
power of the element controlled by output
2rEG and power of the element controlled by
output 1rEG.
AUTOTUNING AND SELFTUNING FUNCTIONS
All the parameters referring to the AUTO-TUN-
ING and SELF-TUNING functions are contained
in the group “]rEG”.
The AUTO-TUNING and SELF-TUNING functions
permit the automatic tuning of the PID con-
troller.
The AUTO-TUNING function permits the calcula-
tion of thePID parameters by means of a FAST
type tuning cycle and, at the end of this opera-
tion, the parameters are stored into the instru-
ment’s memory and remain constant during
control.
The SELF-TUNING function (rule based "TUNE-
IN") instead allows control monitoring and the
continuous calculation of the parameters during
control.
Both functions automatically calculate the fol-
lowing parameters :
"Pb" – Proportional Band
"tcr1" – Cycle time of the output 1rEG
"Int" – Integral Time
"dEr" – Derivative Time
“FuOC” - Fuzzy Overshoot Control
and, for the Double Action PID control, also :
“tcr 2” – Cycle time of the output 2rEG
"Prat" - Ratio P 2rEG/ P 1rEG
To activate the AUTO-TUNING function proceed
as follows :
1) Program and activate the desired Set Point.
2) Program par. "Cont" =Pid.
3) Program par. "Func" according to the process
to be controlled through output 1rEG.
4) Program an output as 2rEG if the instrument
controls a plant with double action
5) Program par. "Auto" as:
- "1” – if auto-tuning is desired automatically,
each time the instrument is switched on, on the
condition that the process value is lower (with
“Func” =HEAt) than [SP- |SP/2|] or higher (with
“Func” =CooL) than [SP+ |SP/2|].
- "2" – if auto-tuning is desired automatically,
the next time the instrument is switched on, on
the condition that the process value is lower
(with “Func” =HEAt) than [SP- |SP/2|] or higher
(with “Func” =CooL) than [SP+ |SP/2|], and
once the tuning is finished, the par. “Auto” is
automatically swapped to the OFF state
- "3" - if manual auto-tuning is desired, by
selecting par. “tunE” in the main menu or by
correctly programming key F as “USrb” = tunE.
In this case the auto-tuning starts without any
control on the process value condition. It is rec-
ommended to use this option, starting the auto-
tuning when the process value is as far as possi-
ble from the Set Point because, in order to fea-
ture the Auto-tuning FAST with its best perfor-
mances , it is preferable to respect this condi-
tion.
- "4" - if it’s desired to activate the autotuning
automatically at the end of programmed Soft-
Start cycle. The Autotuning will start at the con-
dition that the process value is lower (with
“Func” =HEAt) than [SP- |SP/2|] or higher (with
“Func” =CooL) than [SP+ |SP/2|].
6) Exit from the parameter programming.
7) Connect the instrument to the controlled
plant.
8) Activate the Auto-tuning by selecting par.
“tunE” in the main menu (or by correctly pro-
gramming key F ).
At this point the Auto-tuning function is activat-
ed and is indicated by the flashing led AT/ST.
The regulator carries out several operations on
the connected plant in order to calculate the
most suitable PID parameters.
If “Auto” = 1 or “Auto” = 2, and if, at the Auto-
tuning start, the condition for the lower process
value is not found (with “Func” =HEAt) than
[SP- |SP/2|] or higher (with “Func” =CooL) than
[SP+ |SP/2|], the display will show “ErAt” and
the instrument will be swapped to normal con-
trol conditions according to the previously pro-
grammed parameters.
The Auto-tuning cycle duration has been limited
to 12 hours maximum.
If Auto-tuning is not completed within 12 hours,
the instrument will show "noAt" on the display.
In case of probe error, the instrument automati-
EWTQ 905
4/8
0N
tcr1
1.rEG
(HEat)
SP1
PV
tcr1
off
tcr1
tcr1
tcr1
tcr1
0N
off
off
0N
off
off
0N
0N
tcr1
off
0N
0N
time
OUT
2
1
3
SP1
PV
time