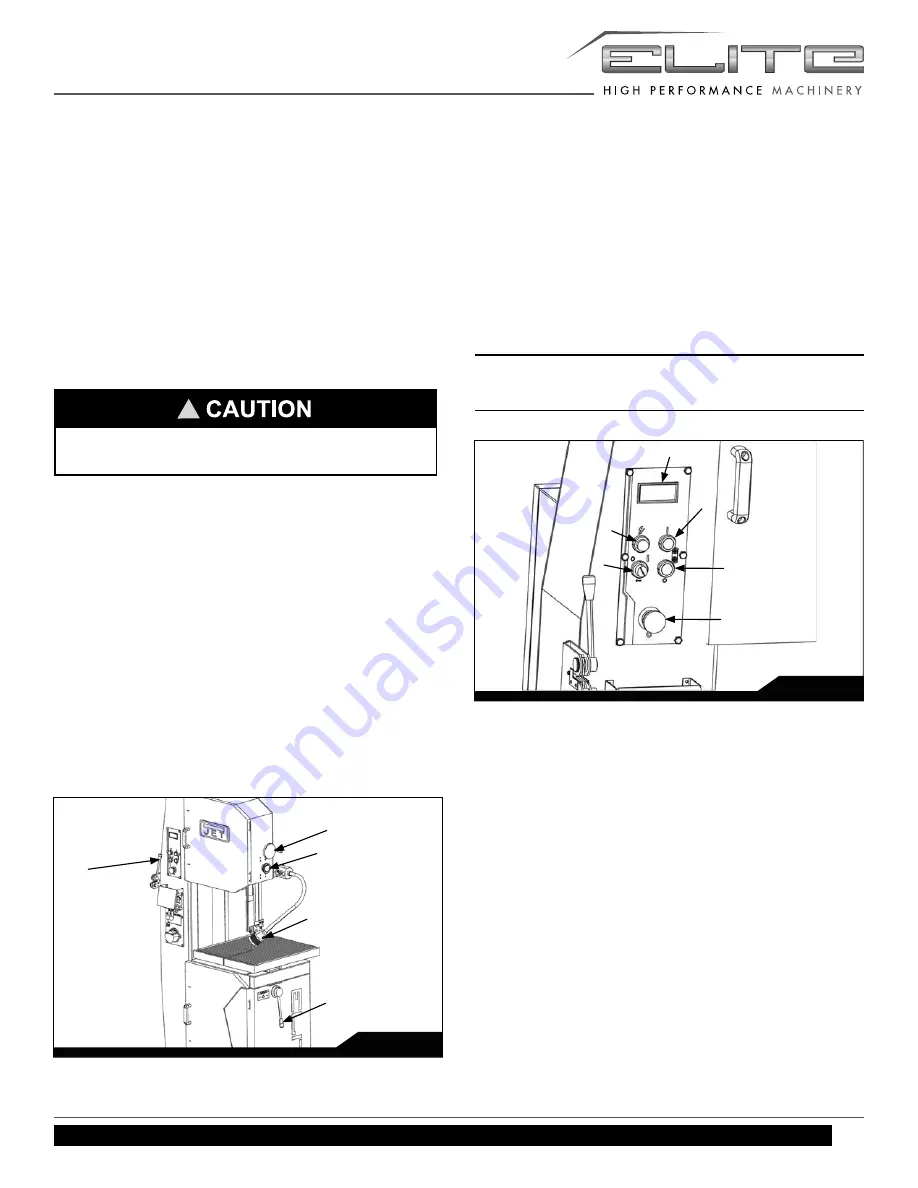
9
EVBS-26
machine from power, and switch any two of the three
leads in the motor junction box (see section 19.0,
Wiring
Diagram
).
9.0 CONTROLS
Refer to Figures 2 and 3.
Low/High Range Shift Lever (B, Figure 2) -
Pull toward the front of the machine to shift into the low
speed range. Push toward the rear of the machine to shift
into the high speed range.
Upper Blade Guide Lock Knob (D, Figure 2) -
Turn counterclockwise to loosen and clockwise to tighten.
Upper Blade Guide Knob (E, Figure 2) -
Turn clockwise to raise blade guide assembly; counter-
clockwise to lower.
Work Lamp Switch (F, Figure 2) -
Located on top of lamp shade; turns lamp on and off.
Shear Lever (G, Figure 2) -
UP position allows insertion of blade end into shear. Pull
lever DOWN to cut blade.
Main Motor Start Switch (H, Figure 3) -
Press to start band saw.
Main Motor Stop Switch (I, Figure 3) -
Press to stop band saw.
!
Do not turn knob while machine is stopped. Adjust
speed only when machine is running.
Grinder Toggle Switch (N, Figure 4) -
Located on blade welder panel. Flip switch up to start
grinder; fl ip down to stop grinder.
Weld Button (O, Figure 4) -
Located on blade welder panel. Press and hold to start
welding. Shuts off automatically when weld is done. Re-
lease when weld is completed.
Anneal Button (P, Figure 4) -
Located on blade welder panel. Press and hold to anneal
blade, release to stop.
Blade Clamp Pressure Knob (Q, Figure 4) -
Located on blade welder panel. Sets pressure for different
width blades.
Blade Clamps (R, Figure 4) -
Located on blade welder panel. DOWN position allows
insertion of blade into clamp. Up position locks blade.
Key Lock Switch (J, Figure 3) -
Turn to 12 o’clock position and remove key to lock out
power from the control panel. Insert key and turn to 3
o’clock position to turn on power to control panel.
Emergency Stop Switch (K, Figure 3) -
Press to stop all machine functions. Turn 90° to reset.
Power Lamp (L, Figure 3) -
Illuminated when power is being supplied to band saw.
Digital Readout (M, Figure 3) -
Indicates blade speed in feet per minute.
Note: After saw is fi rst started or the speed has been
changed, allow at least a minute for the readout to
stabilize the new setting.
Fig. 3
H
I
K
L
J
M
Fig. 2
B
E
D
G
F
Summary of Contents for EVBS-26
Page 25: ...25 EVBS 26 BREAKDOWN ASSEMBLY EVBS 26...
Page 36: ...36 Vertical Band Saw NOTES...