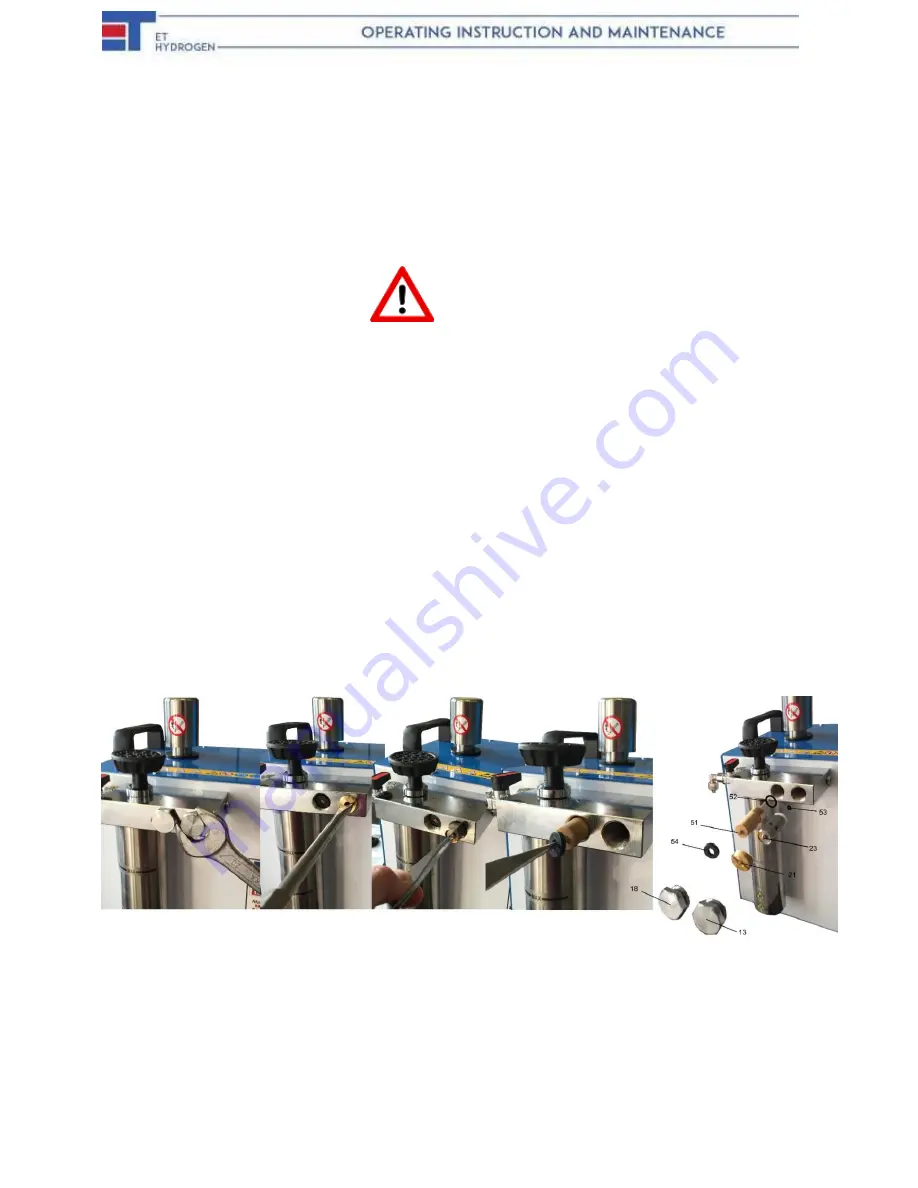
27
5.10.3 CHECKING VALVE TIGHTNESS
When the welder is on, the working pressure must be approximately, (1.0- 1.2 Bar). Then, after turning
off the welder, check that the pressure reading on the pressure gauge drops to the approx. 0.5 Bar,
over 5-6 minutes. If the pressure drop is greater than 0.5 Bar, replace the valve (see. 5.10.4).
ATTENTION
If is very important that the valve is tight, since this enables the machine to maintain a
minimum pressure of approx. 0.3 Bar inside the tank, even after several hours. Keep in mind
that when the machine is not working, the tank cools down causing a pressure drop. If for
some reason there is a total lack of pressure, the methyl alcohol contained in the Booster
Tank would be sucked in, thus contaminating the electrolyte.
5.10.4 REPLACING THE VALVE
1) Turn off the welder and remove the pressure
gauge or safety cap (Fig.5 # 2).
2) Unscrew the check valve cap (A Fig. 4 # 13)
3) Unscrew the threaded disk (B Fig. 4).
4)
Remove the valve and relevant “OR” from the seat (C Fig. 4).
5)
Install the new valve and relevant “OR” (C Fig. 4) 23.
6) Tighten the threaded disk 21, the cap 13, and safety cap.
7) Check pressure (sec. 5.10.3).
FIG 4
– CHECK VALVE AND BACK FLAME FILTER REPLACEMENT