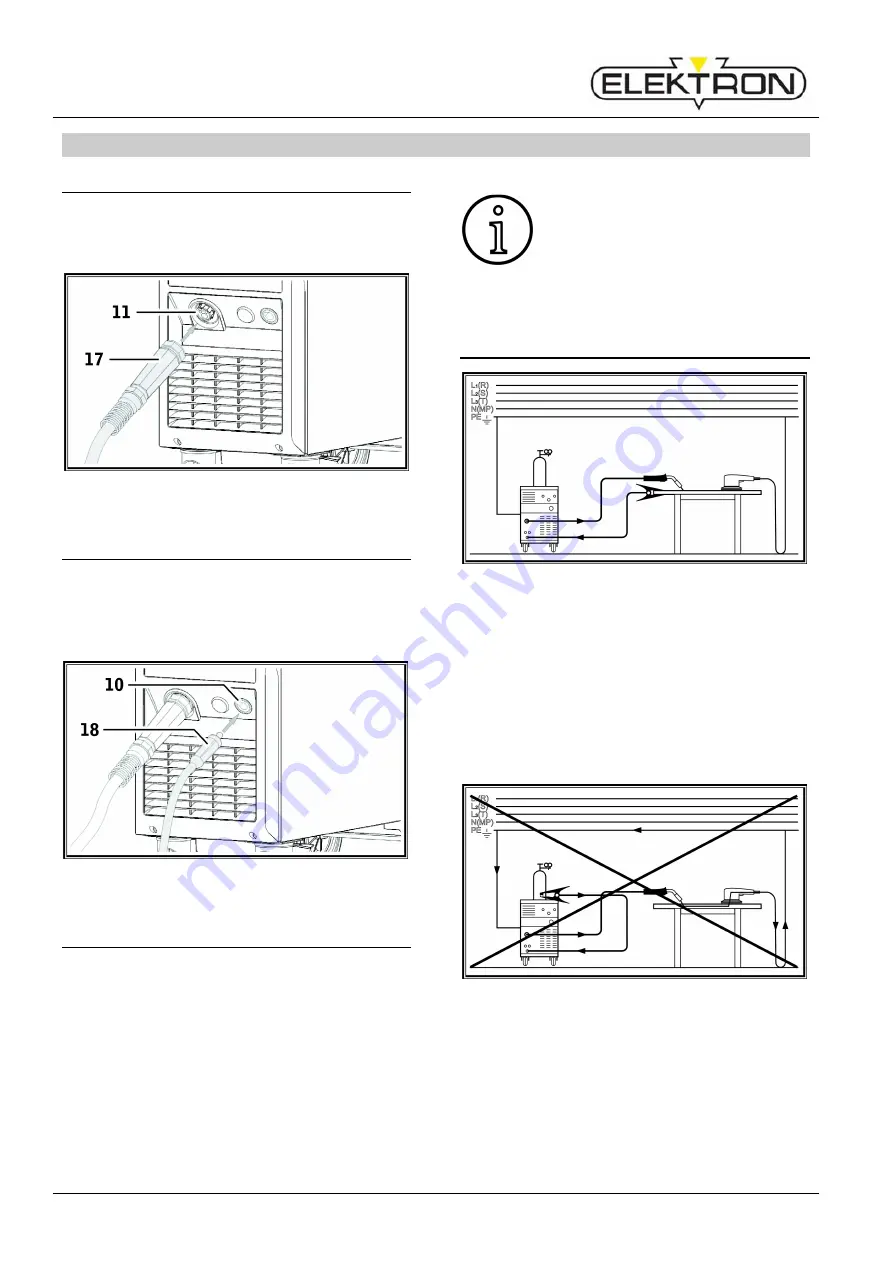
KERCOMET 170
and
210, MULTIMIG 150
Before start-up
10
12 Before start-up
12.1 Connecting the torch
Connect the central connector 17 of the
torch to the central socket 11.
Fig. 3:
Connecting the torch
12.2 Connecting the ground cable
Connect welding return cable 18 to con-
nector 10 and secure it by turning it clock-
wise.
Fig. 4:
Connecting the ground cable
12.3 Select mains voltage
(Only for machines with mains voltage switch-
over, refer to technical data)
Set the required voltage by using mains
voltage switch 4.
For 230 V operation, the adapter CEE 16 on
shock proof plug (incl. in delivery) may be
used.
Performance values are limited in
230 V mode, i.e. max welding
power is limited to 2/3 of the values
stated in technical data.
12.4 Fastening the ground clamp
Fig. 5:
Correct
Attach the ground clamp immediately be-
side the welding point so that the welding
current will not try to find its own return path
through machine parts, ball bearings or
electric circuits.
Connect the ground clamp firmly to the
welding bench or the work piece.
Fig. 6:
Incorrect
Do not place the ground clamp on the
welding machine or the gas cylinder; oth-
erwise the welding current will be carried via
the protective conductors and it will destroy
these.