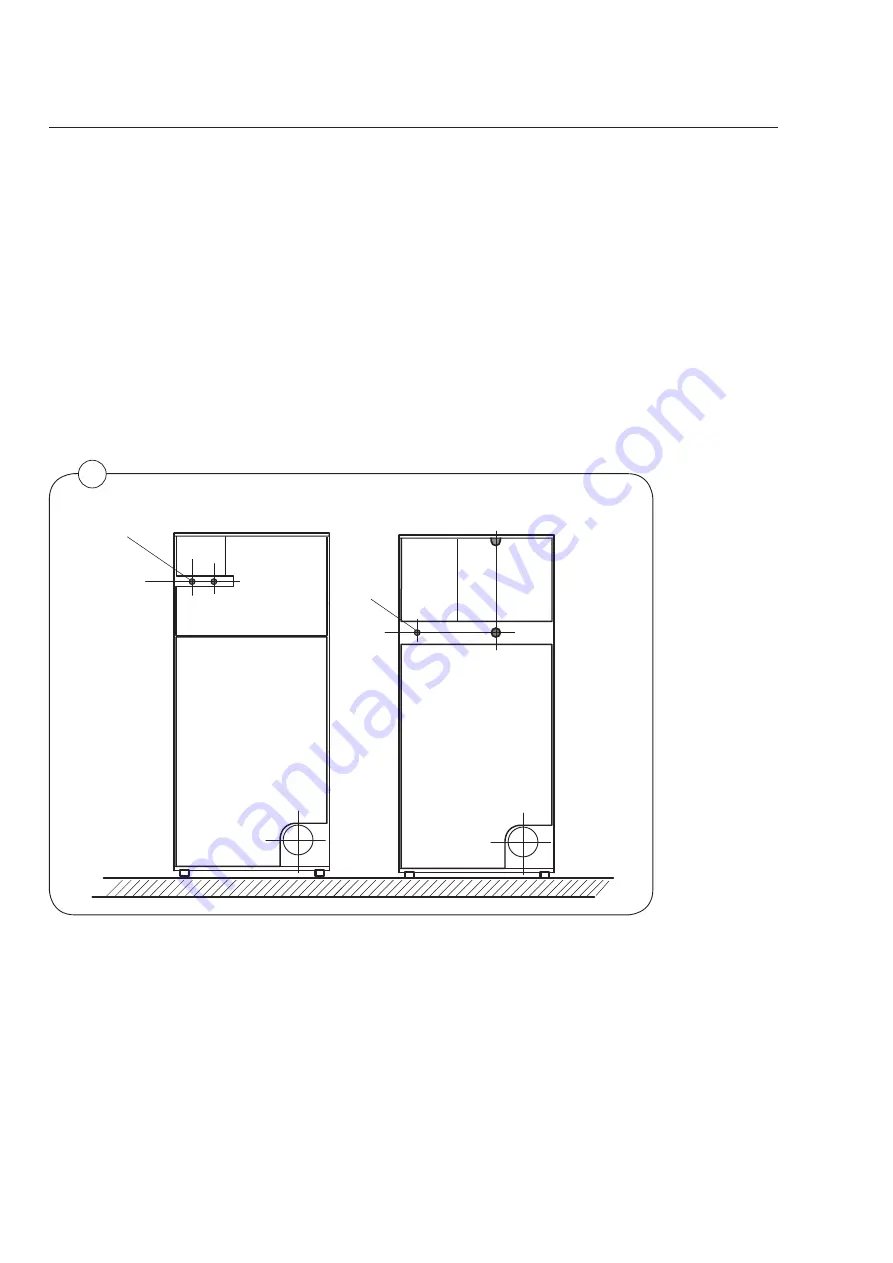
Installation
2
Electric installation
Connecting the cable (outside the EU and EEA)
1. Demount cover plate
A
, fig. 1.
2. Pass the feeder cable through cable gland
**,
fig. 1.
. Connect the feeder cable as illustrated.
4. Remount cover plate
A
.
. Function check the dryer.
The function check is described in the back of this manual.
A
A
1
Cable gland for feeder cable
Fig 1 Positioning of cable gland for feeder cable.
On electric heated dryers type T40 and T460 the cable gland is not
mounted. The cable gland is in the drum and has to be mounted on the
beam.