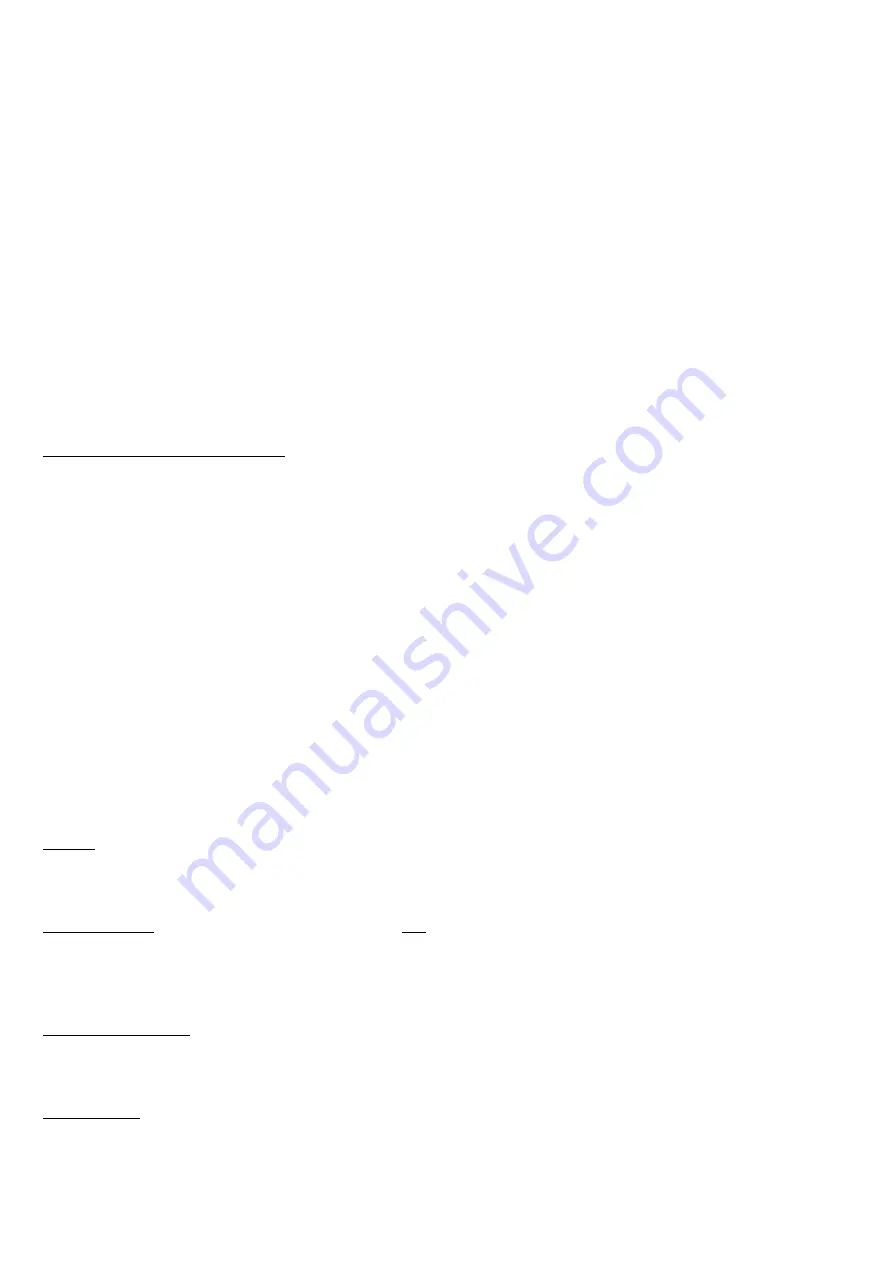
Page 6 RESI219
•
If the freezer fan and compressor are off, the temperature of the food compartment must rise another
2ºC before the freezer fan motor is activated. The compressor will not switch on until the freezer
sensor reaches its set point.
For each half hour of a 24 hour period, the amount of time the door is open for the half hour is recorded.
This is compared with three previous values and the three maximums out of the four values are kept. This
procedure is repeated for the 24 hour period until the three daily maximums have been recorded
(Basically trying to match breakfast, lunch and tea).
The next day each half hour maxima is preceded by an extra cooling period that tries to reduce the freezer
compartment air temperature to 3°C below the set point. A 30 minute time limit applies. This provides
extra capacity for the expected door opening period.
The same three maximums are also used to try and prevent defrosts from occurring during those times of
maximum door opening, provided a minimum run time is met. After each defrost the compressor run time
for the next period is set to one of seven values between 6 and 22 hours based on
the heater on time of that defrost. If during the next period there are door openings the run time is reduced
in six stages to compensate for the extra moisture load.
ADDITIONAL INFORMATION
When the cabinet is first switched on (or after a power failure) the refrigerator goes into a 27 minute self
diagnostics. During this period the baffle is closed for the first 10 minutes and the compressor and freezer
fan run continuosly for apprximately 21 minutes. This is followed by a 2 minute defrost. The refrigerator
then switches off for 4 minutes before switching into normal mode conditions.. (If during this 27 minute
period the food compartment door is opened or a button is pressed on the User Interface (Control Display)
the self diagnostics will be cancelled). Initiating a manual diagnostics will overide the self diagnostics.
If there is a power failure or the refrigerator is switched off the Control Board holds in its memory the
control settings (temperatures) and the time of day the refrigerator was switched off. When power is
returned to the refrigerator the Control Board memory (temperatures & time) will be re communicated
back to the User Interface (Control Display). The compressor should then run continuously until the set
air temperature of the freezer compartment sensor is reached and the baffle will remain open until the set
air temperature of the fresh food compartment sensor is reached. The compartments will then cycle about
the set air temperatures. When 3 hour 10 minutes has elapsed a defrost will occur (required because the
electronics retains no memory during a power failure, this stops the possibility of extended run time
between defrosts causing excessive ice build-up), the compressor run time to the next defrost is now set
and the cabinet is now in its normal operational state.
Clock: If there is a power failure or the refrigerator is switched off the Control Board holds in its memory
the time of day the refrigerator was switched off. When the refrigerator is switched back on the customer
will have to reset the clock to the present time if the power was off for more than a minute.
Defrost Timing: The 6 to 22 hours of compressor run time is followed by the lesser of a 35 minute
defrost period, or heater on time plus 4 minute drip time. The heater on time is determined by the defrost
termination thermostat (DTT). The defrost heater on time is sensed through a separate wire connected
between the defrost heater and the DTT.
System Equalisation: The compressor off cycle will never be less than 6 minutes duration even if the
freezer sensor is warmed up manually or the wiring short circuited. This allows the system pressures to
equalise so the compressor starts under no load.
Failure Mode: If one of the sensors goes open or short circuit the compressor, freezer fan and baffle will
run a 50% on and off cycle.
Summary of Contents for B Series
Page 4: ...Page 4 RESI219 ...
Page 8: ...Page 8 RESI219 ...
Page 9: ...Page 9 RESI219 ...
Page 10: ...Page 10 RESI219 ...
Page 11: ...Page 11 RESI219 ...
Page 12: ...Page 12 RESI219 ...
Page 13: ...Page 13 RESI219 ...
Page 14: ...Page 14 RESI219 ...
Page 15: ...Page 15 RESI219 ...
Page 16: ...Page 16 RESI219 ...
Page 17: ...Page 17 RESI219 ...
Page 18: ...Page 18 RESI219 ...
Page 19: ...Page 19 RESI219 ...
Page 20: ...Page 20 RESI219 ...
Page 27: ...Page 27 RESI219 OPERATING CYCLE ILLUSTRATIONS MECHANICAL ...
Page 28: ...Page 28 RESI219 ...
Page 29: ...Page 29 RESI219 OPERATING CYCLE ILLUSTRATIONS ELECTRICAL ...
Page 30: ...Page 30 RESI219 ...
Page 31: ...Page 31 RESI219 ...
Page 37: ...Page 37 RESI219 ...
Page 38: ...Page 38 RESI219 DOOR GASKET REMOVAL ...
Page 39: ...Page 39 RESI219 DOOR GASKET REMOVAL ...
Page 40: ...Page 40 RESI219 ...
Page 41: ...Page 41 RESI219 Gasket Profiles DOOR GASKET REPLACEMENT ...
Page 42: ...Page 42 RESI219 ...
Page 43: ...Page 43 RESI219 ...
Page 44: ...Page 44 RESI219 ...
Page 46: ...Page 46 RESI219 REMOVAL OF THE FREEZER FAN D T T HEATER HARNESS CONNECTIONS ...
Page 48: ...Page 48 RESI219 ...
Page 49: ...Page 49 RESI219 ...
Page 50: ...Page 50 RESI219 ...
Page 51: ...Page 51 RESI219 ...
Page 52: ...Page 52 RESI219 REMOVAL OF THE FREEZER LIGHT GLOBES ...
Page 53: ...Page 53 RESI219 ACCESS TO THE CONTROL BOARD COMPRESSOR CONDENSER FAN CONDENSER WATER VALVES ...
Page 55: ...Page 55 RESI219 MODELS WSE6070PB 06 AIR FLOW R757 WSE6070SB 06 WSE6070WB 06 ...
Page 56: ...Page 56 RESI219 MODELS WSE6070PB 06 AIR FLOW R1051 WSE6070SB 06 WSE6070WB 06 ...