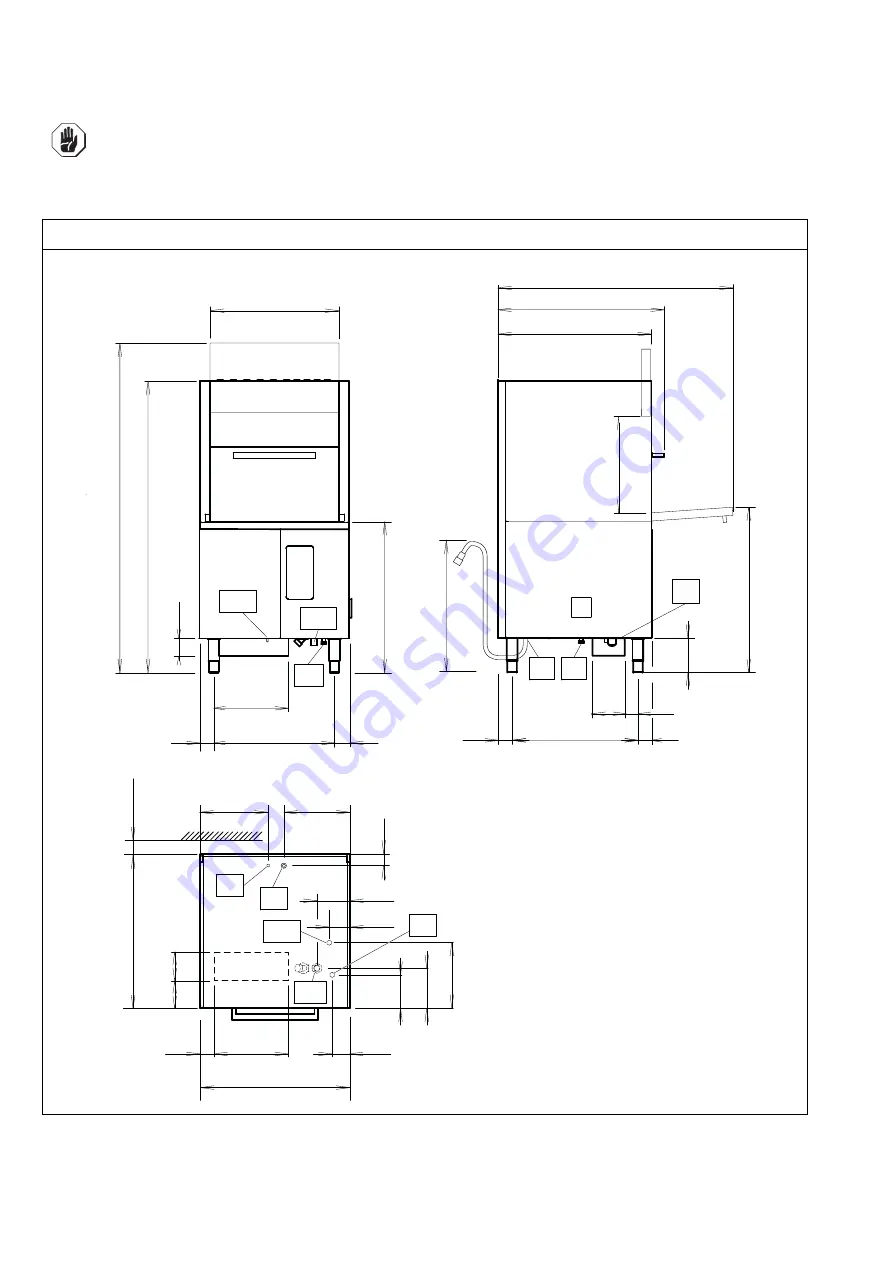
16
F6.2
Installation diagrams
The following installation diagrams give the appliance overall dimensions and position of water and electrical con-
nections.
IMPORTANT!
Make sure to install an extractor hood to remove the steam produced by the appliance.
The hood air flow must be calculated taking into account the type of installation and the work
environment where it is installed. In any case, an air flow rate of between 1000 m
3
/h and 1500 m
3
/
h is recommended.
Installation diagram for EPPWES (electric versions)
83
738
79
87
702
414
220
986
900
1374
570
972
105
904
M
ax 800
1791
2020
87
145
220
900
876
284
194
385
151
200
55
440
190
M
in 100
780
430
380
70
EI
EI
D
EI
EQ
XD
D
HWI
HWI
EQ
XD
59
220
LEGEND
HWI
Hot water inlet
D
Drain outlet
EI
Power supply entry
EQ
Equipotential screw
XD
Pipe inlet for detergent