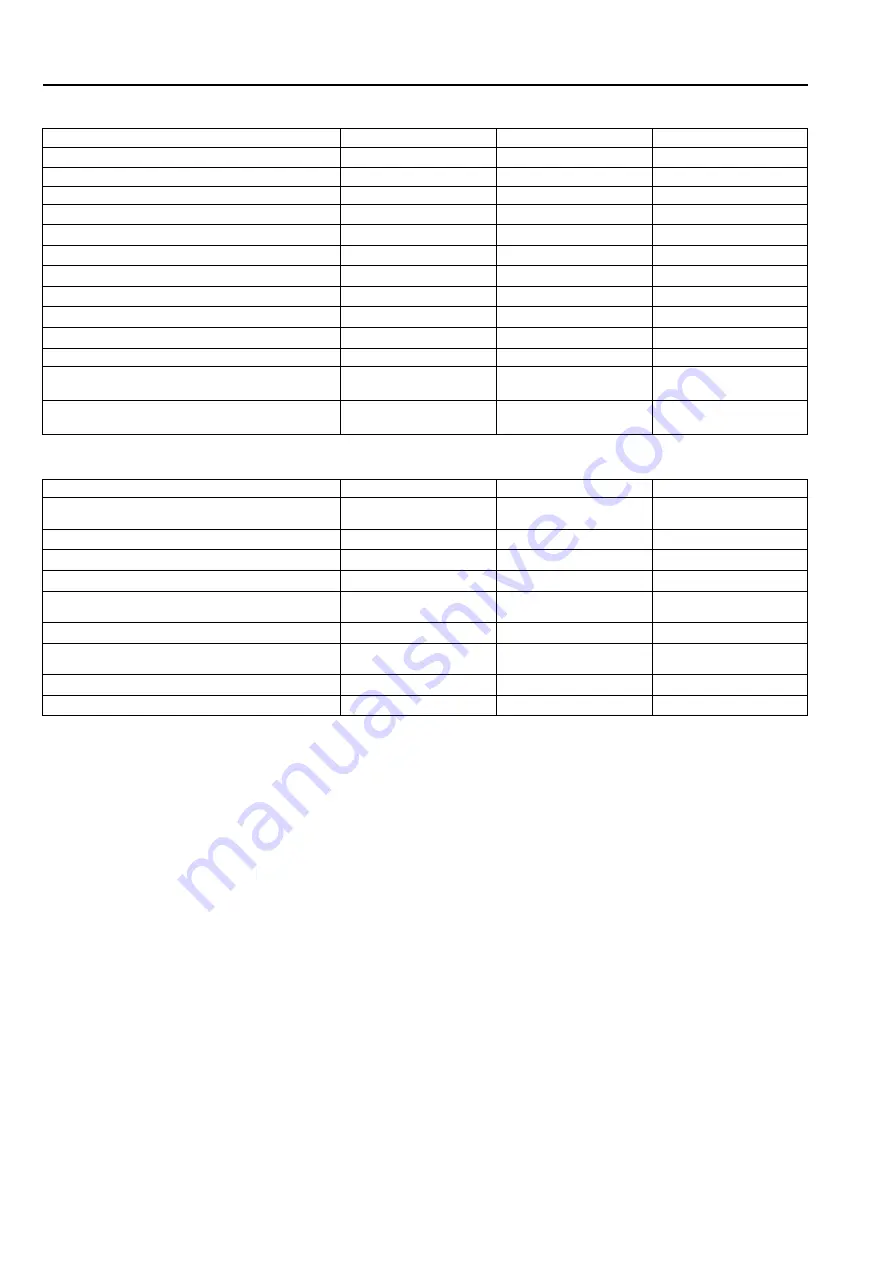
10
Installation manual
3.2
Technical data
WB5130H
WB5180H
Weight, net
kg
296
356
Drum volume
litres
130
180
Drum diameter
mm
650
725
Drum speed during wash
rpm
49
44
Drum speed during extraction
rpm
910
860
G-factor, max.
300
300
Heating: Electricity
kW
13
18
Heating: Steam
x
x
Heating: Hot water
x
x
Frequency of the dynamic force
Hz
15.2
14.3
Floor load at max extraction
kN
3.4±0.5
2.9±1.0
A-weighted emission sound pressure level at working
stations (Wash)
dB(A)
<70
<70
A-weighted emission sound pressure level at working
stations (Extraction)
dB(A)
79
85
3.3
Connections
WB5130H
WB5180H
Water valves
DN
BSP
20
3/4”
20
3/4”
Recommended water pressure
kPa
200–600
200–600
Continuous operating pressure
kPa
50–800
50–800
Capacity at 300 kPa
l/min
20
60
Drain valve
⌀
outer
mm
75
75
Draining capacity
l/min
170
170
Steam valve connection
DN
BSP
15
1/2”
15
1/2”
Recommended steam pressure
kPa
300–600
300–600
Functioning limits for steam valve
kPa
50–800
50–800
Summary of Contents for WB5130H
Page 2: ......
Page 4: ......
Page 32: ...Electrolux Professional AB 341 80 Ljungby Sweden www electroluxprofessional com ...