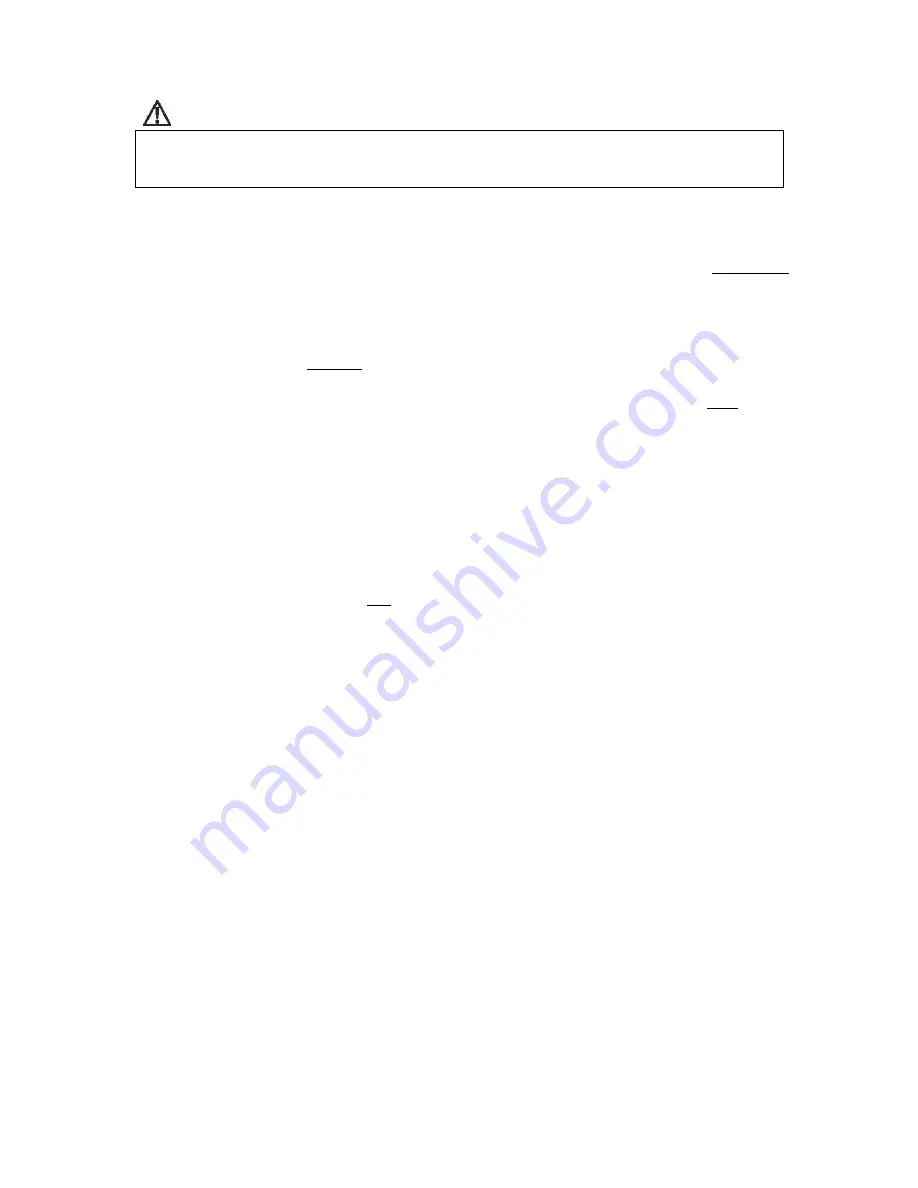
03/12/2019
4
BI309
MECHANICAL INSTALLATION
CAUTION
Electro Industries Inc. requires the use of dielectric isolation between the boiler vessel supply
and return piping when the boiler is plumbed using copper or any other dissimilar metal.
Damage to the vessel caused by galvanic corrosion voids Electro Industries’ warranty.
Reference drawing BX305
The plumbing components and piping layout shown on drawing BX305 has been very carefully picked and
should be plumbed as shown. When following this diagram, the water fill procedure becomes very simple and
almost guarantees the removal of all air or prevents air locking problems. Experienced hydronic heating
installers may be able to eliminate components such as regulated fill valve, check valve, temperature gauge, etc.,
but the inclusion of these components guarantees installation and initial operating success.
The key mechanical components required include:
Boiler/Plumbing Kit Placement
– This model series is wall hung and the vessel must be vertical.
The plumbing kit items are located adjacent to the boiler housing itself as shown on
drawing BX305.
For future servicing, the unit itself must be installed a minimum of 18” above the floor. The
elements are screwed in from the bottom.
Allow adequate space for cover removal and maintenance.
Expansion Tank
- As a closed loop hydronic heating system, a minimal expansion tank is required.
This can be an air diaphragm tank as provided in the plumbing kit or a basic “empty” tank where air
is compressed at the tank top.
Temperature/Pressure Gauge
- Recommended to observe the operation of the system. Actually a
temperature gauge at the inlet and outlet is desirable.
Pressure Safety Valve
- This is required at the hot outlet and is furnished as a
loose
component
with the boiler unit itself. Failure to install the provided, 30 PSI, pressure relief valve as shown
voids warranty and product listing.
Add the necessary pipe extension from the relief valve to the floor to prevent water damage on this unit
or surrounding area.
Gate Valve/Drain Valve
- These are for servicing and easy fill purposes.
Circulating Pump
- Depending upon system lift and system loop resistance (feet of head), the
proper circulating pump is required to guarantee the minimum GPM flow as specified on the cover
sheet.
Comment
: Circulator pump can be in the outlet or inlet. However, the circulator pump should “pump
away from” the expansion tank.
Air Vent
– Whenever there is a plumbing point higher than any of the components shown or an
adjacent line (any vertical “U” trap), an air vent valve should be provided.
Building Water Supply Connection
– Reference drawing BX305, note 4, some local building
codes require sophisticated check valve or anti-siphon check valve when the hydronic heating
system is permanently connected to the domestic water system. The intent of this connection is
temporary and for fill purposes only. The installer has the responsibility of complying with local
building codes.
Summary of Contents for Mini-Boiler EMB-S-1
Page 12: ...EMB S H 12 04 18 1 of 2 BX305 ...
Page 13: ...EMB S H 12 04 18 2 of 2 BX305 ...
Page 14: ...EMB S EMB H 03 19 19 1 of 2 BH310 G ...
Page 15: ...EMB S EMB H 03 19 19 2 of 2 BH310 G ...
Page 16: ...DECAL TITLEBLOCK ...