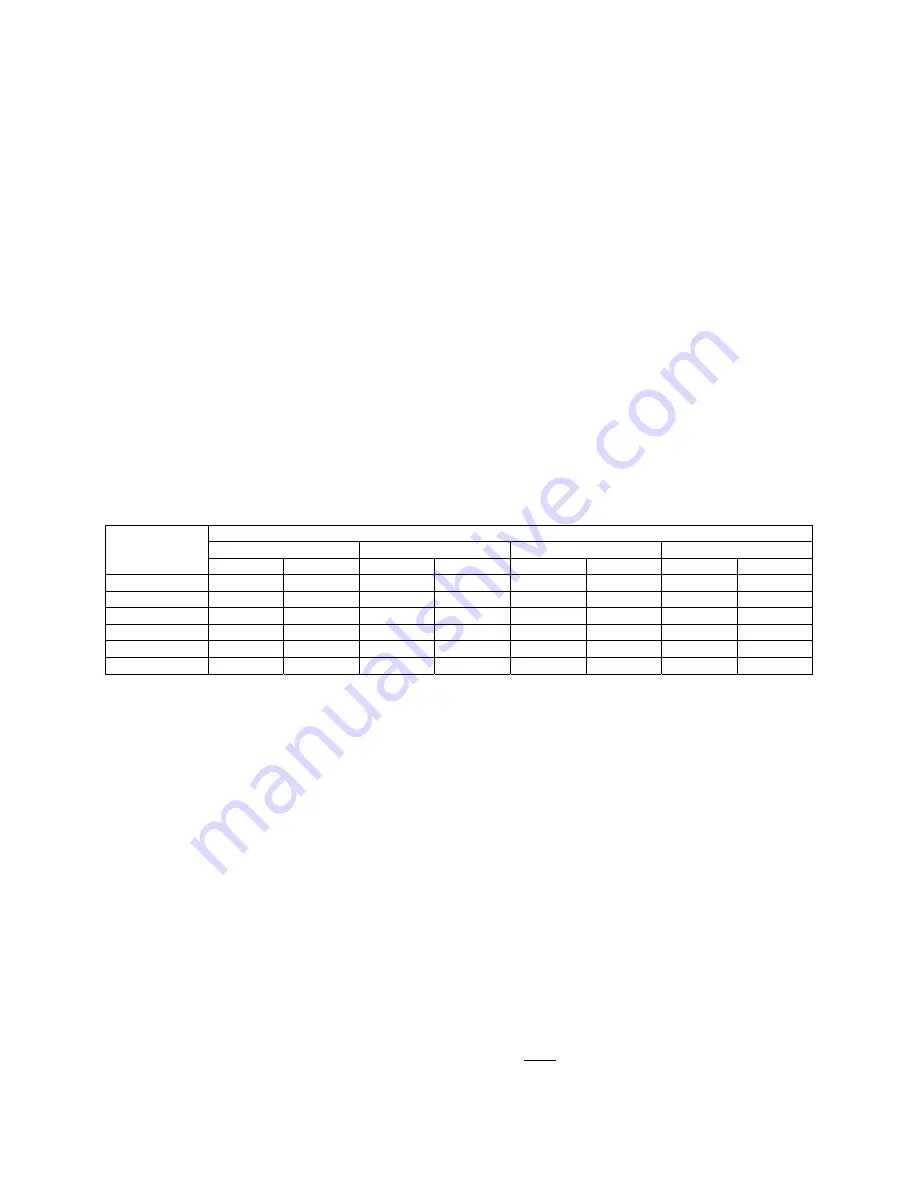
03/12/2019
1
BI309
GENERAL
As stated, this product series applies to under floor hydronic heating. The basic
components
for an electric
energy heating system typically include:
1.
Electric Mini-Boiler itself – covered by this manual.
2.
Thermostat hookup control – covered by this manual.
3.
Plumbing kit or piping material at the boiler itself – can be ordered as a kit, reference catalog number EMB-PK.
a.
These items are shown on plumbing installation drawing BX305.
4.
Circulating pump – typically sized for head pressure and system flow requirement, typical catalog number EMB-P2.
5.
The under floor circulating tubes and manifolds – provided and manufactured by others, not covered in this manual.
APPROVED TUBING/PIPING
When plumbing this boiler and its peripheral parts to the loop system, all plumbing parts and/or tubing must be
sealed to prevent entrance of oxygen.
Use only tubing or polyethylene tubing with oxygen Diffusion Barrier (ie. PEX).
SYSTEM OR WATER FLOW
In order to prevent rapid stage cycling and long term deterioration of components and elements, it is important
the water flow be greater than the specified 0.3 GPM per kW.
WATER FLOW REQUIREMENTS
(MINIMUM 0.3 GPM PER KW WATER FLOW THROUGH BOILER)
Model
Water Temperature Rise
Flow – 10° F/6° C
Head Loss
Flow – 20° F/11° C
Head Loss
gpm lpm ft m gpm lpm ft m
EMB-S-1 .75 2.83 .01 .003 .37 1.39 .003 .001
EMB-S-2 1.7 6.43 .01 .006 .85 3.21 .02 .006
EMB-S-4 3.41 12.88 .08 .024 1.70 6.42 .04 .012
EMB-S-5 3.07 11.60 .06 .018 1.53 5.78 .02 .006
EMB-S-7 4.78 18.06 .12 .036 2.39 9.03 .06 .01
EMB-S-9 6.14 23.20 .23 .07 3.07 11.60 .10 .03
Note: Head Loss based on 110° F return temperature.
TEMPERATURE SENSING STAGING CONTROL
This model series is factory equipped with a digital supply water sensor and a staging controller. The controller
regulates the elements to maintain a preset maximum or preset operating temperature. The control board has a
front panel screwdriver adjustment (see Operational Tips section) for setting the operating temperature point.
During initial turn on (slab stat call for heat) there is an initial pump on in attempt to stabilize the loop
temperature followed by stage 1. After approximately 4 minutes if the water supply sensor value is still below
the set point, stage 2 is turned on. At this point, the water temperature is sampled every 4 minutes to determine
correct element sequence. Assuming proper flow, the element power will regulate to maintain this preset
temperature.
ROOM THERMOSTAT PLACEMENT
Comfort and proper space heating response is a direct relationship to the room thermostat type and the
placement of the thermostat sensing bulb. Typically an under floor heating system can be broken down into two
categories.
Energy storage, water tubing is under the concrete or within the sand base
- The controlling
thermostat must have a remote bulb, and this remote bulb must sense the concrete slab temperature (slab
stat). Coordinated with the concrete pour, install a ¾” PVC, minimum bend radius of 7 inches, and
locate at approximately center (vertical) of the concrete slab. The thermostat sensing bulb can later be
Summary of Contents for Mini-Boiler EMB-S-1
Page 12: ...EMB S H 12 04 18 1 of 2 BX305 ...
Page 13: ...EMB S H 12 04 18 2 of 2 BX305 ...
Page 14: ...EMB S EMB H 03 19 19 1 of 2 BH310 G ...
Page 15: ...EMB S EMB H 03 19 19 2 of 2 BH310 G ...
Page 16: ...DECAL TITLEBLOCK ...