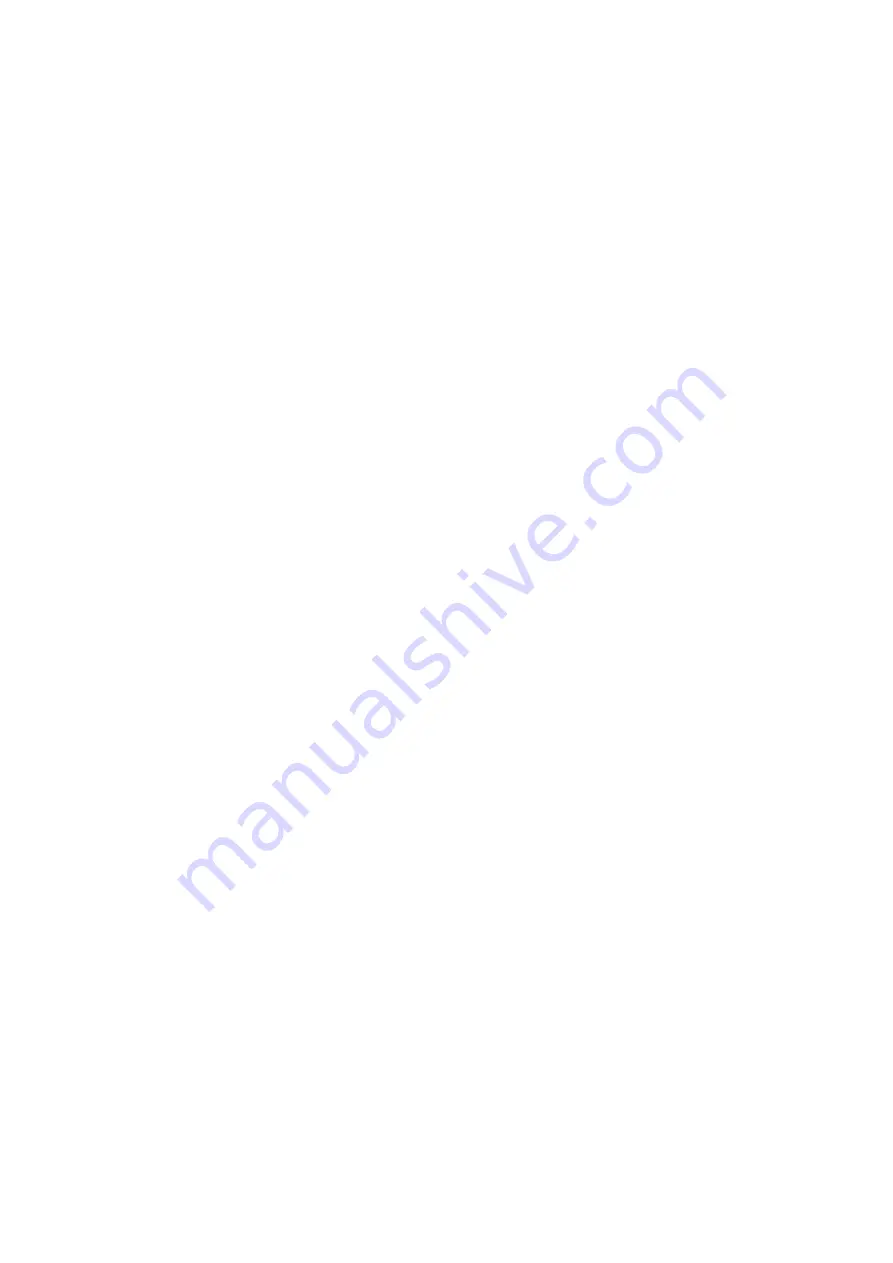
ELCO spa - ELK 39 - OPERATING INSTRUCTIONS - Vr. 02 - ISTR 06262 - PAG. 12
AL1H – HIGH ALARM AL1: Alarm AL1 high threshold when the
alarm is a band type or maximum set of AL1 alarm threshold when
the alarm is low or high type.
HAL1 - ALARM AL1 HYSTERESIS: Asymmetrical semi-band
relative to alarm AL1 threshold which defines the deactivation value
of alarm AL1.
AL1d – ACTIVATION DELAY OF ALARM AL1: This permits
definition of alarm delay activation AL1 when the delay function on
par. “Ab1” is activated.
AL1i – ALARM AL1 ACTIVATION IN CASE OF MEASUREMENT
ERROR: This permits a definition of measurement error conditions,
i.e whether the alarm has to be active ("yES") or not ("no").
GROUP “LbA” (PARAMETERS RELATIVE TO THE LOOP
BREAK ALARM): this contains the parameters relative to the
Loop Break alarm (control loop interruption), which intervenes
when, for any reason (short-circuit of a thermocouple, load
interruption, etc) the control loop is interrupted.
OLbA – OUTPUT WHERE THE LOOP BREAK ALARM IS
ADDRESSED: This defines to which output the LOOP BREAK alarm
has to be addressed.
LbAt – TIME NECESSARY TO ACTIVATE THE LOOP BREAK
ALARM : Delay time to the intervention of the Loop Break alarm.
The alarm intervenes when the output power remains at 100% for
the time programmed on this parameter (in sec.)
GROUP “
]
rEG” (PARAMETERS RELATIVE TO THE CONTROL):
this contains the parameters relative to control functions.
Cont – CONTROL TYPE: This permits selection of one of the
possible control modes offered by the instrument : PID (Pid),
ON/OFF with asymmetrical hysteresis (On.FA), ON/OFF with
symmetrical hysteresis (On.FS), Neutral Zone ON/OFF (nr).
Func – FUNCTIONING MODE OUTPUT 1rEG: this permits one to
decide whether the control output 1rEG has to carry out a reverse
action, as for example a Heating process ("HEAt") or a direct action,
as for example a Cooling process ("CooL").
HSEt –ON/OFF CONTROL HYSTERESIS: Semi-band relative to
the Set Point which defines the activation and deactivation values of
the control output/s in case of ON/OFF control (On.FA, On.FS, nr).
CPdt – COMPRESSOR PROTECTION DELAY TIME: The delay
time is counted starting from the last 2rEG output switch off , when
it’s used as Neutral zone control mode, during which the output is
kept in off state. The output will be switched on when the
temperature regulator requires it at this time is elapsed. The function
in deactivated programming "CPdt" = OFF.
Auto – AUTO-TUNING FAST ENABLE : this parameter allows one
to decide how Auto-tuning has to be carried out. The possible
selections are :
= 1 – if auto-tuning is desired automatically, each time the
instrument is switched on, on the condition that the process value is
lower (with “Func” =HEAt) than [SP- |SP/2|] or higher (with “Func”
=CooL) than [SP+ |SP/2|].
= 2 – if auto-tuning is desired automatically, the next time the
instrument is switched on, on the condition that the process value is
lower (with “Func” =HEAt) than [SP- |SP/2|] or higher (with “Func”
=CooL) than [SP+ |SP/2|], and once the tuning is finished, the par.
“Auto” is automatically swapped to the OFF state
= 3 - if manual auto-tuning is desired, by selecting par. “tunE” in
the main menu or by correctly programming key “U” as “USrb” =
tunE. In this case the auto-tuning starts without any control on the
process value condition. It is recommended to use this option,
starting the auto-tuning when the process value is as far as possible
from the Set Point because, in order to feature the Auto-tuning
FAST with its best performances , it is preferable to respect this
condition.
= 4 - if it’s desired to activate the autotuning automatically at the
end of programmed Soft-Start cycle. The Autotuning will start at the
condition that the process value is lower (with “Func” =HEAt) than
[SP- |SP/2|] or higher (with “Func” =CooL) than [SP+ |SP/2|].
= OFF - Autotuning disabled.
When it’s occurring an Autotuning cycle, led AT blinks.
SELF – SELF-TUNING ENABLE: Parameter used to enable (yES)
or disable (no) the Self-tuning function. Once the function has been
enabled, the Self-tuning has to be started by selecting item “tunE”,
in the main menu, or through key U properly programmed (“USrb” =
tunE).When the Self-tuning function is active, led AT is permanently
lit, and all the PID parameters ("Pb", "Int", "dEr", ecc.) are no longer
visualised.
Pb – PROPORTIONAL BAND: Width of the band around the Set
Point within which the proportional control is performed.
Int – INTEGRAL TIME: Integral time to be programmed in the PID
algorithm, expressed in sec.
dEr – DERIVATIVE TIME: : Derivative time to be programmed in the
PID algorithm, expressed in sec.
FuOc - FUZZY OVERSHOOT CONTROL: Parameter that permits
the elimination of the variable over-shoots at the start up of the
process or at the changing of the Set Point. A low value of this
parameter reduces the overshoot while a high value increase it.
tcr1 – CYCLE TIME OF OUTPUT 1rEG : Cycle time of output 1rEG
with PID control mode, expressed in sec..
Prat – POWER RATIO 2rEG / 1rEG : Parameter where it is possible
to program the power ratio between the element controlled by output
2rEG (ex.Cooling) and the element controlled by output 1rEG (ex.
Heating) in case of PID double action control.
tcr2 - CYCLE TIME OF OUTPUT 2rEG : Cycle time of output 2rEG
with PID double action control mode, expressed in sec..
rS - MANUAL RESET: Power Offset added to the power increase of
the proportional term, in order to eliminate the error when it is not
present the integral value. This parameter is only visualised when
“Int” =0.
Parameters relative to the ramps, allowing the Set Point to be
reached in a predetermined time.
Furthermore, once the first Set (SP1) has been reached, it is
possible to have automatic switching to the second Set (SP2)
after a programmable time, thus obtaining a simple thermal
cycle (functions available for all the control types)
SLor – GRADIENT OF RISE RAMP: Gradient of rise ramp to be
carried out when the process value is lower than the active Set
Point, expressed in unit/minute.
Programming the parameter = InF the ramp is not active.
dur.t - DWELL TIME: Dwell time of the Set Point SP1 before the
automatic switching to SP2 (expressed in hrs. and min.)
Using this parameter, once the first Set (SP1) has been reached, it
is possible to have automatic switching to the second Set (SP2)
after a programmable time, thus obtaining a simple thermal cycle.
Programming the parameter = InF the function is not active.
SLoF - GRADIENT OF FALL RAMP: Gradient of fall ramp to be
carried out when the process value is higher than the active Set
Point, expressed in unit/minute.
Programming the parameter = InF the ramp is not active.
Parameters relative to the Soft-Start function, which allows
limitation of control power, when the instrument is switched
on, for a predetermined time. This function is only available for
PID control.
St.P - SOFT START POWER: If parameter “SSt” is programmed
with a value other than OFF, this is the power given as output at the
instrument switch on, for the time “SSt”.
Practically speaking, the instrument works in manual condition and
switches to automatic control at the elapsing of time “SSt”.
If instead par. “St.P” = OFF and a value is set on par. “SSt” at
switch on, the power calculated by the PID controller is divided by
the time “SSt”, in order to calculate a ramp. The output power starts
from 0 and is progressively increased, according to the calculated
ramp, until the time “SSt” is reached or until the power overcomes
the power calculated by the PID controller.
SSt - SOFT START TIME (for PID control only): Duration time in
hours and min. of the Soft-Start described on pa. “St.P”.
To disable the Soft-Start function set par. “SSt” = OFF.
GROUP “
]
PAn” (PARAMETERS RELATIVE TO THE USER
INTERFACE) : This contains the parameters relative to the key
U and display functions.
Usrb – KEY U FUNCTION : Decides which function is associated to
key U. The possible selections are :
= noF : no function