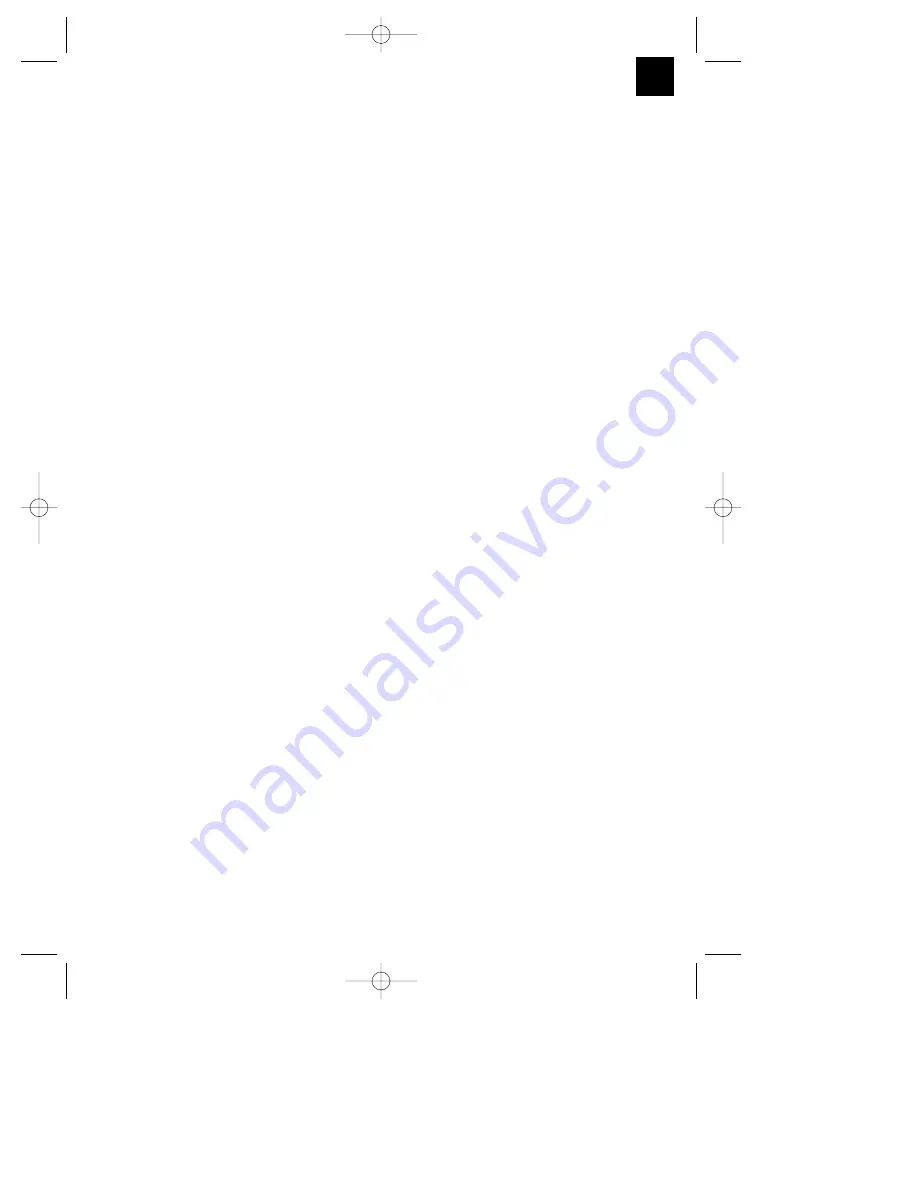
GB
5
The level of noise at the workplace may exceed 85
dB(A). In this case you will need to introduce noise
protection measures for the user. The noise pro
duced by this electric tool was measured in accor
dance with ISO 3744, NFS 31-031 (84/637/EEC).
Vibration emission was measured in accordance
with ISO 8662-8.
5. Prior to operation
Before starting the router, make sure that all its
guards and safety devices are properly fitted.
Before connecting up the router, make sure that
your power supply complies with the data on the
machine’s rating plate.
6. Assembly and operation
Important!
Pull out the power plug before fitting any parts or
making any adjustments.
A.) Fitting the extractor socket (Fig. 3)
Important!
For the sake of your health, always use a dust
extractor.
Use the two countersunk head screws (a) to fasten
the extractor socket (10) securely to the routing base
(12).
The extractor socket is suitable for dust extractors
with a suction hose diameter of 36 mm.
For other diameters you must use the extractor
adapter (20).
B.) Fitting the parallel stop (Fig. 4)
Insert the guide shaft (a) of the parallel stop (18) in
the holes (b) of the routing base (12).
Adjust the parallel stop (18) to the required
distance and clamp it in place with the thumb
screws (11).
Plug the scale (16) on the guide shaft (a).
C.) Fitting the guide roller (Fig. 5)
Use the two screws (a) to fasten the guide roller
(19) to the parallel stop (18).
Insert the parallel stop (18) in the routing base
(12).
Place the machine on the material.
Move the guide roller (19) against the edge of the
material and adjust to the required distance.
Use the thumb screws (11) to fasten the parallel
stop (18) in position.
Switch on the machine, lower the router and move
the guide roller (19) along the edge of the material
so that there is only slight counter-pressure.
Switch off the machine and return it to starting
position.
D.) Fitting the trammel point (Fig. 6)
Push the trammel point (17) onto the guide shaft
(a) of the parallel stop (18) and fasten it in place
with the thumb screw (b).
Important:
The parallel stop has to be turned over
so that the stop rail faces up.
Place the trammel point against the material.
Set the required radius by adjusting the parallel
stop (18) and fixing it in place with the two thumb
screws (11).
Switch on the machine.
After releasing the clamping handle (24), lower the
machine slowly as far as the stop (see section I.).
Cut grooves, shoulders, etc. at a steady rate of
feed, holding the machine with both hands.
When finished, raise the machine again.
Switch off the machine.
E.) Fitting the guide bush (Fig. 7/8)
Use the two countersunk head screws (f) to fasten
the guide bush (13) to the routing base (12).
The template (c) is traced with the guide ring (b) of
the guide bush (13).
To obtain an exact copy, the workpiece (d) must
be bigger by an amount equal to the difference
between the ‘outer edge of the guide ring’ and the
‘outer edge of the cutter’ (e).
F.) Fitting the base plate (Fig. 9)
Use the countersunk head screw (c) to fasten the
base plate (15) to the bottom of the routing base
(12).
The base plate can be used to cut along templates
with larger radii.
G.) Fitting the universal stop (Fig. 9)
Screw the stop rail (a) of your choice to the univer
sal stop (23).
Use the two screws (b) to fasten the universal stop
(23) to the routing base (12).
Anl. BOF 700-1 GB,I,FIN 05.07.2001 14:49 Uhr Seite 5