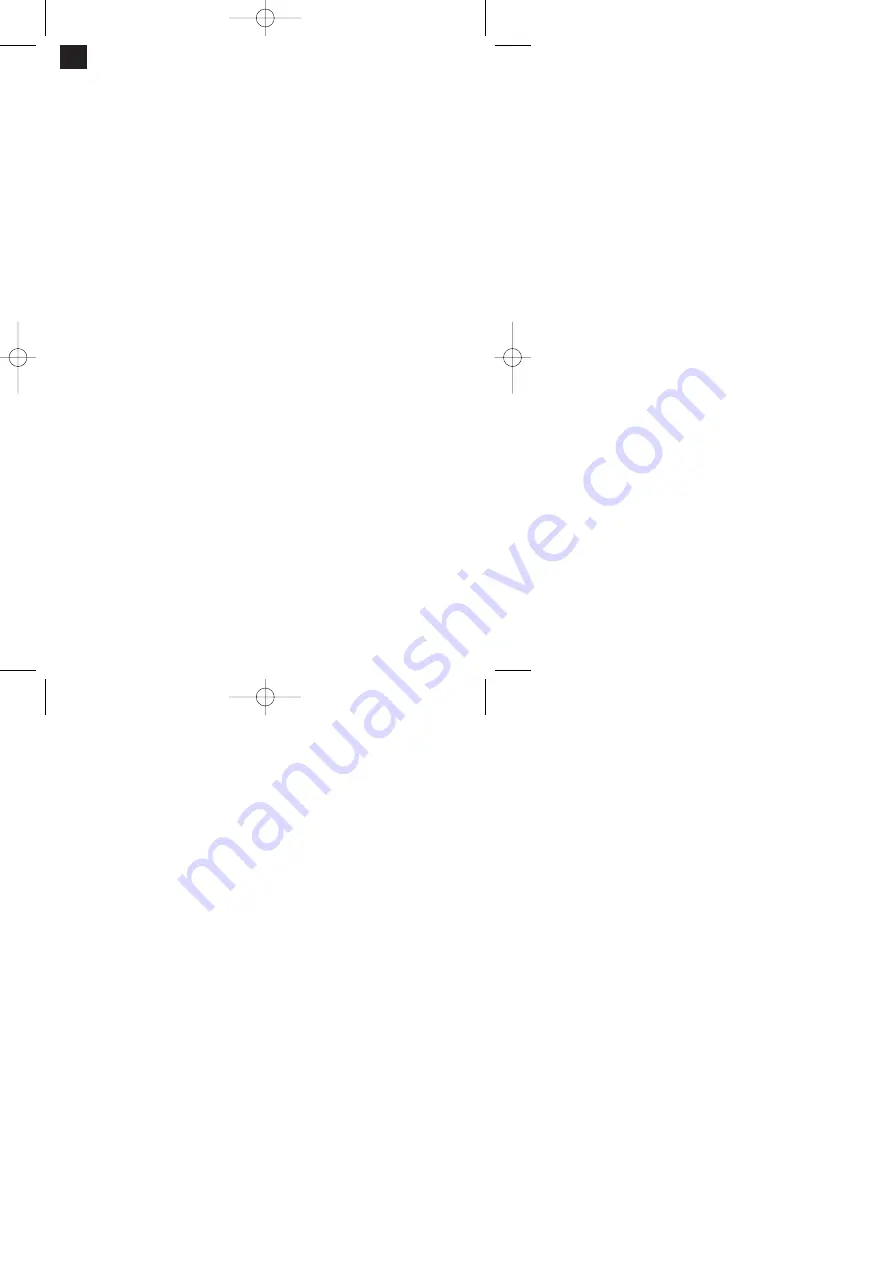
10
GB
The extraction port can be connected to extractor
units (vacuum cleaners) with a suction hose.
6.2 Fitting the parallel stop (Fig. 5)
Push the guide shafts (a) of the parallel stop (13)
into the holes (b) on the routing shoe (11).
Set the parallel stop (13) to the required dimension
and secure it in place with the wing screws (8).
6.3 Fitting the compass point (Fig. 6)
You can route circular areas using the compass
point (10) and the mounting to go with it.
Clamp the compass point (10) to the end of one of
the guide rods (a). Push the guide rod (a) into a
hole (c) on the routing shoe (11). Secure the guide
rod (a) on the routing shoe (11) using the securing
screws (8).
Set the required radius between the compass point
(10) and cutter.
Position the compass point (10) in the center of the
circle you wish to route. If necessary undo the wing
screw (b) on the compass point (10) and
extend/shorten the part of the compass point (10)
that points downwards.
Switch on the machine
After undoing the securing handle (15) slowly move
the machine downwards as far as it will go.
Route grooves, shoulders, etc. with a uniform feed
speed. Guide the machine with both hands as you
route.
After completing the work move the machine back
upwards.
Switch the machine off.
6.4 Fitting the guide sleeve (Fig. 7/8)
Secure the guide sleeve (9) to the routing shoe (11)
using the two countersunk screws (f).
The guide sleeve (9) is guided along the template
(c) using the guide ring (b).
The workpiece (d) must be larger by the difference
of “external edge of guide ring” and “external edge
of router” (e) to obtain a precise copy.
6.5 Fitting the cutting tool (Fig. 9)
Important: Remove the power plug.
Press the spindle lock (12) and allow the spindle to
engage by turning it at the same time.
Undo the clamp nut (a) using the open-ended span-
ner (14).
Select the appropriate cutting tool for the job in
hand.
Select the appropriate clamp for the cutter.
Now fit the clamp and nut into the cutting spindle.
Press and hold the spindle lock (12).
Tighten the clamp nut (a) using the open-ended
spanner (14).
The cutter must project out of the nut by at least 3
mm.
Before you start the electric router, check to ensure
that the cutting tool is secure and runs smoothly.
Important: Remove the setting and assembly
tools before starting the machine.
Changing the cutter:
Pull the mains plug and wait
until the cutter reaches a complete standstill. Now
press the spindle lock (12). Undo the clamp nut
using the open-ended spanner (14). Now take the
clamp and cutter out of the cutting spindle.
Important: The cutter may have become hot during
the routing work. You can now fit a new cutter.
6.6 Adjusting the routing depth (Fig. 10)
Place the machine on the workpiece
Undo the wing screw (a) and fixing handle (15)
Slowly move the machine downwards until the cut-
ter makes contact with the workpiece.
Tighten the fixing handle (15).
Set the depth stop (3) to the required routing depth
using the scale and secure it with the wing screw
(a).
Press the ON/OFF switch (6) to switch on the
machine.
Set the required speed on the routing tool using the
speed adjuster (7).
Undo the fixing handle (15) again and lower the cut-
ter to start the routing process.
After completing the work, the machine must be
returned to its initial position.
The speed of the router depends on the material you
wish to route, the feed speed and the routing tool you
wish to use.
6.7 Cutting direction (Fig. 11)
Always cut on a counter-rotating basis. Otherwise
there is a risk of injuries caused by kick-back.
Anl BOF 850-1 E_SPK1:_ 21.12.2006 9:00 Uhr Seite 10