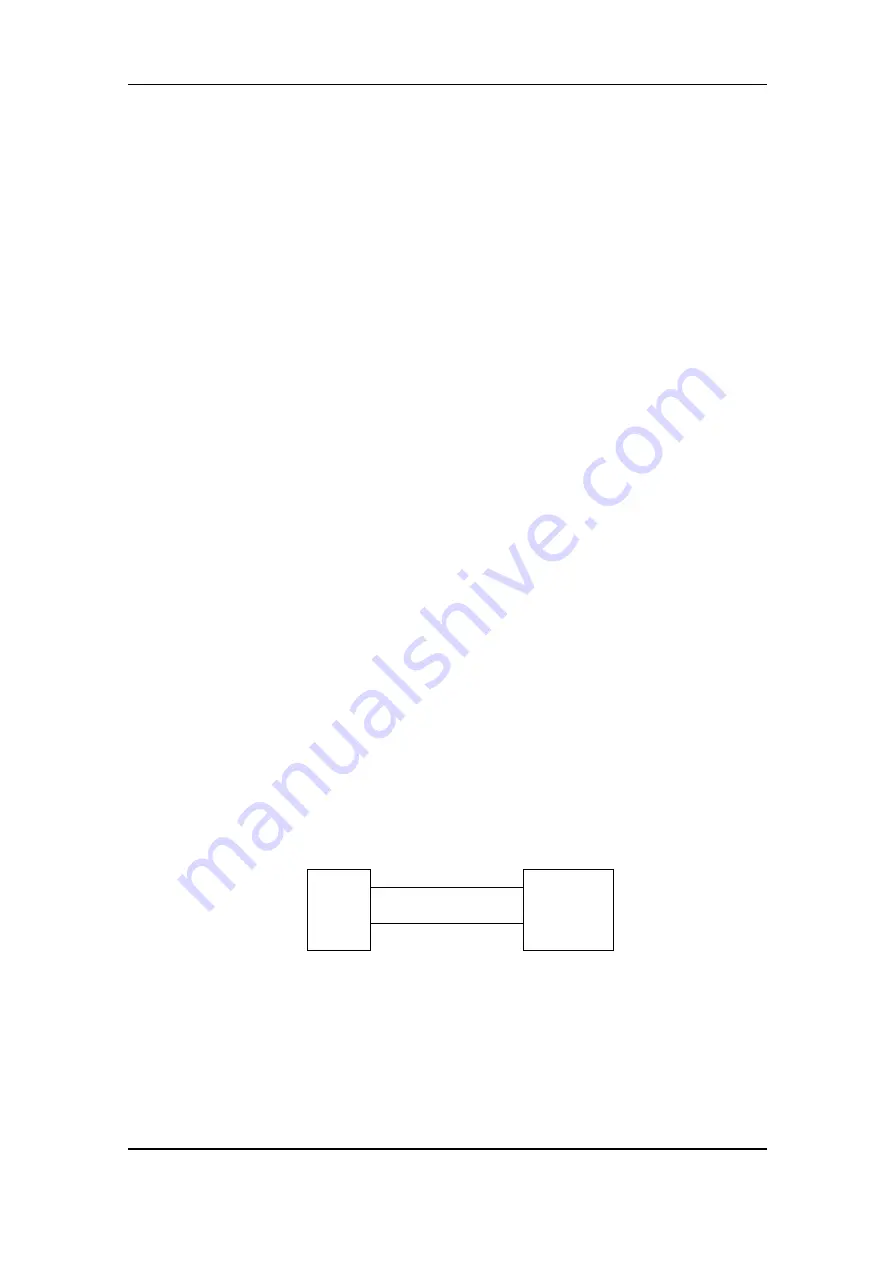
O2- Kompmaster
Page 4
All rights reserved. May not be photocopied or stored on a retrieval system without the prior written permission of EHS.
Only for use in conjunction with an Aerotronic control unit. © EHS - Engineering 2003
For more information, see
http://www.komposttechnik.de
3.3 Inputs
The input signals of the temperature sensors and the oxygen sensor are processed as ana-
log currents of 4 to 20 mA. The inputs are momentarily protected against over-voltage
and electrical interference.
For details please see the “Technical Specifications” table.
Only connect measuring sensors authorized by EHS.
3.4 Outputs
The control output is designed as a potential-free make contact with a maximum load of
30 V and 1 A. The control output is used in the system to operate a relay (usually 24V
relay) which again controls the fan.
Switch “open” = Signal blocked
Switch “closed” = Signal switched
Direct control of bigger loads than specified, e.g. a fan with higher voltages and currents
is prohibited and will damage the control unit.
The device is exclusively designed for low voltage. Non-observance of this specifi-
cation makes any warranty claim null and void.
4 Interfaces
The are two control unit variations with different interfaces to the control PC.
(1) RS232/V24 “Stand-alone“ operation
Units which will not be networked are equipped with this interface. When oper-
ating several controls, you must connect them to the PC alternately to configure
the control or download the data.
The specification of the RS232/V24 interface in hardware and software complies
with the usual PC standard.
(2) In networked operation via RS485, up to 32 units can be operated at one PC in-
terface. Since this is not a standard PC interface, suitable converters must be
used. The RS485 interface is operated in 4-wire full-duplex mode, with each unit
having its own network address which is set by means of micro-switches inside
the control unit. The control units are connected to each other and to the inter-
face converter using a four-wire line. The wiring diagram is as follows:
PC
Komp-
master
TxD
RxD