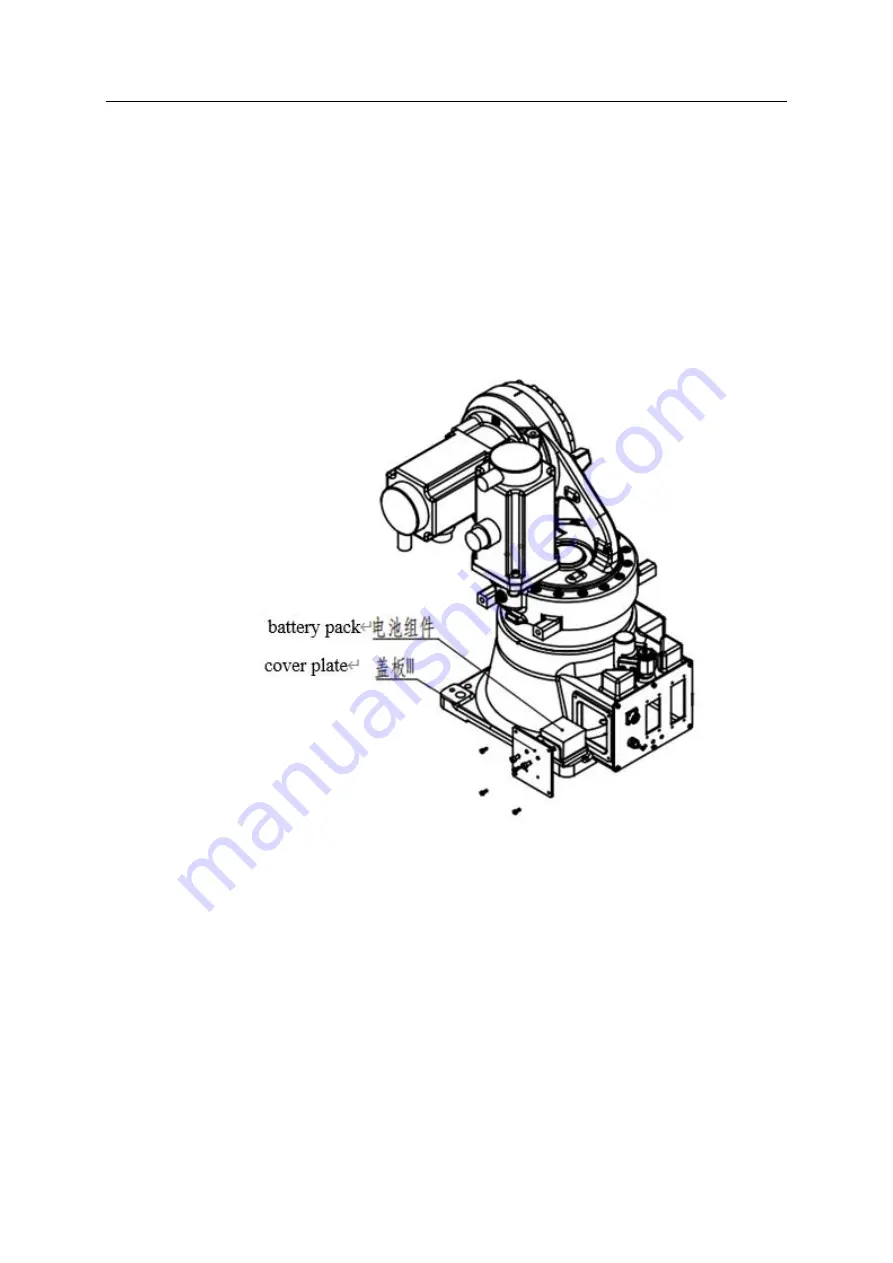
EFORT Intelligent Equipment Co., Ltd
38
Adjust the robot to calibration state (each axis in zero position). To prevent dangers, cut off the power
supply, hydraulic pressure source and air pressure source connected to the robot.
Remove the side cover plate of the base and remove the battery pack, as show in figure 4-6.
Remove the old battery from the battery box and load new battery. Differentiate the positive and negative
polarity of the battery. Reconnect the battery wiring and fix the pack.
Follow the steps to fix the rear cover plate of the base after installation.
Zero position calibration, verification and testing on precision of relative zero positions cannot start
until all the safety conditions are met. For detailed steps, see Chapter Zero Position Calibration in the
EFFORT Industrial Robot Operation Manual.
Fig. 4-6 Position of Battery Pack