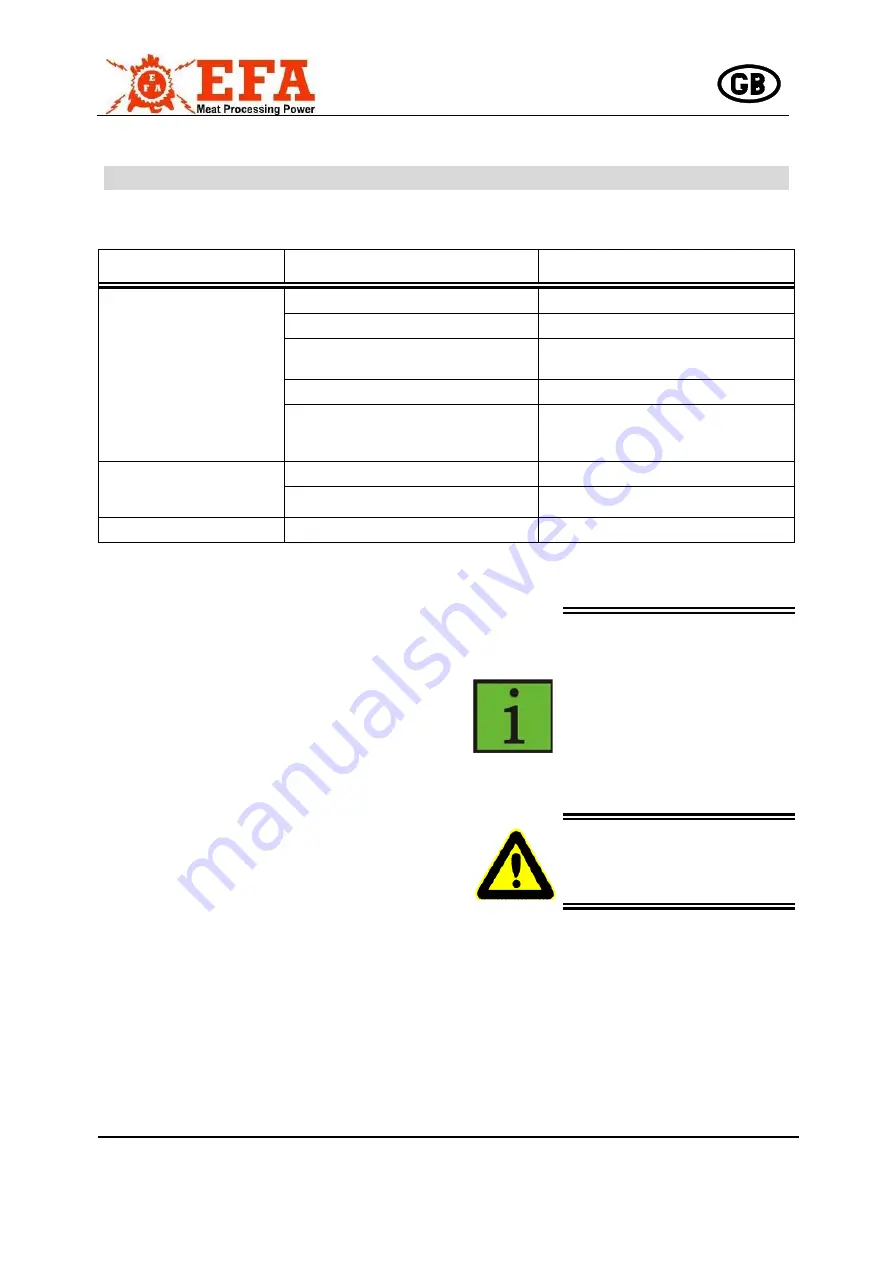
Schmid & Wezel
Seite / Page
38 / 53
Ausführung / Version
02 / 2011
7. Repairs and Troubleshooting
7.1 List of faults
Malfunction Cause
Solution
The unit does not start
when the trigger handle is
pressed
Air filter on maintenance unit clogged
Replace air filter
Loose hose connection
Check correct hose connection
Motor or gear box parts defective
Inspect wearing parts, replace if
necessary
Rotor slide defective
Replace rotor slide
Parts of the unit are rusty, because
there is water in the supply line or the
maintenance unit is defective
Check the parts or the maintenance
unit and replace if necessary
The switch lever can not
be pressed, or only with
difficulty
Valve spring broken
Replace valve
Valve jammed due to soiling
Clean valve
Handle iced
Air pressure set too high
Regulate the air pressure to 7 bar
Tab. 1:
List of faults
Faults can occur during operation but the
solutions are, in most cases, relatively simple.
The list of faults contains various faults
together with their possible causes and related
corrective measures.
7.2 Repair by after-sales service
Repairs may only be carried out by
authorised specialists.
•
Our Service department is at your disposal
for all repair work.
In the event of a repair, please contact your
nearest service centre or our parent
company directly.
•
On request, spare parts lists can be
supplied to the repair workshop with
qualified specialist staff.
•
After every repair, the gear units must be
repacked with grease!
Defective devices should
never be repaired on site
because, in most cases, the
necessary tools and levels of
cleanliness are not available.
This is particularly the case
when the defective device is
in the direct vicinity of food
processing areas.
Disconnect the unit from the
mains power supply before
starting any repair work!
Basically, when the fault in the device cannot
be explicitly localised, it should be sent to S&W
for repair with the relevant information on the
fault symptoms.