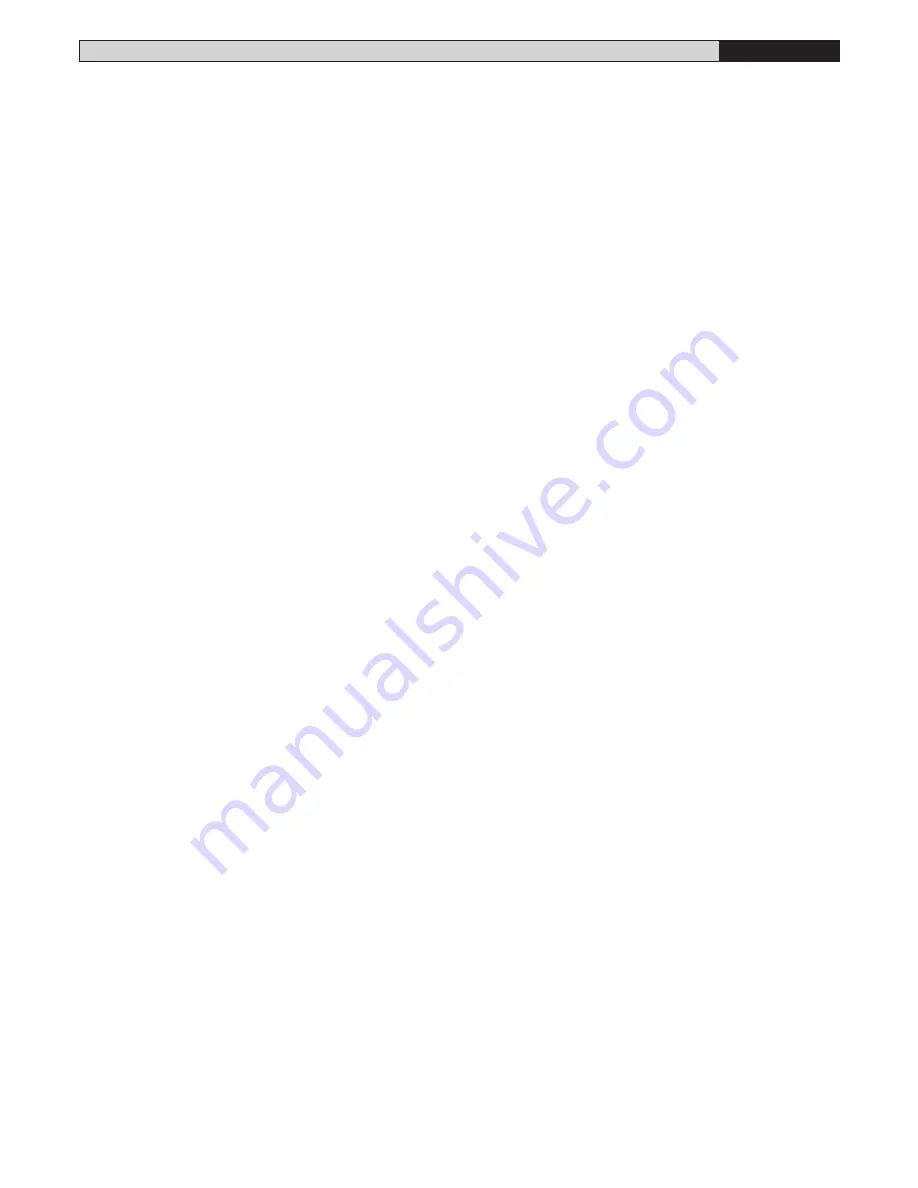
VIRGO Ver. 03 -
17
D811415_03
5) SUPPORT PLATE FIXING (Fig.2)
The operator is supplied with a fixing bracket and lever arm.
Having identified the leaf reinforcement point, with the gate closed, trace an
imaginary horizontal line from the centre of the reinforcement point to the
pillar (fig. 3-4).
Fig. 2 illustrates the most common types of installation:
-
with the leaf hinge pivot not aligned with the fixing plate
(90
°
opening – maximum distance between hinge pivot and plate:
210mm)
-
with the hinge pivot aligned with the fixing plate
Position the anchoring bracket observing the dimensions shown in fig.3 for
opening up to 90
°
, or in fig.4 for opening over 90
°
up to a max of 120
°
.
The pillar surface, where the bracket is fixed, must be flat and parallel to the
leaf. Use screws and expansion plugs adequate for the type of pillar. In the
case where the pillar surface is irregular, use expansion plugs with studs,
in order to be able to adjust the fixing bracket parallel to the leaf (fig.5).
•
Assemble the lever arm as in fig.7.
DX = fitting to right leaf
SX = fitting to left leaf
Choose the most suitable position for fixing bracket “F” to the leaf.
•
Insert lever L into the gearmotor output shaft, and fix it using appropriate
pivot P and self-locking nut D (fig.7).
•
Release the operator by activating the release lever to allow the arm to
move easily (see paragraph “EMERGENCY MANOEUVRE”).
•
Open the gearmotor cover and fix it to the plate as indicated in Fig.8.
•
Fix towing angle bar “F” to the leaf.
•
The correct position for the operator arm is illustrated in fig.6. The leaf
attachment point can be identified by positioning the arm according to
the dimension indicated in fig.6.
•
With the operator released, check the arm for correct movement.
•
Repeat the same procedure for the other leaf.
6) BACKSTOP FIXING
The VIRGO operator is provided with mechanical end-of-stroke backstops,
which make the installation of ground stop plates redundant.
With reference to Fig. 10 proceed as follows:
-
Identify the opening and closing end-of-stroke points and fix the backstops
accordingly.
-
Fix protection cover C.
7) ELECTRICAL INSTALLATION SET-UP
Arrange the electrical installation as shown in fig.11.
The power supply connections must be kept separate from the auxiliary
connections (photocells, sensitive edge, etc.).
For this purpose, the operator is provided with appropriate fittings, indicated
in Fig.9, for a spiral flexible raceway with an inside diameter of 20:
- P1 input for mains power GND.
- P2/P3 inputs for safety devices and accessories.
For the mains power supply, use the appropriate cable clamp (Fig.9 -”S”),
the terminal bar with an incorporated protection fuse (Fig.9 -”L-N”) and the
GND terminal.
8Fig.11 shows the cross-section and the number of connections.
8) TERMINAL BAR CONNECTIONS (Fig.16)
NOTE: The VIRGO operators provided with incorporated LINX control
panels are preset for fitting to the left leaf, whereas the operators
without panels (VIRGO-SQ) are preset for fitting to the right leaf, as
illustrated by the example given in Fig.11.
Should it be necessary to reverse the operator opening direction, proceed
as follows:
1 – Reverse motor polarity (JP1 terminals 1-2)
2 – Reverse motor polarity (JP2 terminals 14-15)
WARNING
– During the wiring and installation operations, refer to the
current standards as well as principles of good technical practice.
Wires powered at different voltages must be physically separated, or
suitably insulated with at least 1 mm extra insulation. T
he wires must be clamped by an extra fastener near the terminals, for
example by bands.
All the connection cables must be kept at an adequate distance from the
dissipator(Fig.14 “D”).
WARNING! For connection to the mains, use a multipolar cable with
a minimum of 3x1.5mm
2
cross section and complying with the
previously mentioned regulations. For example, if the cable is out side
(in the open), it has to be at least equal to H07RN-F, but if it is on the
inside (or outside but placed in a plastic cable cannel) it has to be or
at least egual to H05VV-F with section 3x1.5mm
2
.
JP1
1-2
Motor 2 connection (VIRGO with LINX panel):
3-5
Opening limit switch SWO M2 (N.C.)
4-5
Closing limit switch SWC M2 (N.C.)
6-7
24 Va.c. power supply input from the transformer
JP2
8-9
24Va.c. Vsafe 180mA max output – power supply for photocell
transmitters with check (Fig.14)
10-11
24Va.c. 180mA max output – power supply for photocells or other
devices
12-13
Blinker connection (24Va.c. 25W max)
14-15
Motor 1 connection (VIRGO-SQ – without LINX panel - Fig.13a):
16-18
Opening limit switch SWO M1 (N.C.)
17-18
Closing limit switch SWC M1 (N.C.)
19-24
Pedestrian opening button PED (N.O.). Controls partial opening
of Motor M2.
20-24
Fault input (N.O.). Input for photocells or safety devices provided
with an N.O. check contact (Fig.14).
21-24
Photocell input (N.C.). If not used, leave bridged.
22-24
STOP button (N.C.). If not used, leave bridged.
23-24
START button (N.O.).
25-26
Output for gate-open warning light (N.O. contact (24Va.c./1A
max) or alternatively for 2nd radio channel (see configuration -
“logics” menu)
27-28
Antenna input for incorporated radio-receiver board (27 braid - 28
signal).
9) PROGRAMMING
The control panel provided with a microprocessor is supplied with function
parameters preset by the manufacturer, suitable for standard installations.
The predefined parameters can be altered by means of either the
incorporated display programmer or UNIPRO.
In the case where programming is carried out by means of UNIPRO,
carefully read the instructions relating to UNIPRO, and proceed in the
following way.
Connect the UNIPRO programmer to the control unit through the UNIFLAT
and UNIDA accessories (See fig. 18). The
LINX
control unit does not supply
the UNIPRO programmer with power, and therefore requires an appropriate
supply unit.
Enter the “CONTROL UNITS” menu, and the “PARAMETERS” submenu,
then scroll the display screenfuls using the up/down arrows to set the
numerical values of the parameters listed below.
For the function logics, refer to the “LOGIC” submenu.
In the case where programming is carried out by means of the incorporated
programmer, refer to Fig. A and B and to the paragraph on “Configuration”.
10) CONFIGURATION
The display programmer is used to set all the
LINX
control panel functions.
The programmer is provided with three pushbuttons for menu scrolling and
function parameter configuration:
+
menu scrolling/value increment key
-
menu scrolling/value reduction key
OK
Enter (confirm) key
The simultaneous pressure of the + and - keys is used to exit the active
menu and move to the preceding menu.
The modifications made are only set if the OK key is subsequently pressed.
When the OK key is pressed for the first time, the programming mode is
entered.
The following pieces of information appear on the display at first:
-
Control unit software version
-
Number of total manoeuvres carried out (the value is expressed in
thousands, therefore the display constantly shows 0000 during the first
thousand manoeuvres)
-
Number of manoeuvres carried out since the latest maintenance
operation (the value is expressed in thousands, therefore the display
constantly shows 0000 during the first thousand manoeuvres)
-
Number of memorised radio control devices.
When the OK key is pressed during the initial presentation phase, the first
menu can be accessed directly.
Here follows a list of the main menus and the respective submenus available.The
predefined parameter is shown between square brackets [ 0 ].
The writing appearing on the display is indicated between round brackets.
INSTALLATION MANUAL
ENGLISH