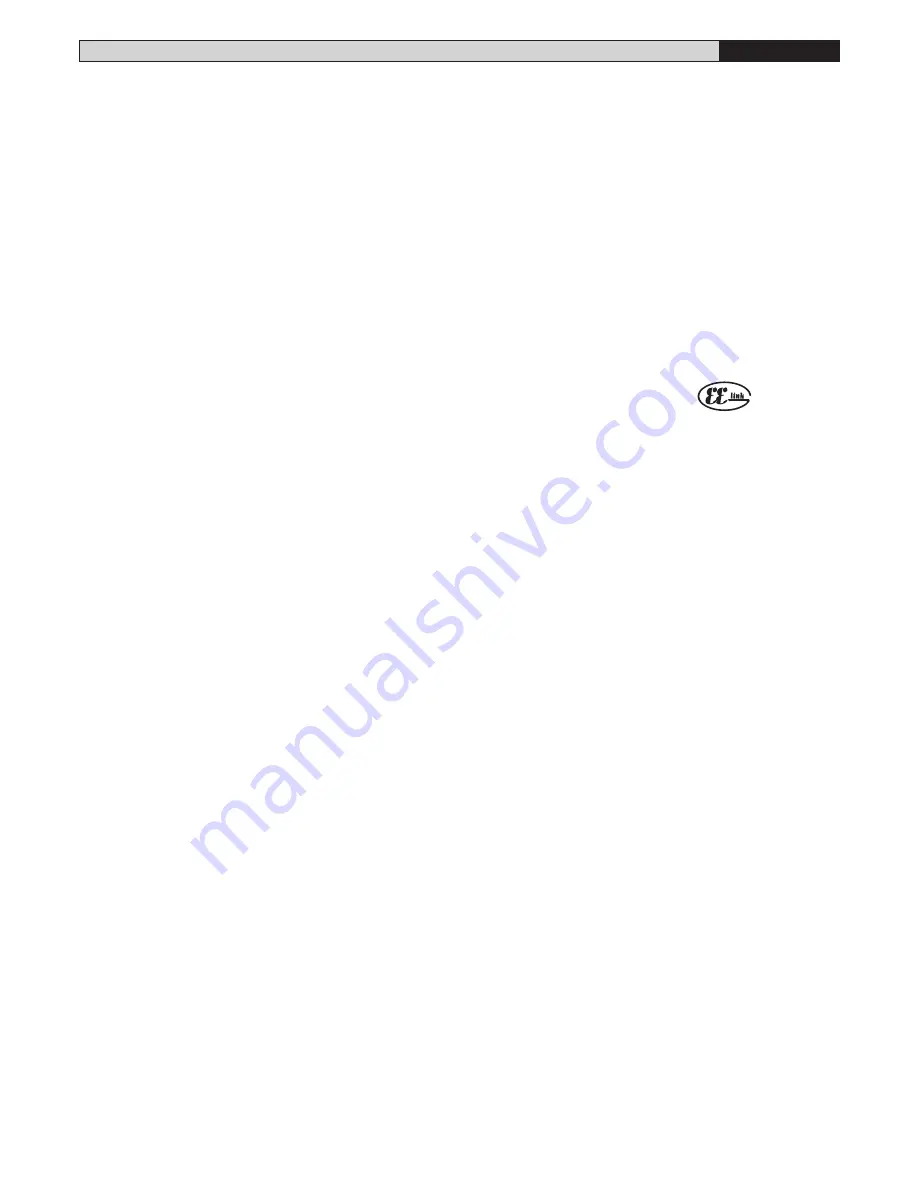
VIRGO Ver. 03 -
19
D811415_03
INSTALLATION MANUAL
ENGLISH
from the receiver memory.
-
Receiver code reading
(RX code)
This displays the code entered in the receiver.
Consult paragraphs 12-13-14-15 for further information concerning
the advanced functions of the Clonix incorporated receiver.
10.4) LANGUAGE MENU (
language
)
Allows you to set the language on the display programmer.
-
ITALIAN (
ITA
)
-
FRENCH (
FRA
)
-
GERMAN (
DEU
)
-
ENGLISH (
ENG
)
-
SPANISH (
ESP
)
10.5) DEFAULT MENU (
default
)
Restores the preset default values on the control unit. After restoring, a new
autoset operation must be carried out.
10.6) DIAGNOSTICS AND MONITORING
The display on the
LINX
panel shows some useful information, both during
normal operation and in the case of malfunctions.
Diagnostics:
In the case of malfunctions, the display shows a message indicating which
device needs to be checked:
PED = PED input activation
STRT = START
input activation
STOP= STOP input activation
PHOT= PHOT input activation
FLT
= FAULT input activation for checked photocells
In the case where an obstacle is found, the
LINX
panel stops the door and
activates a reverse manoeuvre; at the same time the display shows the
“AMP” message.
Monitoring
:
During the opening and closing phases, the display shows four digits
separated by a dot, for example
35.40.
The digits are constantly updated
during the manoeuvre, and represent the maximum torque reached by
motor 1 (
35
) and motor 2 (
40
).
These values allow the torque setting to be corrected.
If the maximum torque value reached during the manoeuvre gets sensibly
close to the value set in the parameter menu, malfunctions may occur in the
future following wear or slight door deformation.
It is therefore advisable to check the maximum torque reached during some
of the manoeuvres carried out in the course of installation, and if necessary
set a value about 15-20 percent points higher in the parameter menu.
10.7) AUTOSET MENU (
autoset
)
Allows you to automatically set the Motor torque.
WARNING!!
The autoset operation is only to be carried out after checking
the exact leaf (opening/closing) movement, and correct limit-switch
activation.
As soon as the OK pushbutton is pressed, the “.... ....” message is
displayed, and the control unit executes an opening manoeuvre followed by
a closing manoeuvre, during which the minimum torque value needed for
leaf movement is automatically set.
During this phase, it is important to avoid obscuring the photocells, as well
as using the START, STOP or PED commands and the display.
After this, if autosetting has been successfully completed, the control unit
displays the “OK” message and, after pressing any key, returns to the
Autoset menu.
If, on the other hand, the control unit displays the “KO” message, it means
that the autoset procedure has not been successfully completed; it is thus
necessary to check the wear condition of the gate and the regular movement
of the leaves before proceeding to a new autoset operation.
WARNING! During the autoset phase, the obstacle detection function is not
active, therefore the installer must control the automation movement and
prevent persons and things from approaching or standing within the
automation working range.
In the case where buffer batteries are used, autosetting must be carried out
with the control panel supplied by mains power voltage.
WARNING: Check that the impact force value measured at the
points established by the EN 12445 standard is lower than that
specified in the EN 12453 standard.
Incorrect sensitivity setting can cause injuries to persons or
animals, or damage to things.
11) STATISTICS
Having connected the UNIPRO programmer to the control unit, enter the
CONTROL UNIT / STATISTICS menu and scroll the screenful showing the
statistical parameters:
-
Board microprocessor software version.
-
Number of cycles carried out. If motors are replaced, count the number
of manoeuvres carried out up to that time.
-
Number of cycles carried out from the latest maintenance operation.
It is automatically set to zero after each self-diagnosis or parameter writing.
-
Date of latest maintenance operation. To be updated manually from the
appropriate menu “Update maintenance date”.
-
Installation description. 16 characters can be entered for installation
identification.
12) INTEGRATED RECEIVER TECHNICAL SPECIFICATION
Receiver output channels:
-
output channel 1, if activated, controls a START command.
-
output channel 2, if activated, controls the excitation of the 2nd radio
channel relay for 1s.
Transmitter versions which can be used:
all Rolling Code transmitters compatible with
ANTENNA INSTALLATION
Use an antenna tuned to 433MHz.
For Antenna-Receiver connection, use RG8 coaxial cable.
The presence of metallic masses next to the antenna can interfere with
radio reception. In case of insufficient transmitter range, move the antenna
to a more suitable position.
13) RECEIVER CONFIGURATION
The on-board receiver combines characteristics of utmost safety in copying
variable code (rolling code) coding with the convenience of carrying out
transmitter “cloning” operations thanks to an exclusive system.
Cloning a transmitter means creating a transmitter which can be automatically
included within the list of the transmitters memorised in the receiver, either
as an addition or as a replacement of a particular transmitter.
Cloning by replacement is used to create a new transmitter which takes the
place of the one previously memorised in the receiver; in this way a specific
transmitter can be removed from the memory and will no longer be usable.
Therefore it will be possible to remotely program a large number of
additional transmitters or, for example, replacement transmitters for those
which have been lost, without making changes directly to the receiver.
When coding safety is not a decisive factor, the on-board receiver allows
you to carry out fixed-code additional cloning which, although abandoning
the variable code, provides a high number of coding combinations, therefore
keeping it possible to “copy” any transmitter which has already been
programmed .
PROGRAMMING
Transmitter storage can be carried out in manual mode or by means of the
UNIRADIO programmer which allows the complete installation database to
be managed through the Eedbase software.
In this second case, receiver programming takes place through the
connection of UNIRADIO to the
LINX
control panel, using the UNIFLAT and
UNIDA accessories as indicated in Fig. 15.
14) MANUAL PROGRAMMING
In the case of standard installations where advanced functions are not
required, you can proceed to manual storage of the transmitters, making
reference to fig. B for basic programming.
-
If you wish the transmitter to activate output 1 (START) by means of
key1, key2, key3 or key4, enter the transmitter in menu “Start key”, as
in fig. B.
-
If you wish the transmitter to activate output 2 (2nd radio channel relay)
by means of key1, key2, key3 or key4, enter the transmitter in menu “2nd
ch. key”, as in fig. B.
Note:
Hidden key P1 appears differently depending on the transmitter model.
For transmitters with hidden key, press hidden key P1 (fig. B1). For
transmitters without hidden key, the key P1 function corresponds to
simultaneously pressing the 4 transmitter keys or, after opening the
battery compartment, bridging the two P1 points by means of a
screwdriver (fig. B2).