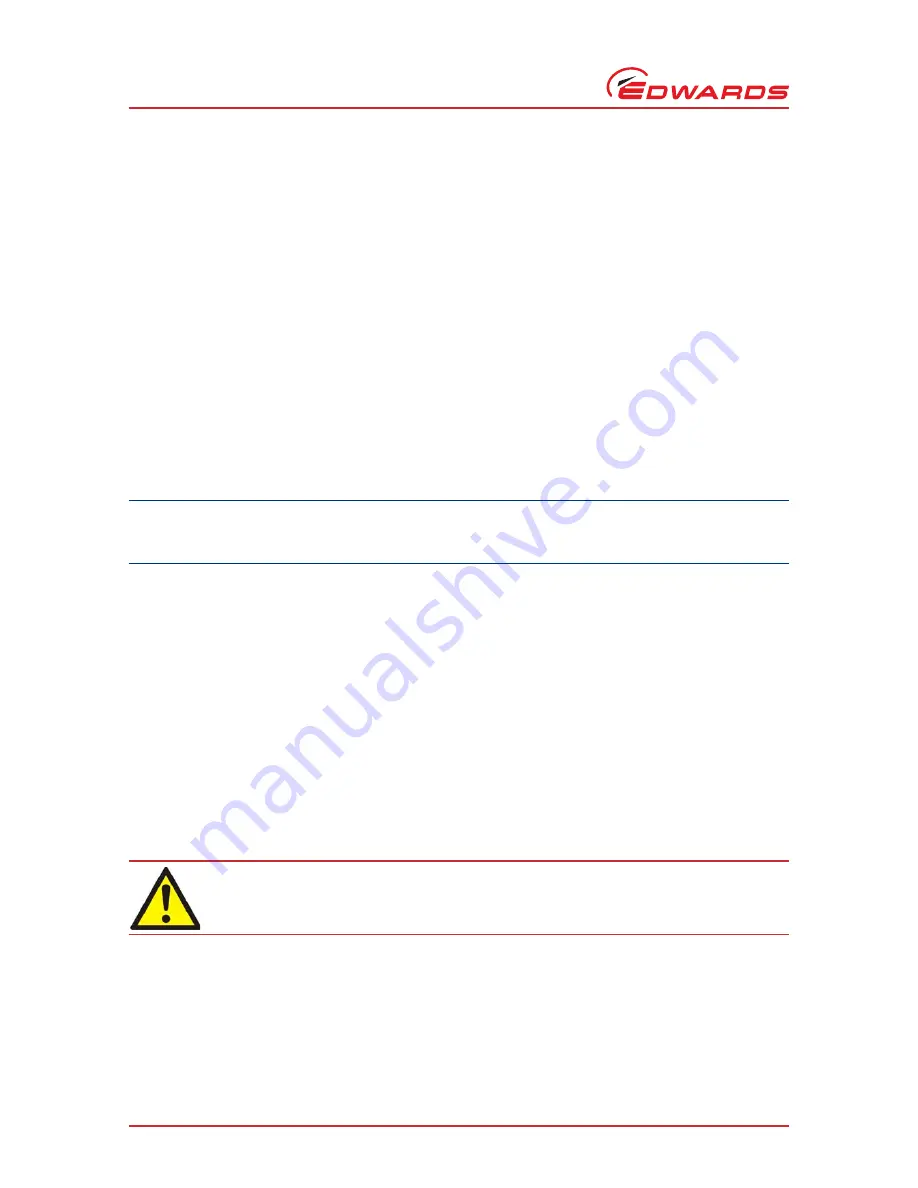
M561-00-880 Issue C
Page 48
© Edwards Limited 2012. All rights reserved.
Edwards and the Edwards logo are trademarks of Edwards Limited.
Maintenance
2. Connect a regulated clean dry air supply (5 barg or 73 psig) to the cooling water supply connection
(
Figure 4
, item 15). Do not turn on the air supply yet.
3. Connect a drain hose to the cooling water return connection (
Figure 4
, item 18). Position the open end of the
drain hose in a suitable collection container.
4. Turn on the clean dry air supply.
5. Monitor the drain hose outlet until no further cooling water is purged.
6. Fit the external EMS link plug (supplied) to the EMS connection on the rear of the system (
Figure 4
, item 10). If
you do not, you will not be able to purge the water system effectively.
7. Connect the system to a suitable mains electrical supply. The control system will now open each temperature
control valve, purging the cooling water from all flow paths. After two minutes, remove the electrical supply.
Wait for 10 seconds and then re-connect the electrical supply and repeat the entire process. Continue repeating
until no further cooling water is purged from the system.
8. The cooling water drain procedure is now complete. Disconnect the air supply, electrical supply and the drain
hoses. Dispose of the drained cooling water appropriately.
5.4
General maintenance
CAUTION
Do not use cleaning materials based on strong alkalis, aggressive or chlorinated solvents. Do not use cleaning
materials containing abrasives.
The system is given a charge of oil before it leaves the factory. You should not need to check or adjust oil levels
between major overhauls.
We recommend that you carry out a monthly visual inspection of the system in situ. Check that the cables, hoses
and pipelines bringing services to the pump are in good condition and ensure that all connections are secure.
The following maintenance can also be carried out on the system, contact Edwards for details and training:
Inspect the connections, pipelines, cables and fittings inside the pump enclosure, refer to
Section 5.5
.
Inspect and clean exhaust pipe, elbow, and check valve
Note:
The system is supplied with either a trapped O-ring or a metal seal for the exhaust connection, depending
on pump type and anticipated exhaust temperatures. Ensure that you always replace seals with the same
type.
5.5
Inspect the connections, pipelines, cables and fittings
If the system is not relocated for maintenance, ensure all supplies are locked out and tagged out before starting the
following procedure.
1. Remove the enclosure side and top panels.
2. Check that all the connections are secure; tighten any loose connections. Inspect all cables, pipelines, hoses and
connections and check that they are not corroded or damaged and do not leak; repair or replace any pipelines,
hoses and connections that are corroded or damaged, or which leak.
3. Refit the enclosure side and top panels.
WARNING
Electrical, nitrogen and water supplies are all potentially hazardous energy sources. Before
carrying out any maintenance the supply of these sources should be locked and tagged out.