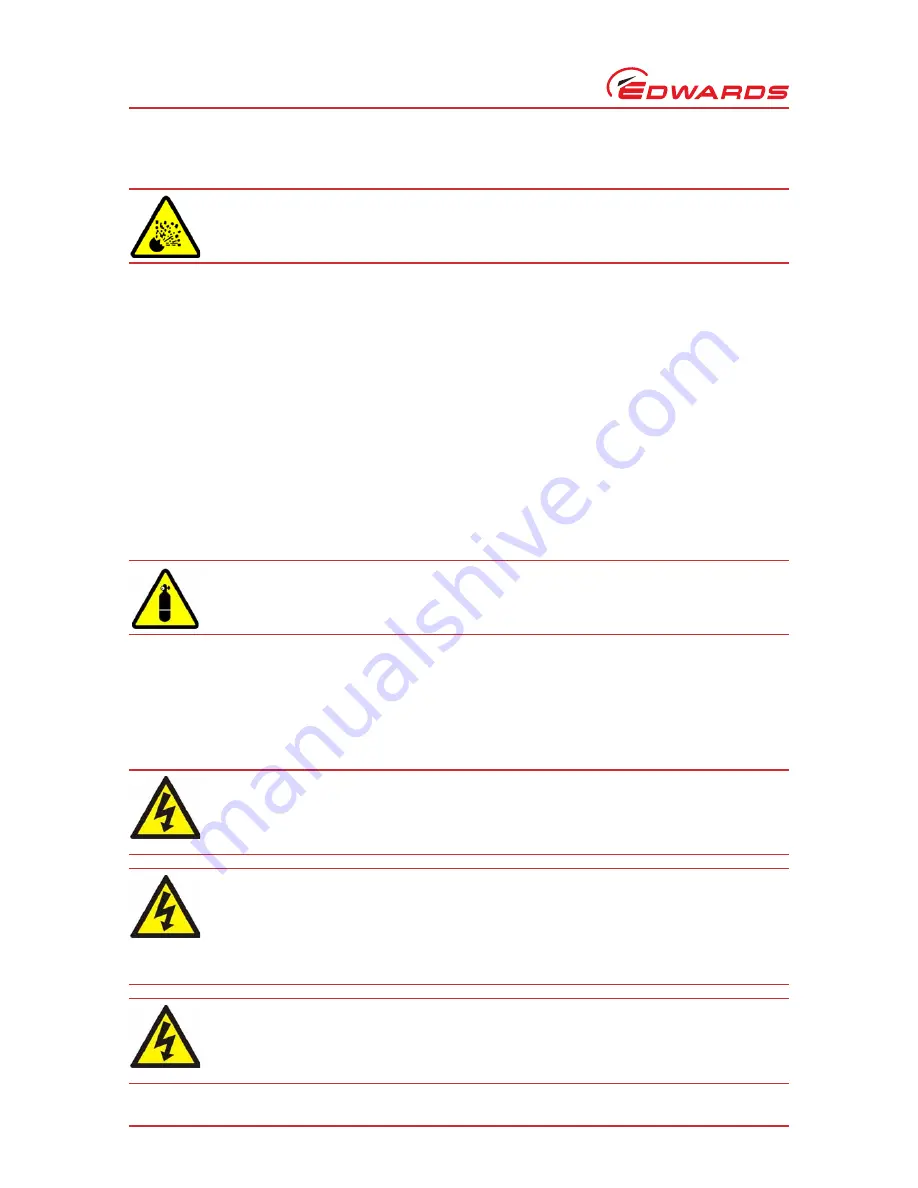
A590-00-880 Issue D
Page 18
© Edwards Limited 2008. All rights reserved.
Edwards and the Edwards logo are trademarks of Edwards Limited.
Installation
3.6.2
Gas purges
Switch on the inert gas purge to remove air from the pump and the exhaust pipeline before the process starts. Switch
off the purge flow at the end of the process only after the remaining flammable gases or vapours have been purged
from the exhaust pipeline.
If liquids that produce flammable vapours could be present in the pump foreline, then the inert gas purge to the dry
pumping system should be left on all the time this liquid is present. Flammable liquids could be present in the foreline
as a result of condensation or may be carried over from the process.
When calculating the flow rate of inert gas required for dilution, consider the maximum flow rate for the flammable
gases/vapours that could occur. For example, if a mass flow controller is being used to supply flammable gases to
the process, you should assume a flow rate for flammable gases that could arise if the mass flow controller is fully
open.
Continually measure the inert gas flow rate: if the flow rate falls below that required, then the flow of flammable
gases or vapours to the pump must be stopped.
3.7
Leak-test the system
Note:
If you need further information on leak-testing, look it up on the Web using URL at the start of manual, or
contact your supplier or Edwards for advice.
Refer to
Figure 5
, items 6 or 7.
3.8
Electrical supply
WARNING
If you use inert gas purges to dilute dangerous gases to a safe level, ensure that the pump is shut
down if an inert gas supply fails.
WARNING
Leak test the system after installation and seal any leaks found to prevent leakage of dangerous
substances out of the system and leakage of air into the system.
WARNING
This equipment is suitable for Installation Category II as defined in IEC 60664-3. Connect the
system to the electrical supply through a suitably rated isolator/connector for your dry pumping
system. (Refer to
Table 6
).
WARNING
Ensure that the system and your electrical supply cable are suitably protected against earth
(ground) faults and that the earth (ground) conductor of the electrical supply cable is longer than
the phase conductors in the connector. You must fit a second protective earth (ground) conductor
(with a cross-sectional area at least equal to phase conductor size) to the protective earth (ground)
stud.
WARNING
All connections to the interface control must be double insulated or have equivalent protection.
Do not connect voltages greater than 30 V a.c. or 60 V d.c. to the control/interface connections.
If you do, the interface control will not provide protection against electric shock.
Summary of Contents for iH1000
Page 3: ......