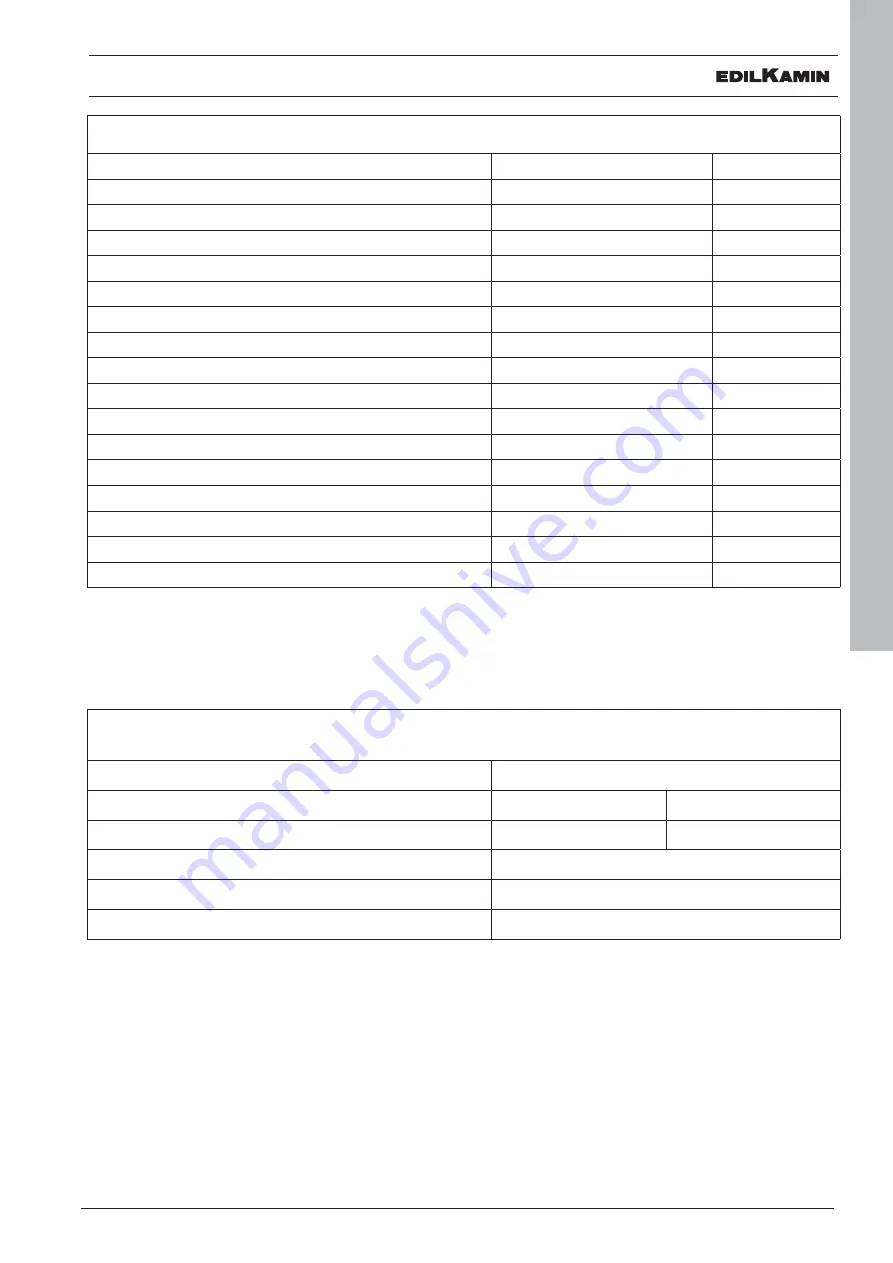
7
ENGLISH
TECHNICAL DATA as per EN 14785
Rated power
15,7
kW
Water heating power
12,6
kW
Approx. overall efficiency
92,2
%
Approx. water efficiency
81
%
CO emission (13% O
2
)
0,014
%
Max. pressure
2
bar
Operating pressure
1,5
bar
Smoke output temperature from test EN14785
130
°C
Minimum draught
12 / 5
Pa
Min./max. autonomy
8 / 27
hores
Fuel consumption min./max.*
1 / 3,5
kg/h
Hopper capacity
30
kg
Heating capacity **
410
m³
Weight including packing
201
kg
Diameter of smoke extract duct male thread
80
mm
Air intake duct diameter (male)
40
mm
Energy efficiency classes (2015-1186/1187 Regulation)
A+
TECHNICAL DATA FOR SIZING THE FLUE
which must in any case satisfy the requirements of this sheet and the installation instructions for the product
Power supply
/- 10% 50 Hz
Average power consumption
150
W
Power consumption during ignition
400
W
Remote control frequency
infrared
Protection on mains power supply
Fuse 2AT, 250 Vac 5x20
Protection on electronic circuit board
Fuse 2AT, 250 Vac 5x20
** The heatable volume is calculated based on the assumption of a heating demand of 33 Kcal/m³ hour.
*A calorific value of 4.8 kW/Kg has been used to calculate consumption.
The above data is for guidance only and was measured during certification by a notified
body.
EDILKAMIN s.p.a. reserves the right to modify the product without notification in the interests
of improvement.
TECHNICAL DATA
USER/INSTALLER