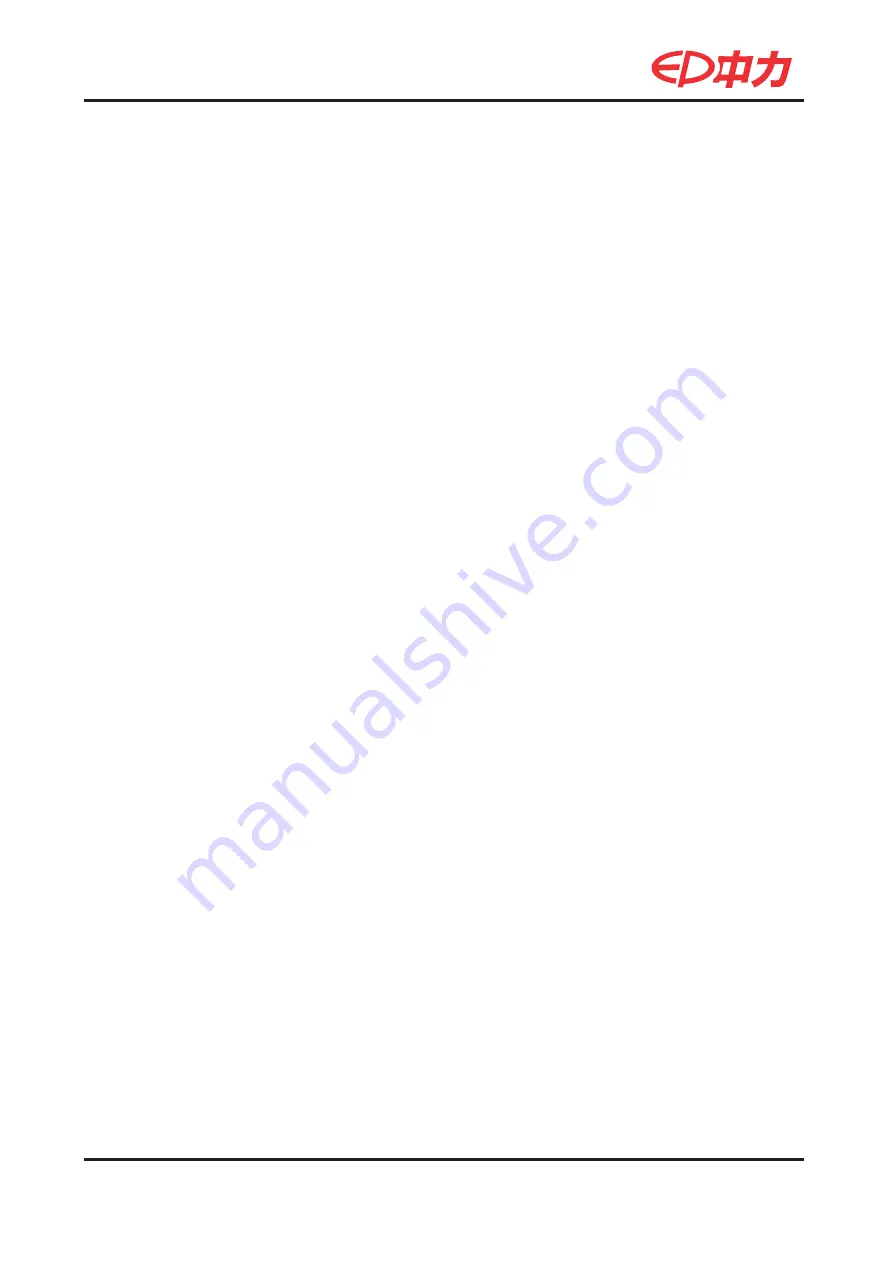
22
REV. 03/2015
3. Put the controller into the diagnostic mode by
pressing the "Arrow Keys" (Figure 01508).
Using the Navigation key, select the Faults
menu. Display the Faults menu by pressing the
Right side of the Arrow Keys. Press the Right
side of the Arrow Keys again to display the list
of System Faults. The display should indicate "No
Known Faults."
Release the brake by pulling down the steering
arm into the operating position. The controllers
LED should continue blinking a single fl ash and
the programmer should continue to indicate no
faults. If there is a problem, the LED will fl ash a
diagnostic code and the programmer will display a
diagnostic message. If you are conducting the
checkout without a programmer, look up the LED
diagnostic code in Table 1 .
When the problem has been corrected, it may be
necessary to cycle the brake in order to clear the
fault code.
4. With the brake released, select a direction and
operate the throttle. The motor should begin to
turn in the selected direction. If it does not, verify
the wiring to the forward/reverse switches and
motor. The motor should run proportionally faster
with increasing throttle. If not, refer to Paragraph
A-1.8.
5. Put the controller into the test mode by using the
Arrow Keys to select the "Monitor" menu.
Select the Monitor mode by pressing the "Right"
arrow on the Arrow Keys. Press the Arrow key
"Down" arrow to scroll down to observe the
status of the forward, reverse, brake, emergency
reverse, and mode switches. Cycle each switch in
turn, observing the programmer. Each input
should show the correct state on the programmer.
6. Check the controller's fault detection circuitry as
described in Paragraph A-1.5.
7. Take the vehicle off the blocks and drive it in a
clear area. It should have smooth acceleration
and good top speed.
8. Test the plug braking of the vehicle. The vehicle
should smoothly slow to a stop and reverse direc-
tion, with the audible plugging tone.
9. Verify that all options, such as high pedal disable
(HPD), static return to off (SRO), and anti-tiedown,
are as desired.
10. Check to see whether the emergency reverse
(belly button) feature is working correctly. Verify
that the circuit is operational by momentarily dis-
connecting one of the emergency reverse wires.
The vehicle should be disabled and a fault indi-
cated.
ELECTRICAL