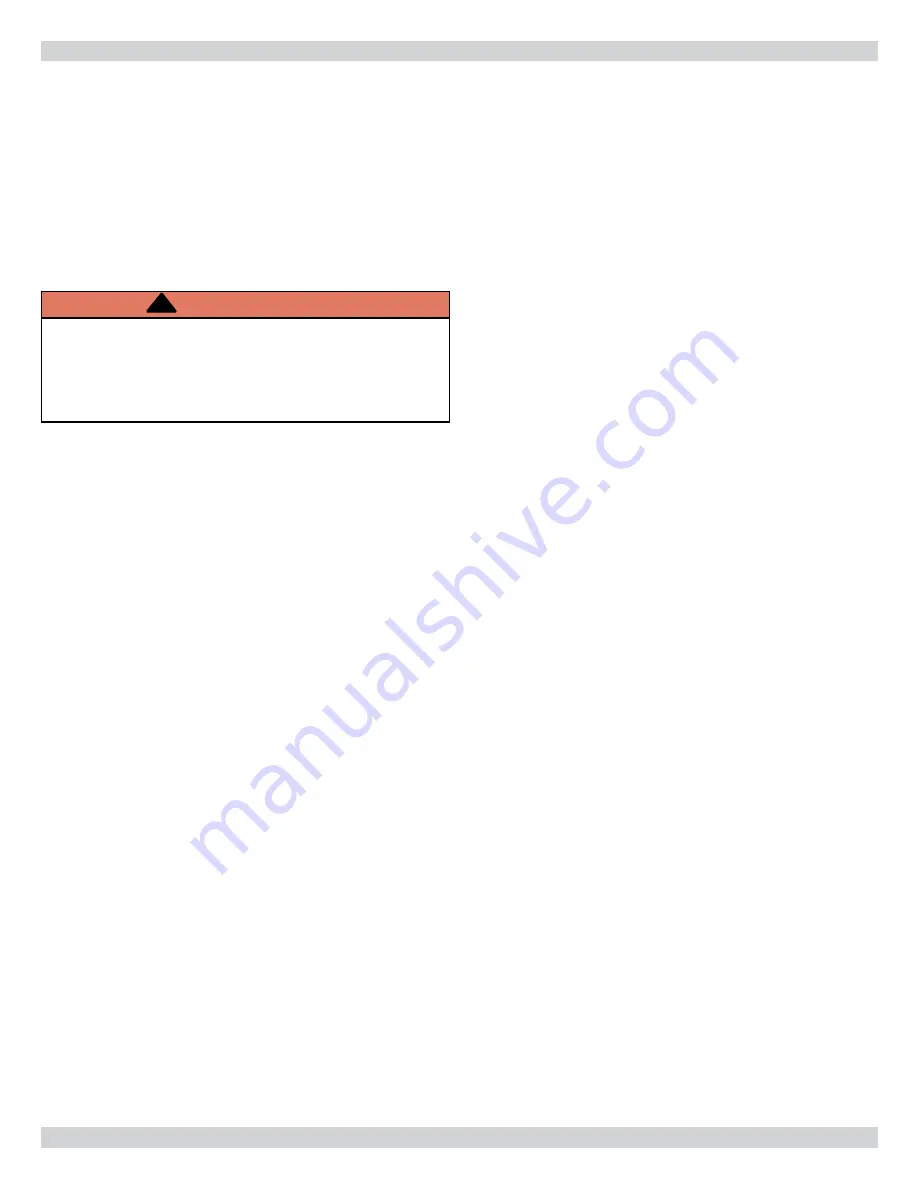
6.2 Combustion Air and Vent Pipe Requirements
• This boiler requires dedicated direct vent system.
• In direct vent system all air for combustion is taken
directly from outside atmosphere, and all fl ue products
are discharged to outside atmosphere.
• Combustion air and vent pipe connections must
terminate together in same atmospheric pressure
zone, either through roof or sidewall (roof termination
preferred). See Figures 5 and 6
for required clearances.
For proper set up of concentric vent termination see
Figure 7 and Figure 8.
WARNING
Solvent cements are combustible. Keep away from
heat, sparks, and open fl ame. Use only in well
ventilated areas. Avoid breathing in vapor or allowing
contact with skin or eyes. Failure these instructions
could result in fi re, personal injury, or death.
!
• Locate combustion air inlet as far away as possible
from swimming pool and swimming pool pump house.
• All combustion air and vent pipes must be airtight and
watertight. Combustion air and vent piping must also
terminate as shown in “Combustion Air and Vent Pipe”
section.
• Vent connections serving appliances vented by
natural draft shall not be connected into any portion
of mechanical draft systems operating under positive
pressure.
• Covering non-metallic vent pipe and fi ttings with
thermal insulation shall be prohibited.
6 - LOCATING THE BOILER
6.3 Condensate Drain Requirements
• Condensate trap provided with boiler, an additional
trap is not required and should not be used.
• Pitch condensate drain line down to fl oor drain at
minimum of ¼” per foot. External condensate pump
(not furnished) may be used if fl oor drain is not
available.
• Condensate pump must be designed for fl ue gas
condensate application.
• Wood frame or blocks may be used to raise boiler
to maintain drain pitch or to be above external
condensate pump reservoir.
• If boiler is not level, condensate drain lines will not
function properly. Adjustable feet are located on boiler
to make up for minor surface irregularities or tilt.
• 115 volt AC receptacle provided on control panel to
provide power for external condensate pump if used.
6.4 Removal of Existing Boiler From Common
Vent System
When an existing boiler is removed from a common
venting system, the common venting system is likely to be
too large for proper venting of the appliances remaining
connected to it. At the time of removal of an existing boiler,
the following steps shall be followed with each appliance
remaining connected to the common venting system
placed in operation, while the other appliances remaining
connected to the common venting system are not in
operation.
1.
Seal any unused openings in the common venting
system.
2.
Visually inspect the venting system for proper size and
horizontal pitch and determine there is no blockage, or
restrictions, leakage, corrosion and other defi ciencies
which could cause an unsafe condition.
3.
In-so-far as is practical, close all building doors and
windows and all doors between the space in which the
appliances remaining connected to the common venting
system are located and other spaces of the building.
Turn on clothes dryer and any appliance not connected
to the common venting system. Turn on any exhaust
fans, such as range hoods and bathroom exhaust, so
they will operate at maximum speed. Do not operate a
summer exhaust fan. Close fi re dampers.
4.
Place in operation the appliance being inspected.
Follow the lighting instructions. Adjust thermostat so
appliances will operate continuously.
5.
Test for spillage at the draft hood relief opening after 5
minutes of main burner operation. Use the fl ame of a
match or candle, or the smoke from a cigarette, cigar
or pipe.
6.
After it has been determined that each appliance
remaining connected to the common venting system
properly vents when tested as outlined above, return
doors, windows, exhaust fans, fi re place dampers,
and any other gas-burning appliance to their previous
condition of use.
7.
Any improper operation of the common venting system
should be corrected so the installation conforms with
the National Fuel Code, NFPA-54/ANSI -Z223.1 and/or
the Natural Gas and Propane Installation Code, CAN/
CSA B149.1. When re-sizing any portion of common
venting system, common venting system should be re-
sized to approach minimum size as determined using
appropriate tables in Chapter 13 of the National Fuel
Gas Code, NFPA-54/ANSI- Z223.1 and/or the Natural
Gas and Propane Installation Code, CAN/CSA B149.1.
8
Summary of Contents for Olsen OQ95M-200
Page 2: ...1 DIMENSIONS OPENING FOR SAFETY RELIEF VALVE DISCHARGE PIPE 30 785mm 39 1 1m 18 458mm 2 ...
Page 27: ...APPENDIX A BOILER PIPING AND WIRING Electrical Wiring Diagram 27 ...
Page 49: ...49 NOTES ...
Page 50: ...50 NOTES ...
Page 51: ...51 Company Address Phone Company Name Tech Initials Service Performed Date SERVICE RECORD ...
Page 52: ...ECR International 2201 Dwyer Avenue Utica NY 13501 web site www ecrinternational com ...