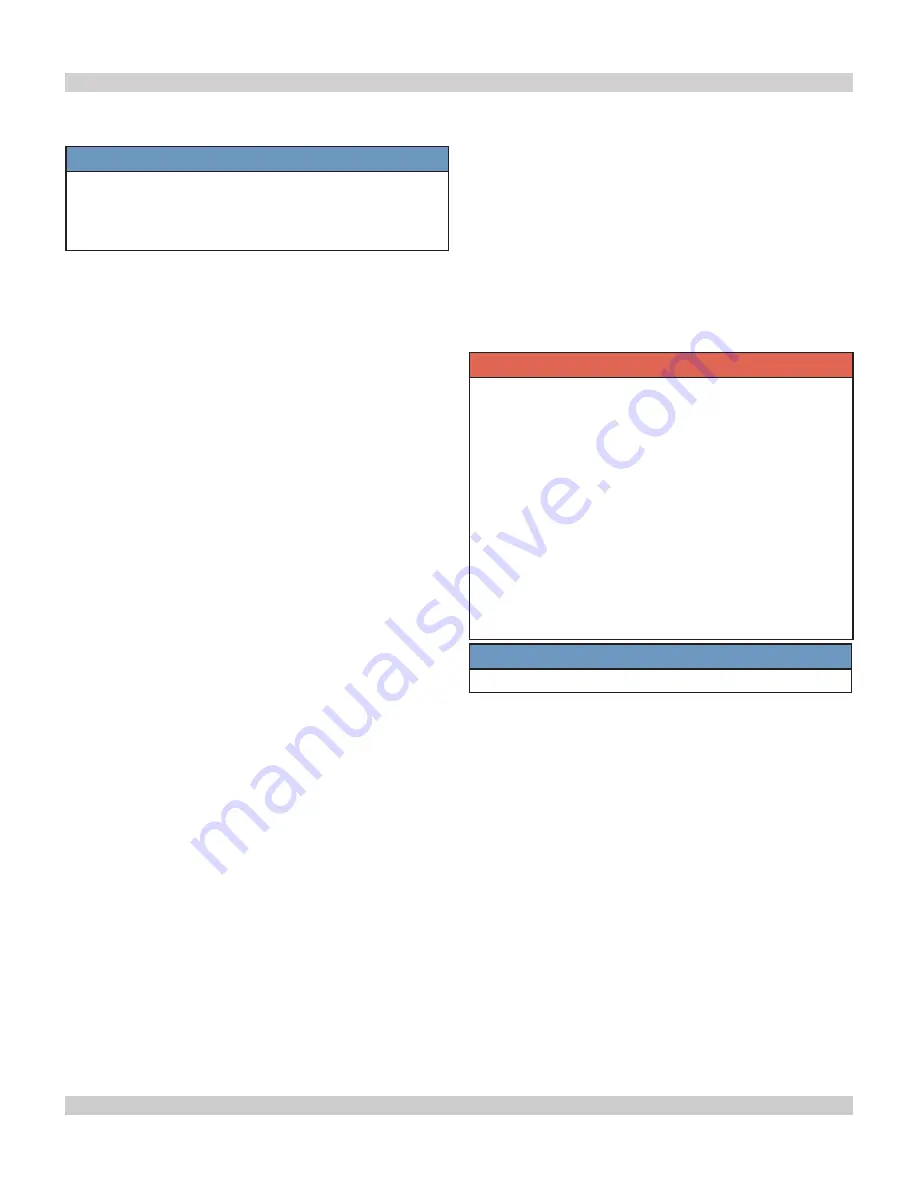
11
5 - HYDRONIC PIPING
5.1
General
• Install piping in accordance with authority having jurisdiction.
NOTICE
Use two (2) wrenches when tightening and
fi
tting
pipe to boiler's threaded
fi
ttings. Boiler's internal
piping can be damaged if subjected to excessive
torque.
• Support system piping and safety relief valve discharge
piping. Boiler's internal piping and wall mount bracket
can be damaged if subjected to excessive weight.
• Size central heating pump (and domestic hot water
pump, if used) for system requirements only. Internal
heat exchanger pump compensates for pressure drop
through boiler internal piping and heat exchanger.
• Thoroughly clean and
fl
ush system before connecting to boiler.
• If oil is present in system water, use approved detergent to
wash system.
• Flush system to remove any solid objects such as metal chips,
fi
bers, or Te
fl
on tape, etc.
5.2 Water System Characteristics
• Water in the heating system must have protection of
metallic materials against corrosion.
• Filling water and subsequent replenishing, must be
clear, with hardness under 150 ppm CaCO3,
A. treated with approved conditioning chemicals
to ensure prevention of corrosion and attack on
metals and plastics, that gases do not form,
B. and bacterial or microbial masses do not proliferate
in low temperature systems.
• Hardness exceeding 150 ppm CaCO3, appropriate water
softening treatment and/or use of suitable anti-fouling
agents must be provided.
Water contained in the system must be checked at least
yearly and have:
A. pH above 7 and under 8.5 (under 8 with presence
of components in aluminum or light alloys),
B. iron content (Fe) less than 0.5 mg/l,
C. copper content (Cu) less than 0.1 mg/l,
D. total content of chlorides, nitrates and sulfates less
than 50mg/l,
E. must contain conditioning chemicals in
concentration suf
fi
cient to protect system for a
year.
There must be no microbial or bacterial loads in low
temperature systems.
Conditioners, additives, inhibitors and anti-freeze
fl
uids can
be used only if manufacturer guarantees they are suitable
for use in heating systems and they do not cause damage
to heat exchanger or other components and/or materials of
boiler and system.
Use of generic chemicals not speci
fi
cally suitable for use in
heating systems and/or incompatible with boiler materials
and system is forbidden.
Conditioning chemicals must ensure complete deoxygenation
of water and contain speci
fi
c protective agents for yellow
metals (copper and its alloys), anti-fouling agents for
limescale at least up to 150 ppm CaCO3, pH neutral
stabilizers and, in low temperature systems, speci
fi
c biocides
for use in heating systems.
In systems with continuous intake of oxygen (e.g.
fl
oor
systems without anti-diffusion pipes, open expansion
vessels), or intermittent (e.g. in case of frequent
replenishing), a separator must be provided. Regarding
domestic hot water (DHW), no type of treatment which
could prevent its possible food use can be provided for.
WARNING
• Poison hazard. Ethylene glycol is toxic. Do not
use ethylene glycol.
• Never use automotive or standard glycol antifreeze,
even ethylene glycol made for hydronic systems.
• Ethylene glycol can attack gaskets and seals used
in hydronic systems.
• Use only inhibited propylene glycol solutions
certi
fi
ed by
fl
uid manufacturer as acceptable for
use with closed water heating system.
• Thoroughly clean and
fl
ush any system that used
glycol before installing new Boiler.
• Provide user with Material Safety Data Sheet
(MSDS) on
fl
uid used.
NOTICE
Do not expose boiler to freezing temperatures.
5.3 Special Conditions
• System piping exposed to freezing conditions: Use
inhibited propylene glycol solutions certi
fi
ed by
fl
uid
manufacturer for use with closed water heating system.
Do not use automotive or ethylene glycol.
• Boiler installed above radiation level (or as required by
authority having jurisdiction) shall have low water cutoff
protection.
• Boiler used in connection with refrigeration system.
Install piping in parallel with boiler, with appropriate
valves to prevent chilled medium from entering boiler.
Summary of Contents for CHB-100
Page 6: ...Figure 2 Component Listing 6 3 GENERAL VIEW AND MAIN COMPONENTS ...
Page 33: ...33 12 RATINGS AND CAPACITIES ...
Page 38: ...KEY Part Number Description Qty A01 FE3980B830 CASING CTR 1 38 REPAIR PARTS LIST CHB 100 ...
Page 40: ...40 REPAIR PARTS LIST CHB 100 ...
Page 42: ...42 REPAIR PARTS LIST CHB 100 ...
Page 44: ...KEY Part Number Description Qty A01 FE3980B830 CASING CTR 1 44 REPAIR PARTS LIST CHB 130 ...
Page 46: ...46 REPAIR PARTS LIST CHB 130 ...
Page 48: ...48 REPAIR PARTS LIST CHB 130 ...
Page 50: ...NOTES 50 ...
Page 51: ...NOTES 51 ...
Page 52: ...ECR International Inc 2201 Dwyer Avenue Utica NY 13501 web site www ecrinternational com ...