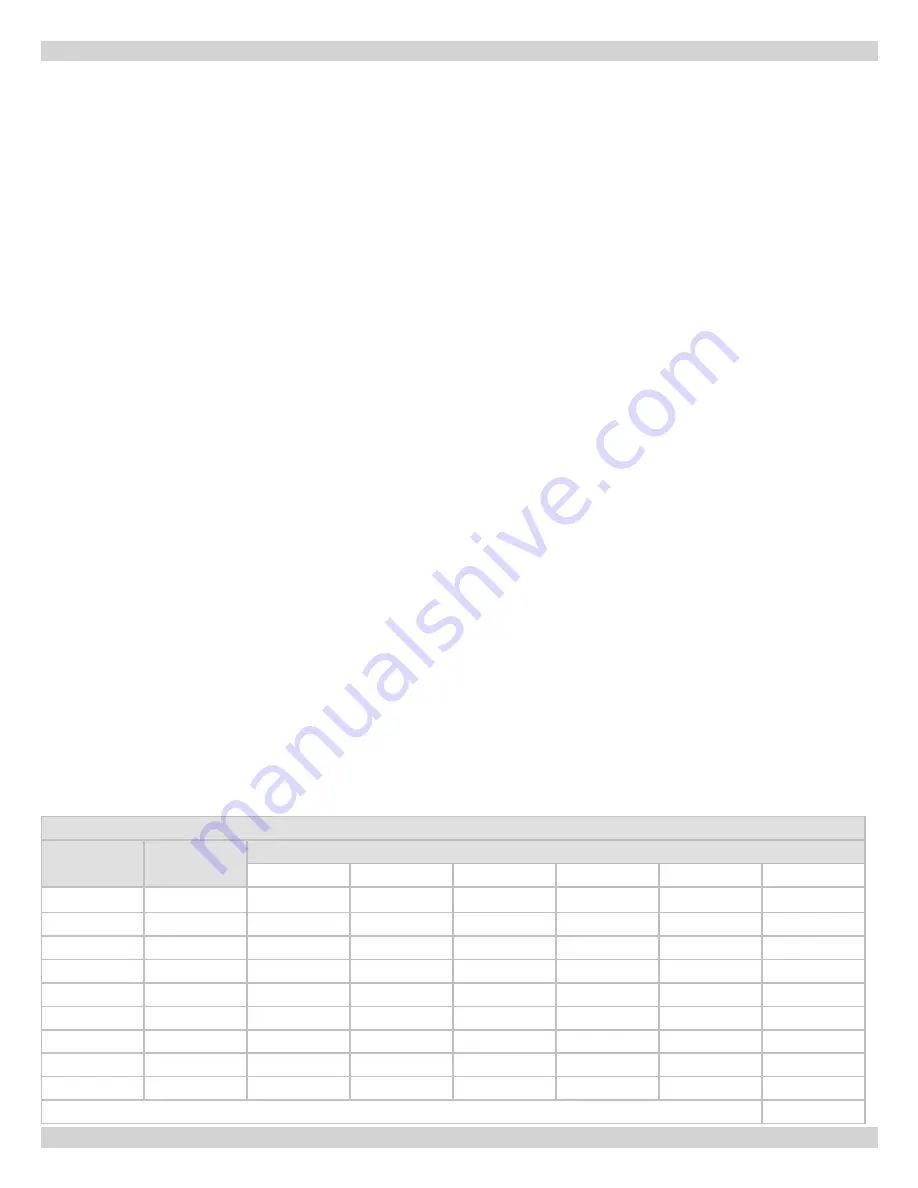
7
Table 3 - Minimum Room Volume, Indoor Air Only*
Input Mbh
Standard
Method
Known Air Infiltration Rate Method (Air Changes Per Hour)
0.1
0.2
0.3
0.4
0.5
0.6
45
2250
9450
4725
3150
2363
1890
1575
70
3500
14700
7350
4900
3675
2940
2450
96
4800
20160
10080
6720
5040
4032
3360
120
6000
25200
12600
8400
6300
5040
4200
145
7250
30450
15225
10150
7613
6090
5075
170
8500
35700
17850
11900
8925
7140
5950
195
9750
40950
20475
13650
10238
8190
6825
245
12250
51450
25725
17150
12863
10290
8575
295
14750
61950
30975
20650
15488
12390
10325
* Table values based on boiler only. Add volume for any additional appliances.
4 - VENTILATION & COMBUSTION AIR
Provide combustion air and ventilation air in accordance
with the section “Air for Combustion and Ventilation,” of the
National Fuel Gas Code, ANSI Z223.1/NFPA 54, or Sections
8.2, 8.3 or 8.4 of Natural Gas and Propane Installation
Code, CAN/CSA B149.1, or applicable provisions of local
building codes.
Provide make-up air where exhaust fans, clothes dryers,
and kitchen ventilation equipment interfere with proper
operation.
National Fuel Gas Code recognizes several methods
of obtaining adequate ventilation and combustion air.
Requirements of the authority having jurisdiction may
override these methods.
• Engineered Installations. Must be approved by
authority having jurisdictions.
• Mechanical Air Supply. Provide minimum of 0.35
cfm per Mbh for all appliances located within space.
Additional requirements where exhaust fans installed.
Interlock each appliance to mechanical air supply
system to prevent main burner operation when
mechanical air supply system not operating.
• All Indoor Air. Calculate minimum volume for all
appliances in space. Use a different method if
minimum volume not available.
о
Standard Method. Cannot be used if known air
infiltration rate is less than 0.40 air changes per
hour. See Table 3 for space with boiler only. Use
equation for multiple appliances.
Volume ≥ 50 ft
3
x Total Input [Mbh]
о
Known Air Infiltration Rate. See Table 3 for
space with boiler only. Use equation for multiple
appliances. Do not use an air infiltration rate
(ACH) greater than 0.60.
Volume ≥ 21 ft
3
/ACH x Total Input [Mbh]
о
Refer to National Fuel Gas Code for opening
requirements between connection indoor spaces.
• All Outdoor Air. Provide permanent opening(s)
communicating directly or by ducts with outdoors.
о
Two Permanent Opening Method. Provide opening
commencing within 12 inches of top and second
opening commencing within 12 inches of bottom
enclosure.
Direct communication with outdoors or
communicating through vertical ducts. Provide
minimum free area of 1 in
2
per 4 Mbh of total
input rating of all appliances in enclosure.
Communicating through horizontal ducts.
Provide minimum free area of 1 in
2
per 2
Mbh of total input rating of all appliances in
enclosure.
о
One Permanent Opening Method. Provide opening
commencing within 12 inches of top of enclosure.
Provide minimum clearance of 1 inch on sides
and back and 6 inches on front of boiler (does not
supersede clearance to combustible materials).
о
Combination Indoor and Outdoor Air. Refer to
National Fuel Gas Code for additional requirements
for louvers, grilles, screens and air ducts.
• Combination Indoor and Outdoor Air. Refer to
National Fuel Gas Code for application information.
National Gas and Propane Installation Code Requires
providing air supply in accordance with:
• Section 8.2 and 8.3 when combination of appliances
has a total input of up to and including 400 Mbh (120
kW).
• Section 8.4 when combination of appliances has total
input exceeding 400 Mbh (120 kW).
• Refer to Natural Gas and Propane Installation Code
for specific air supply requirements for enclosure
or structure where boiler is installed, including air
supply openings and ducts.